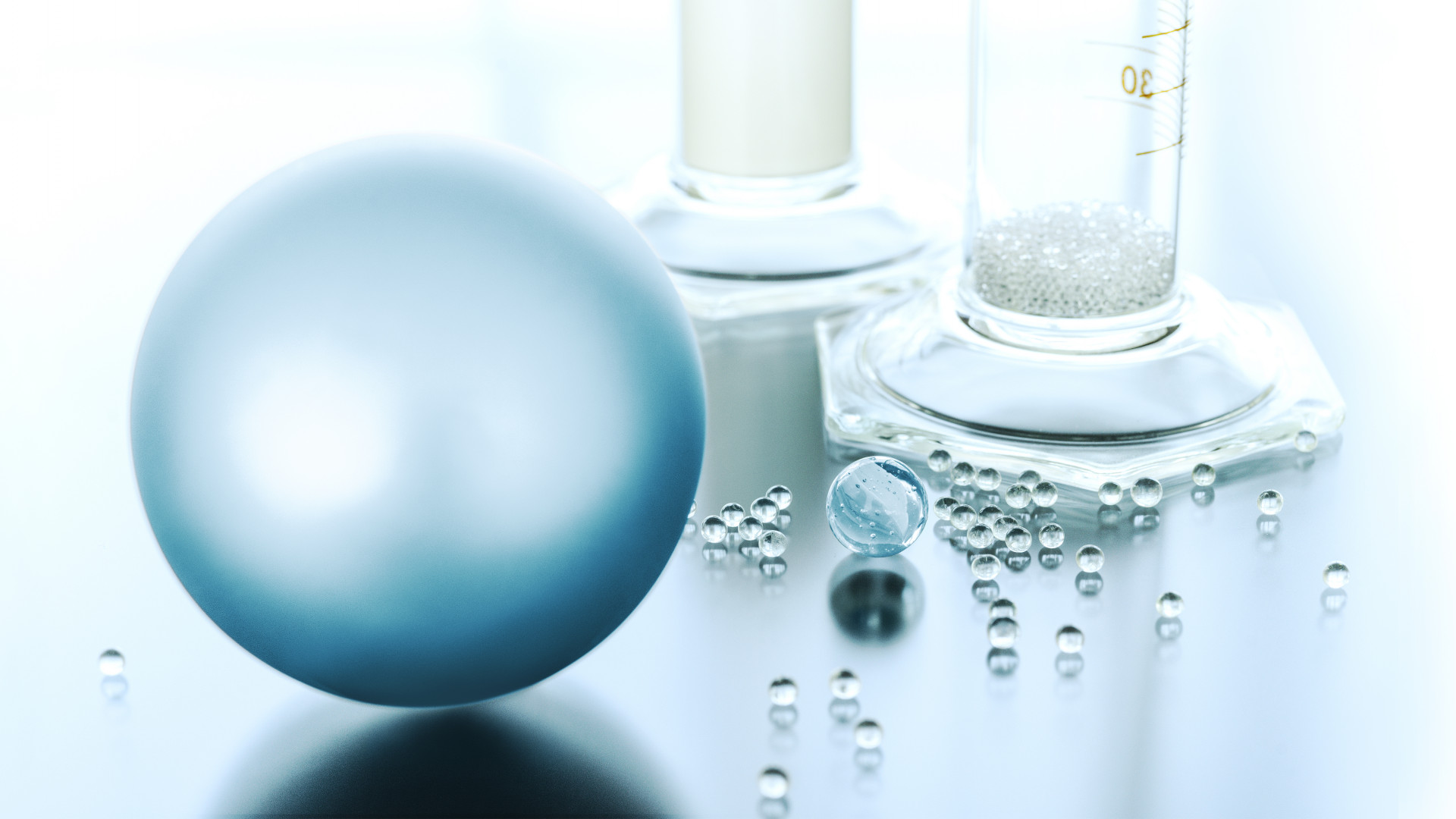
Nominee 2020
Glass-Bubble Insulation
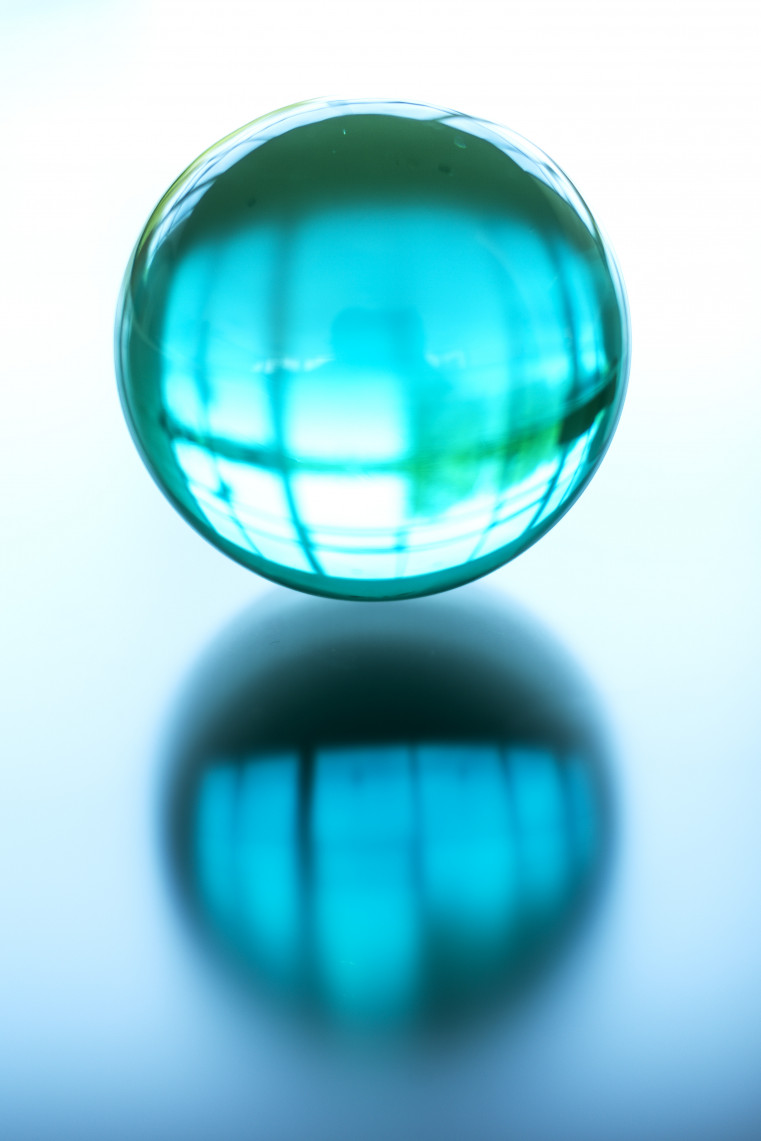
Dipl.-Ing. Friedbert Scharfe, Prof. Dr.-Ing. Thorsten Gerdes and Dr. rer. nat. Klaus Hintzer have invented a novel insulation concept based on hollow spheres of glass. The system based on this concept provides excellent thermal insulation, can be manufactured using existing process technology and is easy to manufacture. It is durable, has countless uses and can be recycled at the end of its useful life.
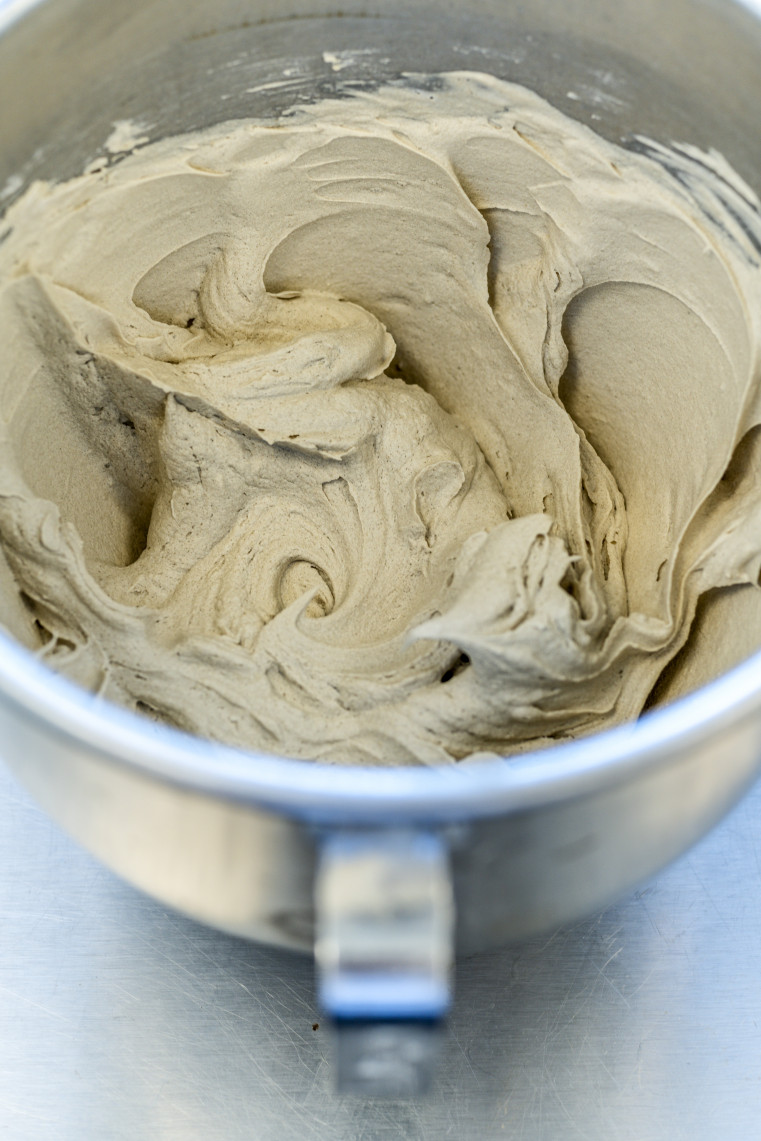
Friedbert Scharfe and Thorsten Gerdes cooperated with partners to develop the system, gradually optimized it and have created a processing method suitable for use in construction. With the hollow glass sphere concept, Klaus Hintzer has laid the foundation for the industrial production of the novel high-quality insulation.
More Details
Resume
Dipl.-Ing. Friedbert Scharfe
- 20.01.1953
- Born Großbodungen
- 1959-1969
- Polytechnic High School, Großbodungen
- 1969 – 1971
- Cement Plant Deuna, Professional Training as a Mechanic
- 1971-1974
- School of Engineering for Building Materials Technology Apolda;
Master Degree (Dipl.-Ing., UAS) in Building Materials Technology - 1975-1977
- School of Engineering Nordhausen; graduation as Special Engineer for Control Systems Engineering
- 1977-1980
- Production Engineer, Deuna Cement Plant
- 1980-1990
- Team Leader Quality Assurance, Deuna Cement Plant
- Since 1990
- Director Research and Development, Franken Maxit GmbH & Co., Board Member
Publications and Patents
- Author/co-author of more than 11 patent applications
Author/co-author of more than 12 scientific publications in journals
Key Research Areas
- Development of low-energy GPZ-based bonding agents as substitutes for cement in collaboration with Weimar University
