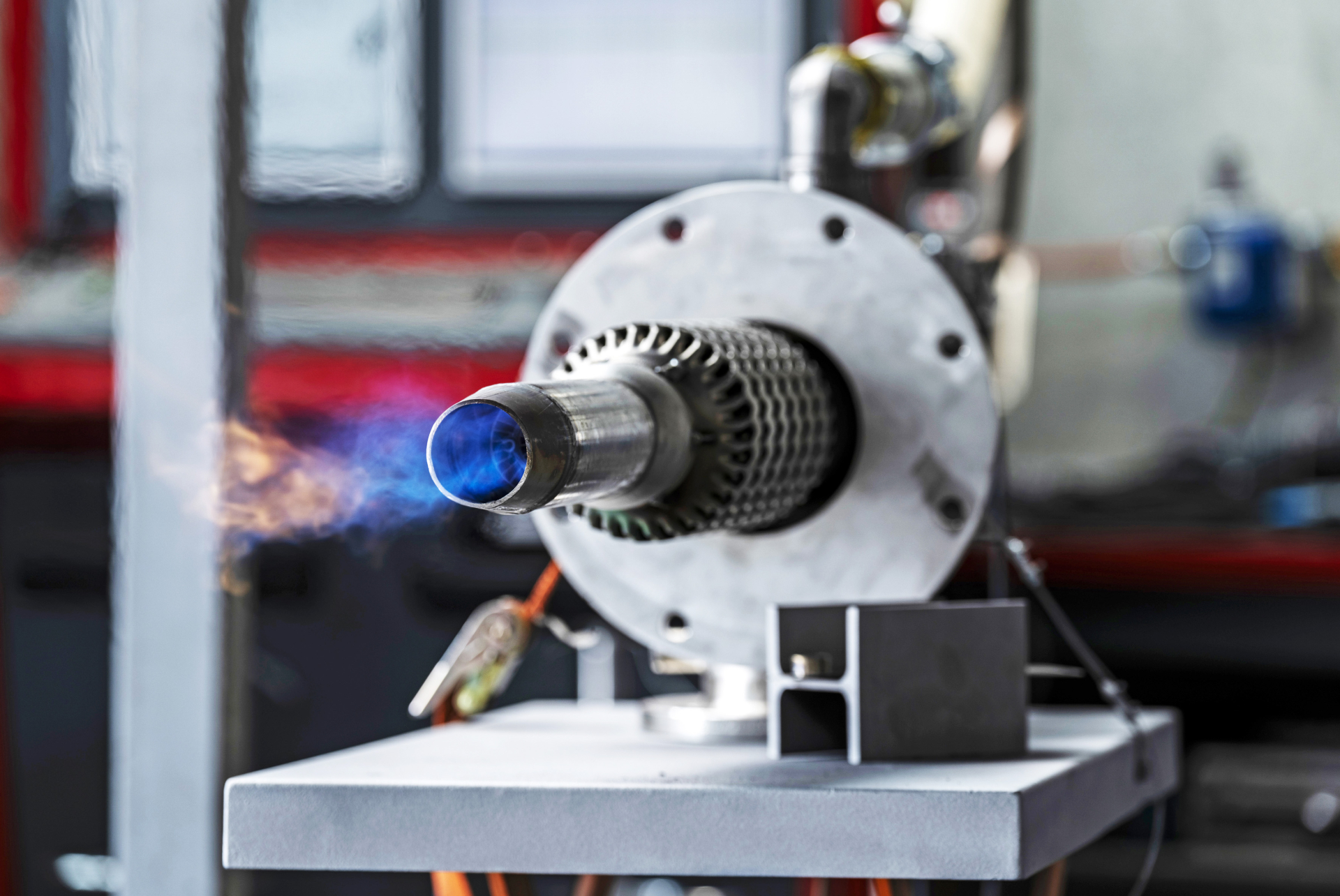
Nominee 2023
Resilience for the gas supply
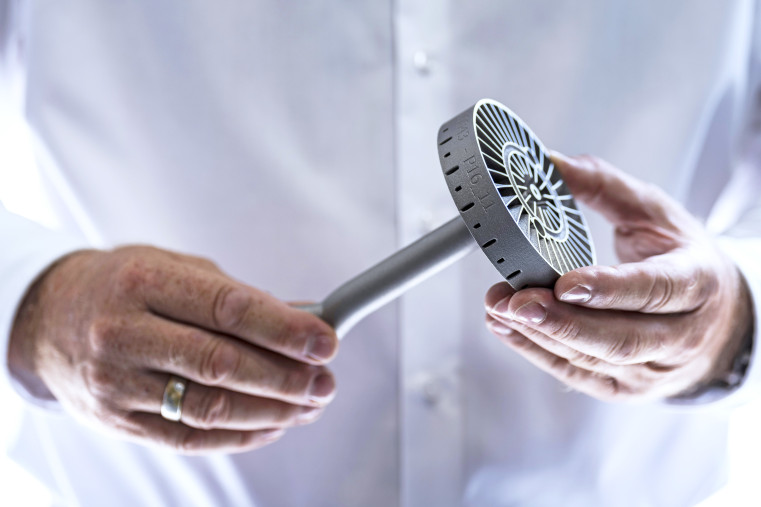
Jens te Kaat, Bernd-Henning Feller and Dan-Adrian Moldovan have designed a system that can provide the basis for this. The three nominees developed a burner capable of supplying the heat needed for different industrial applications much more efficiently from natural gas and thus at a much lower cost than conventional units. In this way, emissions of CO2 that are harmful to the climate as well as nitrogen compounds that damage both the environment and health can be greatly reduced.