Development of mortar pads (“Mörtelpads”) in collaboration with RWTH Aachen University
Development of a winter mortar for use at up to -8° C in collaboration with the Materials Testing Institute of Stuttgart University
Development of straw-based insulation boards in collaboration with Hof University of Applied Sciences
Development of ecosphere insulation in collaboration with Bayreuth University and Weimar University
Honors and Awards
- 2008
- Innovation Award of the district of Kulmbach (maxit solar paints and renders/plasters)
- 2014
- Winner of the 2014 Bavaria’s Best 50 Award
- 2019
- Winner of the Callwey Publishers Best Product Award (maxit ecosphere)
Prof. Dr.-Ing. Thorsten Gerdes
- 25.09.1964
- Born Bremervörde
- 1984
- General qualification for university entrance, Tetjus-Tuegel-Gymnasium Bremervoerde
- 1991
- Master degree (Dipl.-Ing.) in Chemical Engineering, University Dortmund
- 1995
- Doctoral degree Dr.-Ing. awarded (“magna cum laude”) by the Faculty of Chemical Engineering, University Dortmund
- 1991 –1995
- Teaching and research fellow at the Chair of Material Science, University Dortmund
- 1993 – 1995
- Teaching Fellow at the University of Applied Science, Iserlohn, Faculty of Physics
- 1995 –1998
- Post-doctorate, senior engineer at the Chair of Material Science, University Dortmund
- 2001- 2017
- Senior researcher and lecturer at the Chair of Materials Processing, University Bayreuth (Akademischer Direktor)
- 12/2016- 3/2018
- (Acting) head of the department of Materials Processing, University Bayreuth
- Since 2017
- Professor of Deggendorf Institute of Technology DIT and Scientific head of the department Glass
Technology at TAZ-Spiegelau, Technology & Application Centre - Since 2017
- Head of the Keylab Glass Technology, University Bayreuth
Other Activities
- since 1997
- Co-Founder and CEO of InVerTec eV., research institute in the field of combined electrothermal treatment and process intensification
- 2009 – 2012
- Managing Director of the Bavarian research association FORGLAS "Multifunctional glass materials for energy-efficient building technologies
- 2011 – 2015
- Scientific & Technology Manager of the FP7 network HARWIN- Harvesting solar energy with multifunctional glass-polymer windows
- 03/16-01/17
- Managing Director of the Glass-Technology-Alliance Oberfranken-Ostbayern, Glass-TAOO (EFFE technology transfer university-SME)
- since 01/2017
- Spokesman of the Glass TAOO
Publications and Patents
- > 40 scientific publications, over 35 patents
Dr. rer. nat. Klaus Hintzer
- 01.09.1954
- Born Stuttgart
- 1964 – 1972
- Mörike Gymnasium of Ludwigsburg, Abitur
- 1973 – 1978
- Study of Chemistry, Eberhard Karls-University of Tuebingen
- 1979
- Diploma in Chemistry, University of Tuebingen
- 1979 – 1983v
- Thesis in Organic Chemistry, University of Tuebingen/Université Paris-Sud
- 1984 – 1988
- Research specialist Corporate Research Hoechst AG, Frankfurt/Gendorf
- 1989 – 1997
- Quality manager and head of test labs for Fluoropolymers
- 1996
- Foundation member of the Fluoropolymer Joint Ventures (JV) Dyenon (Hoechst/3M)
- 1997 – 2001
- US-Research manager and global Quality manager of Dyneon JV, St. Paul/Minnesota
- 2001 – 2011
- Lab manager (Research, Development, Quality) for Fluoropolymers Gendorf, 3M/Dyneon
- 2011 – 2020
- 3M Corporate Scientist; Activities: Fluoromaterials, Glass bubbles, Glass/Ceramic materials, Technology scouting, University contacts
Other Activites
- 2001 – 2020
- Initiator/Participant of more than 12 governmental sponsored projects with universities and industry; Scope: recycling of fluorinated materials, energy savings, circular economy, energy storage/conversion, new fluorinated materials
- 2012 – 2018
- Board member 3M/Germany
- 2016
- Advisory board „Glas-Technologie-Allianz Oberfranken-Ostbayern, University of Bayreuth