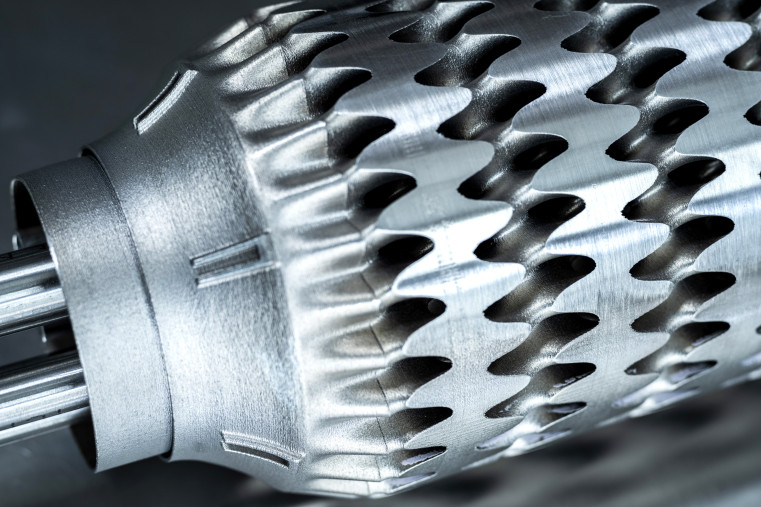
The system also has the option of using not only natural gas but other gases as fuel – specifically, hydrogen that is considered a key element for the ongoing energy transition. Jens te Kaat is Managing Director of Kueppers Solutions in Dortmund, Bernd-Henning Feller is development engineer and a member of the management board, Dan-Adrian Moldovan heads the development and simulation division at the company.
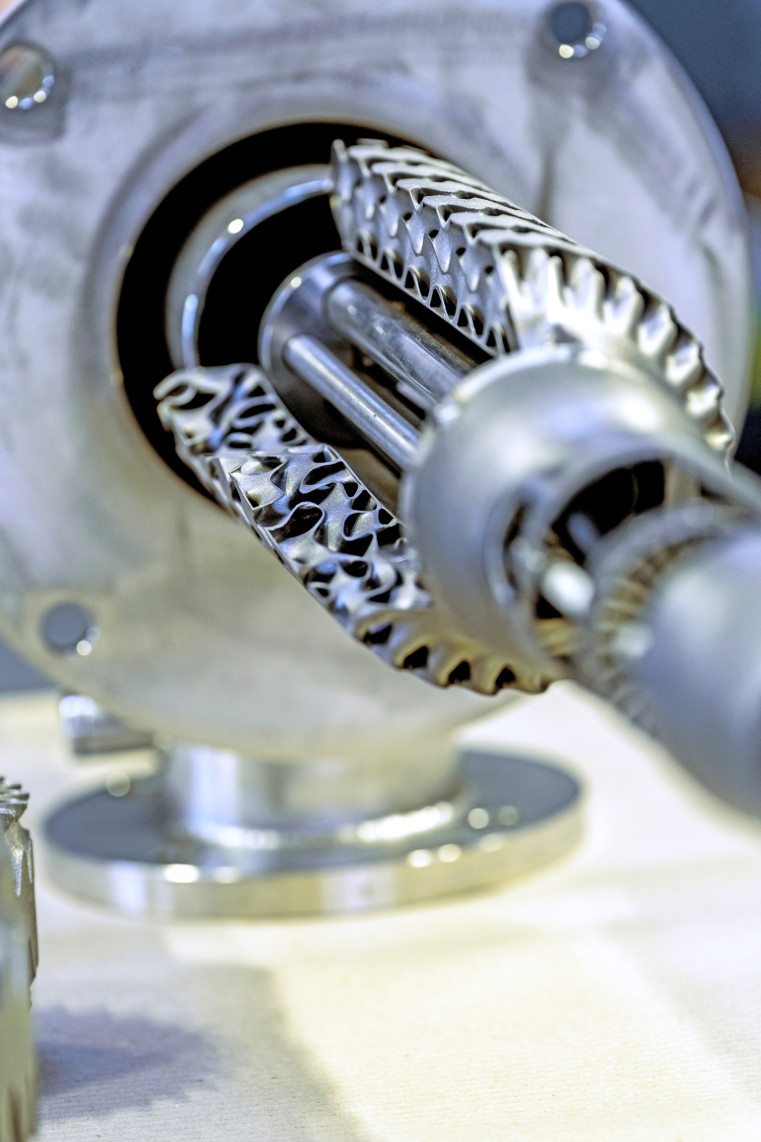
Thermal processing facilities are enclosed industrial furnaces in which products or materials are manufactured or heat-treated at high temperatures. They are essential in many sectors. Vast amounts of process heat are needed by cement factories, glassworks, chemical production plants and in the production of steel. Up to now natural gas was usually used to generate the heat. The companies that run on natural gas are among the largest purchasers of this fossil resource, and not just in Germany. If natural gas were not available in sufficient quantities, this could lead to production downtimes and great economic damage. For that reason alone it would be wise to keep demand for fuel for process heat as low as possible. A highly efficient burner technology can provide the basis for this. In addition, lower natural gas consumption also reduces climate-damaging emissions produced by combustion. This would be another important contribution to climate protection.
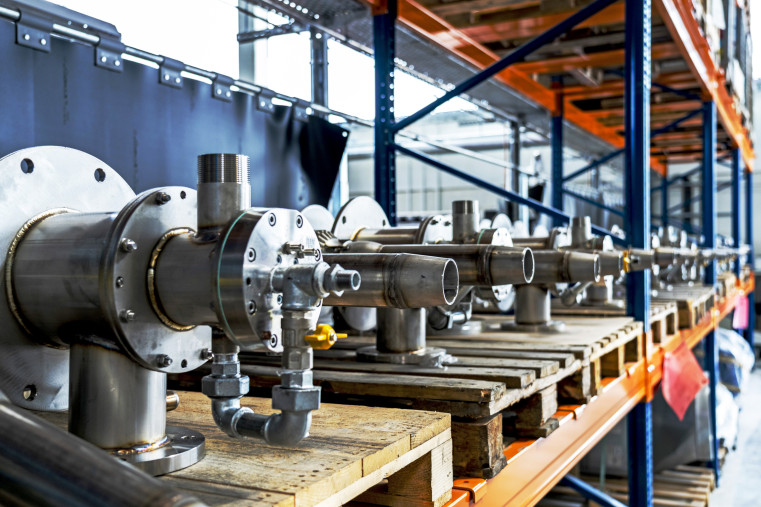
With the iRecu® recuperator burner, the three nominees have developed a system suitable for use in most industrial applications in the thermal processing industry. Where it is used, it lowers demand for natural gas – and thus CO2 emissions – by 12 to 50 percent compared to conventional burners. It also reduces emissions of nitrogen oxides, NOx in shorthand chemical notation, by more than half. These chemical compounds which are formed in considerable amounts by the generation of thermal process heat in normal burners are harmful to the environment and health.