- 2017
- Advisory board “Institut für Engergie- und Umwelttechnik (IUTA), Duisburg
- 2019
- Advisory board „Bayerisches Zentrum für Batterieforschung“ University of Bayreuth
Publications and Patents
- Author/Coauthor of more than 230 patent applications
Author/Coauthor of more than 35 scientific publications in journals/books
Honors and Awards
- 1980
- Carl Duisburg grant for staying at University of Paris-Sud
- 1993
- Bavarian Quality award
- 2011
- Carlton Society award 3M
- 2017
- Bavarian/German VCI-award for Up-cycling of Fluoropolymers
Contact
Press
Reinhard Tyrok
Leiter Marketing
maxit Gruppe |
Franken Maxit Mauermörtel GmbH & Co.
Azendorf 63
95359 Kasendorf
Phone: + 49 (0) 9220 / 18 185
Mobile: + 49 (0) 173 / 57 60 325
E-Mail: reinhard.tyrok@maxit.de
Web: www.maxit.de
Web: www.maxit-ecosphere.de
Spokesperson
Dipl.-Ing. Friedbert Scharfe
Leiter F & E
maxit Gruppe |
Franken Maxit Mauermörtel GmbH & Co.
Azendorf 63
95359 Kasendorf
Phone: +49 (0) 9220 / 18 135
Mobile: +49 (0) 173 / 57 60 207
E-Mail: friedbert.scharfe@maxit.de
Web: www.maxit.de
Web: www.maxit-ecosphere.de
A description provided by the institutes and companies regarding their nominated projects
Sprayable facade insulation with glass bubbles
- sustainable and energy-efficient
A medium-sized company, a global player, and a young university have together developed an innovative answer to one of the challenges of our time. The sprayable facade insulation with glass bubbles ‘ecosphere’ - a joint effort of the companies maxit and Dyneon (3M) and the University of Bayreuth - tackles energy saving targets and CO2 reduction, sustainability and the circular economy, skilled worker development, and automation in the construction industry in one fell swoop. Indeed, it is a shining example of science and business joining forces to build a better future together.