More Details
Resume
Dipl.-Ing. (FH) Jens te Kaat
- 03.03.1966
- Born in Münster, Westphalia
- 1985
- Abitur (university entrance qualification) at the Aufbaugymnasium Dortmund
- 1986 -1988
- Apprenticeship as a car mechanic
- 1988 - 1991
- Degree course in mechanical engineering, majoring in production technology, at Dortmund University of Applied Sciences and Arts
- 1991 - 1998
- Production engineer, later deputy production manager at Friedrich Wilhelm Schwing GmbH, Baumaschinenfabriken, Herne
- 1999 – 2000
- Production manager at Auroflex GmbH & Co KG, Sprockhövel
- 2001 - 2015
- Managing director, later shareholder and board member at Böcker AG, Werne
- Since 2016
- Shareholder and managing director at Kueppers Solutions GmbH, Dortmund
Memberships
- Spokesperson of the Executive Board of Netzwerk Industrie RuhrOst e.V.
Münchener Kreis - Expert Panel of Construction Equipment e.V.
Monitoring committee of the "ProduktionNRW" cluster
Westfälischer Indutrieklub e.V.
Awards
- 2019
- TOP100 Innovator: "Additively manufactured gas/air mixing unit for optimised combustion"
- 2019
- Winner of the Efficiency Award NRW: "Innovative and resource-saving 3D-printed mixing unit for gas burners".
- 2020
- Finalist Innovation Award of the German Gas Industry, Category: Research & Development
- 2022
- Finalist Innovation Award of the German Gas Industry, Category: Efficient application technology
- 2022
- Winner of the Innovation Award for Climate and Environment "iRecu® - Efficient thermoprocessing plants with H2"
Patents
- Ten patent applications
Publications
- Various subject-related publications and lectures at conferences
Bernd-Henning Feller, M.Sc.
- 27.04.1996
- Born in Dorsten
- 2015
- Abitur at the St. Ursula Gymnasium Dorsten
- 2015 – 2021
- Studies in mechanical engineering at the Ruhr University Bochum, degree: M. Sc.
- 2018 – 2019
- Working student at the Gas- und Wärme-Institut Essen e.V.
- 2019 – 2021
- Project engineer at Kueppers Solutions GmbH; focus: Experimental development and project management in the area of new business fields
- 2021 – 2023
- Technical Managing Director (overall authorised signatory) of Kueppers Solutions GmbH; focus: management of the technical business area and the research and development area
- Juni 2023
- Reduction of the operative business at Kueppers Solutions GmbH and start of the doctorate to obtain the degree of Dr.-Ing. at the Gas- und Wärme-Institut Essen e.V.
- Since 2023
- Project manager in the industrial and firing technology department of the Gas- und Wärme-Institut Essen e.V.
Awards
- 2019
- TOP100 Innovator: "Additively manufactured gas/air mixing unit for optimised combustion"
- 2019
- Winner of the Efficiency Award NRW: "Innovative and resource-saving 3D-printed mixing unit for gas burners"
- 2020
- Finalist Innovation Award of the German Gas Industry, Category: research & development
- 2022
- Finalist Innovation Award of the German Gas Industry, Category: efficient application technology
- 2022
- Winner of the Innovation Award for Climate and Environment: "iRecu® - Efficient thermoprocessing plants with H2"
Patents
- Two patent applications
Publications
- Various technical publications
Dan-Adrian Moldovan, M.Sc.
- 02.01.1988
- born in Bucharest
- 2008
- High school graduation (Abitur), Bert-Brecht-Gymnasium in Dortmund, Germany
- 2008 - 2019
- Master’s Degree in Mechanical Engineering (M.Sc.), Ruhr University Bochum, Germany
- 2018
- Internship at Kueppers-Solutions GmbH
- Since 2019
- Development and simulations engineer at Kueppers-Solutions GmbH,Responsible for designing and CFD simulation of the additive manufactured gas/air mixing unit and recuperator.
Scholarships
- 2017
- Deutscher Akademischer Austauschdienst (DAAD), German Academic Exchange Service
Awards
- 2017 – 2018
- Academic education and further training in the People's Republic of China as part of a project of the Sino-German University College (CDHK) at Tongji University in Shanghai
- 2019
- TOP100 Innovator: A mixing unit manufactured through metallic 3D printing for combustion optimization and reduction of nitrogen oxide emissions.
- 2019
- Efficiency Award NRW: Innovative Design, Recyclability, and Nitrogen Oxide Reduction.
- 2020
- Finalist of the Innovation Award of the German Gas Industry, Category: Research and Development
- 2022
- Innovation Award for Climate and Environment: iRecu® - H2-Ready Series Burner with Optimized Heat Recovery
- 2022
- Finalist of the Innovation Award of the German Gas Industry, Category: Efficient Application Technology
Patents
- 2020
- Co-inventor of two filed patents/patent application
Publications
- 2020
- Publication: Process Heat, Recuperator Burner from 3D Printing for Efficient Heat Recovery
Contact
Coordination and Press
Domenik Prüßmann
Geschäftsleitung / Prokurist
Kueppers Solutions GmbH
Robert-Schuman-Str. 6
Phone: +49 (0) 209 / 36 17 22 168
Mobil: +49 (0) 151 / 72 97 58 21
E-Mail: domenik.pruessmann@kueppers-solutions.de
Web: www.kueppers-solutions.de
Spokesperson
Jens te Kaat
Geschäftsführer
Kueppers Solutions GmbH
Robert-Schuman-Str. 6
Phone: +49 (0) 209 / 36 17 22 140
Mobil: +49 (0) 160 / 53 43 985
E-Mail: jens.tekaat@kueppers-solutions.de
Web: www.kueppers-solutions.de
A description provided by the institutes and companies regarding their nominated projects
Resilience for the gas supply – 3D Recu burner lowers natural gas consumption and opens up a future for hydrogen in industry
Increase efficiency immediately, in future also with hydrogen. The energy demand of German industry accounts for about 30 % of Germany's total energy demand. A large part of this energy is provided by fossil natural gas. It is used, for example, to heat hydraulic pipes, to produce packaging sheet for biscuit tins or to roast our breakfast coffee. In this context, industry offers good access to a few, usually large consumers, in contrast to the small-scale nature of private households or the transport sector, for example. The Ukraine war has worsened the availability of natural gas in Germany, and in the course of the energy transition fossil gas must be replaced quickly by green gases anyway. Hydrogen is a promising alternative, but requires technical adjustments in current industrial plants, which typically remain in operation for 30 to 50 years.
Natural gas savings make it possible to get started. With the iRecu, the developers at Kueppers Solutions have created a system that makes existing industrial heat treatment plants more energy-efficient by means of an innovative heat exchanger. The heat exchangers, also known as recuperators, enable an immediate natural gas and thus cost saving of over 10 %, which immediately refinances a plant conversion. At the same time, the introduction of hydrogen is prepared, as the plant can be operated flexibly with both natural gas and hydrogen after the conversion. Thanks to customised burners, there is usually no need to replace other components, which minimises the conversion effort and increases acceptance - a principle comparable to replacing light bulbs with energy-saving lamps, which saves costs, energy and resources.
Become H2-ready and invest safely in the future. A conversion to the iRecu makes plants "hydrogen-ready" at the same time - regardless of whether green hydrogen is already available or not yet. The different combustion characteristics of natural gas and hydrogen normally require a plant conversion. However, the iRecu offers the flexibility to switch back and forth between fuels without conversion, comparable to an electric hybrid car. In this way, industrial companies avoid standstills and expensive conversions when hydrogen is not available - the motto is: switching instead of shutting down.