Buildings still account for around 35 percent of Germany's final energy consumption, and the potential for savings that has not yet been exploited is commensurately huge. With well-insulated external walls, heating energy requirements and the associated CO2 emissions can be permanently reduced, meaning the transformation of the building envelope is crucial to achieving the climate protection targets we have set ourselves. At around 20 percent, the share of direct and indirect greenhouse gas emissions from private households clearly exceeds the contribution of the transport sector (approx. 18 percent) and that of agriculture (approx. 8 percent).
In social terms, this has made consumers more aware of the issue of insulation. Although there is already a wide range of insulation systems available, the characteristics of the materials used, leaving aside their insulation properties, often leave much to be desired. Their manufacturing usually prohibits recycling, fire protection, aesthetics, flexibility, and energy input all from being perfectly reconcilable in one product. Raw material resources, on the basis of which these products are manufactured, are also increasingly coming into focus, as is the question of subsequent recycling of the insulation system. Consequently, anyone wishing to provide their house - whether an existing building or a new construction - with modern facade insulation is confronted with a complicated decision.
Research for progress
With the ecosphere system, the team created a completely new solution for insulating facades. It is the result of manIn social terms, this has made consumers more aware of the issue of insulation. Although there is already a wide range of insulation systems available, the characteristics of the materials used, leaving aside their insulation properties, often leave much to be desired. Their manufacturing usually prohibits recycling, fire protection, aesthetics, flexibility, and energy input all from being perfectly reconcilable in one product. Raw material resources, on the basis of which these products are manufactured, are also increasingly coming into focus, as is the question of subsequent recycling of the insulation system. Consequently, anyone wishing to provide their house - whether an existing building or a new construction - with modern facade insulation is confronted with a complicated decision.y years of research cooperation between the project partners involved. With funding from the Federal Ministry of Education and Research (BMBF), a building material technology was developed under the leadership of maxit, in close cooperation with the University of Bayreuth and Dyneon, a company of the 3M group. The resulting system not only boasts excellent insulation properties, it has its eyes, above all, on the prize of resource conservation. This applies both to the raw materials used and to the labour force.
The result of the research work is a dry mortar containing a lightweight aggregate, which manages the tightrope act of balancing maximal ease of application on the construction site with optimal insulation performance on the facade. What is new about the insulation system is its material composition, which comes to the fore in the "wedding" of glass and plaster.
In particular, the secret of ecosphere is its Glass Bubbles, small and water-insoluble, hollow glass spheres that act as lightweight aggregates. The hollow and thin-walled glass particles have a diameter of only 10-200 micrometres. Due to the unique combination of their spherical shape, pre-defined size, low density, high strength, and good thermal insulation, they are ideally suited for insulation - so good, in fact, that they are already in use.
What is new about ecosphere is the small size and high stability of the glass bubbles. Through their innovative combination with the latest plaster technology and the development of existing spray technologies for plasters, it has been possible to apply the new material to walls in layers up to 15 cm thick without breaking the filigree glass bubbles. Installation errors, which can occur with conventional panel systems, are virtually impossible thanks to the spraying process.
The path to mass production
The research team was able to overcome several challenges on their way to creating a mass product::
1. Suitable hydraulic binder with low CO2 footprint
In order to optimize the ecological balance sheet of the insulation, a binder formulation was developed characterized by a low CO2 footprint, but at the same time meeting the demands of insulation efficiency, good mechanical properties, and long-term stability.
2. Optimization of the glass bubbles
Thanks to the manufacturing process, the internal pressure in the glass bubbles is very low. This not only improves the insulating effect, but also increases their compressive strength. Larger bubbles with very thin walls have particularly good insulating properties. However, during the spraying process they are exposed to strong mechanical stress, so that bubble breakage can occur. As a result, the insulating effect could deteriorate. During the development process, glass bubbles with an optimal set of characteristics were found, providing excellent insulation, surviving the processing process virtually undamaged, and, in addition, not corroding in the strongly alkaline environment of the binder matrix.
3. Optimization of the building material composition
The higher the proportion of glass bubbles, the better the insulation performance, yet from a certain percentage volume upward, mechanical properties deteriorate. In order to still achieve the desired thermal conductivity of 40 mW/m.K, additional porosity was provided by developing the compressed air-assisted spraying process. To prevent this, in turn, from reducing the mechanical load capacity of the insulation too much, the system was modified to allow the crystals formed during the binder hardening phase to bond more tightly to the glass bubbles.