CO2 , NOx and other pollutants. The pollutant "nitrogen oxide" is produced every time a fuel is burned hot with the oxidant air. The higher the temperature during combustion, the more the nitrogen in the air reacts with the oxygen and forms nitrogen oxides. With this thermally induced NOx there is a conflict of goals: On the one hand, one wants to optimise the combustion, i.e. usually make it hotter. This is done, for example, through the improved heat exchanger, which saves fuel and thus CO2 , but increases NOx emissions. Since hydrogen burns hotter than natural gas, NOx emissions increase again significantly with the conversion. This must be avoided, as nitrogen oxides are harmful to the environment and health.
To reduce the formation of nitrogen oxides, the gas-air mixing unit is designed with separate channels for natural gas and hydrogen for optimal combustion of the respective fuel. The entire fuel gas is to react and thus the energy stored in the fuel gas is to be utilised. At the same time, however, pollutant emissions, especially nitrogen oxides, are to be minimised. For this purpose, natural gas and hydrogen are fed to the combustion system via two separate channel systems, each with adapted flow rates and mixing ratios. In addition, the speed of the incoming combustion air, which is greatly accelerated by the heating, is used to drive a jet pump. This ensures a strong mixing of the inflowing gas mixture with exhaust gas even before the mixture is fed to the combustion. The fuel gas is "diluted" with hot exhaust gas, which reduces nitrogen oxide emissions. The good thing is that this dilution is even more effective with hydrogen combustion than with natural gas. Thus, in addition to the NOx increase due to the improved heat exchanger, the increase due to the hotter combustion of hydrogen is also compensated.
Digital value creation of tomorrow. The production of the iRecu is made possible by a largely digitalised value chain: The heat exchanger uses mathematically complex TPMS structures that can only be calculated using computer programmes. Understanding these structures, manufacturing them economically and in a process-safe manner and designing them in such a way that they optimally meet the requirements of the respective system was a major challenge for the developers at Kueppers Solutions. In total, more than four years of intensive development work were necessary until the delivery of the first recuperators could begin in October 2022. These TPMS structures (Triply Periodic Minimal Surface) can only be produced with the help of 3D printing and were therefore not possible to manufacture a few years ago. The optimised flow guidance within the structure means that the energy in the hot exhaust gas is transferred to the combustion air flowing into the process better than the current state of the art allows. Otherwise, the energy in the flue gas - if it is not transferred to the combustion air - is released into the environment via the chimney and remains unused.
The gas-air mixing unit with its separate channels can also only be produced using metallic 3D printing and is calculated beforehand using computer programmes. The last essential component, the jet pump, could theoretically also be produced conventionally. However, here too, the best properties are achieved by printing this component. A lot of digital work is necessary in advance before the "Print" button can finally be pressed.
The 3-D printer essentially produces these parts automatically and appropriately for the application. In the printing process - if everything has been calculated correctly beforehand - different components can be built on the 3-D printer without additional effort, quasi as custom-made production in series production. The effort here lies mainly in the digital adaptation of the print files. The production process of the iRecu is thus a blueprint for the digital production of the future, in which the resulting customised product is manufactured in a highly automated way exactly according to the customer's requirements. This digital value chain enables Kueppers Solutions to be the technology leader in the production of recuperators today.
The industrial energy transition begins today. The iRecu was launched at the end of 2022. Convincing results have already been achieved in the first converted plants: at Mannesmann Precision Tubes in Hamm, 14.2 %, and at thyssenkrupp Rasselstein in Andernach, 12.9 % energy could be saved, without any additional plant engineering effort. With the dual-fuel recuperative burner iRecu, a direct and immediate contribution can be made to achieving climate targets and maintaining Germany as a business location.
Kueppers Solutions GmbH, Dortmund
Kueppers Solutions GmbH, based in Dortmund, was created from the "Heat Technology Division" of Küppersbusch AG in 2016. Its focus is on recuperator burners produced using metallic 3D printing and components for increasing efficiency in thermoprocessing technology.
Contact Dipl.-Ing. Jens te Kaat, Managing Partner, M. Sc. Bernd-Henning Feller, M. Sc. Dan-Adrian Moldovan
Further information: www. kueppers-solutions.de/
The right to nominate outstanding achievements for the Deutscher Zukunftspreis is incumbent on leading German institutions in science and industry as well as foundations. The project "Resilience for the gas supply – 3D Recu burner lowers natural gas consumption and opens up a future for hydrogen in industry” was submitted by Deutsche Akademie der Technikwissenschaften e.V..