4. Optimization of the processing properties
The goal of the development work was an insulation which can be delivered to the construction site either as bagged goods or in a silo, to be processed on site. For processing in plastering machines, the dry mixture of binder, glass bubbles, and aggregates is mixed with water. The mixing screw must homogenize the building material in a short time without subjecting the hollow glass bubbles to excessive mechanical stress. The material is then sprayed on with compressed air. The use of suitable additives ensures that the foamed mass has good flow properties and yet remains stable. Trials with spraying robots are already underway, which are set to be deployed on construction sites in the medium term.
Inventions lead to innovation
Ecosphere was developed as part of the BMBF initiative "High-Tech Materials in Construction". The driving force were the aforementioned shortcomings of existing insulation systems, and the practical goal of creating a high-performance alternative in this area. Through continuous optimization, the research team progressed ever closer to their envisaged project goals. In addition to its very good insulation properties, the ecosphere system combines previously incompatible material characteristics, such as
Recyclability: The mineral insulation material can be easily removed and after grinding, can be completely reused in the cycle.
Fire protection class A1: Not containing organic additives, and thanks to good insulation properties, ecosphere fully meets the requirements for the highest fire protection class according to DIN 4102 and EN 13501-1.
Aesthetics & flexibility: The insulation material can be applied flexibly in a thickness of up to 15 centimetres to exterior and interior walls by means of a spraying process, regardless of the composition of the underlying surface. This even makes ecosphere suitable for the renovation of buildings with heritage-listed facades.
Low material intensity: A dry bulk density of only 125 kg/m3, means a mineral building material of low material intensity, involving a commensurate conservation of resources, is now available. It completely foregoes the use of the scarce resource "construction sand" - as found in conventional plasters
The combination of these properties has the potential to significantly improve the acceptance of energy-efficient building refurbishment. In this way, ecosphere can make a significant contribution to achieving the German government's energy saving targets. And one other aspect gives the innovation real future potential. Because the insulation can be sprayed on by machine, there is nothing to prevent the use of robots, which is still the exception in the construction sector. This means that skilled positions, which are becoming increasingly difficult to fill, can be made significantly more attractive. The work of the plasterer will be noticeably easier, and in fact, the trade will change completely.
Success has not been long in coming: ecosphere was already presented at the BAU trade fair - the world's leading trade fair for architecture, materials, and systems - in January 2019, and has since been available commercially and on an industrial scale for new and existing buildings.
Maxit is renowned for innovative products and services for the construction industry and building trades. In over four decades, a group of companies with the character of an SME has developed into a business of over 800 employees at nine locations in Bavaria, Saxony, Thuringia, and the Czech Republic. Using state-of-the-art equipment, maxit produces dry mortar and mixtures of binders, aggregates, and additives, bagged and in silos, and offers a comprehensive range of products for the areas of shell construction, finishings, and facades.
Dyneon is a company of the 3M group. The multi-technology group 3M was founded in 1902 in Minnesota, USA, and today is one of the most innovative companies worldwide. 3M is represented in over 190 countries by 96,000 employees, and achieved sales of 32 billion US dollars in 2019. The basis for its innovative strength is the diverse use of 51 proprietary technology platforms. Today, its portfolio includes more than 55,000 different products used in almost every area of life. 3M holds more than 25,000 patents and generates about one third of its sales with products that have been on the market for less than five years.
The University of Bayreuth is one of the most successful young universities in Germany. Interdisciplinary research and teaching characterize its 160 courses of study at seven faculties. Keylab Glass Technology is part of the Ceramic Materials research group at the University of Bayreuth, and combines fundamental research with application-oriented development. It brings together expertise in physics, chemistry, materials science, and engineering. One focus is on the production and processing of glass-based products for the building sector.
Dipl.-Ing. (FH) Friedbert Scharfe is an authorised signatory and head of the Research & Development department at Franken Maxit Mauermörtel GmbH & Co. in Azendorf.
Prof. Dr.-Ing. Thorsten Gerdes heads Keylab Glass Technology in the Ceramic Materials research group at the University of Bayreuth.
Dr. rer. nat. Klaus Hintzer is a corporate scientist at Dyneon in Burgkirchen, a company of the 3M group.
The right to nominate outstanding achievements for the Deutscher Zukunftspreis is incumbent on leading German institutions in science and industry as well as foundations.
The project "Sprayable façade insulation with glass bubbles – An energy-efficient and sustainable innovation for building insulation“ was submitted by Bundesministerium für Bildung und Forschung.
Federal President Frank Walter Steinmeier will present the 24th German Future Prize to one of the three nominated teams on November 25, 2020.
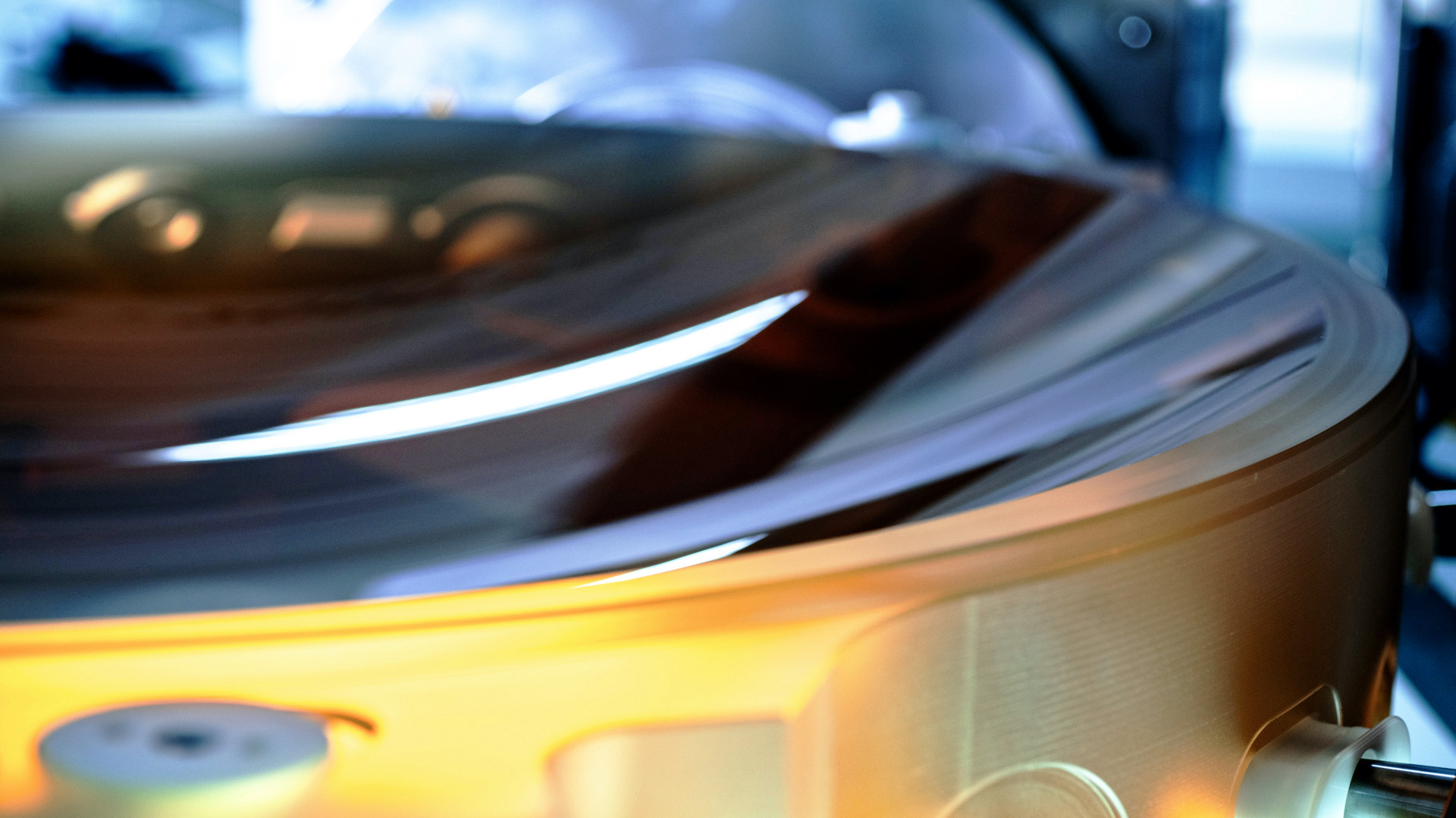