Federal President Frank Walter Steinmeier will present the Deutscher Zukunftspreis to one of the three nominated teams on November 22, 2023.
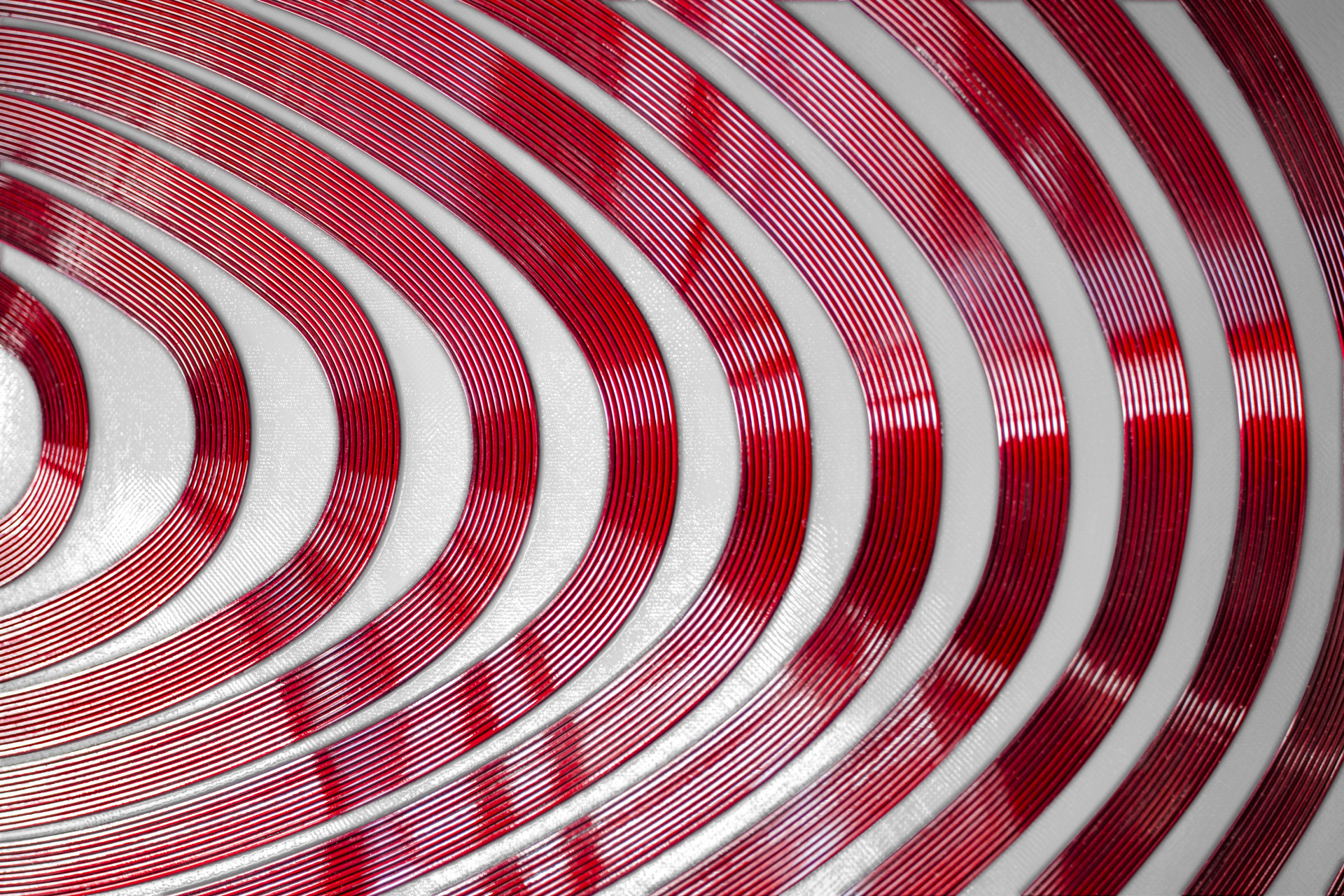