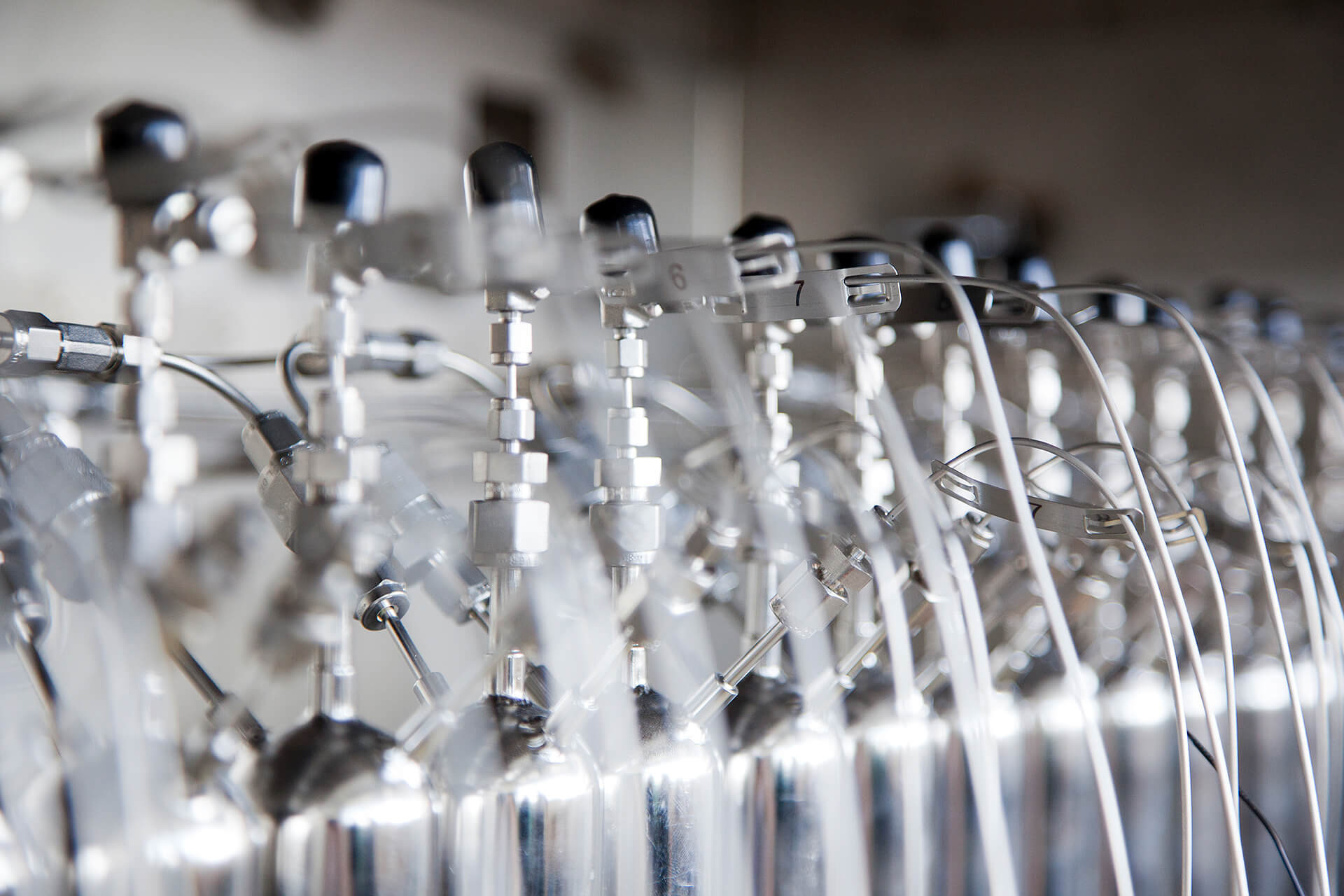
Nominee 2010
Chemische Beschleuniger

Prof. Dr. Ferdi Schüth, Dr. Dirk Demuth and Dr. Wolfram Stichert show how to test a variety of different materials simultaneously for their suitability as catalysts – and to identify the most effective reaction accelerator reliably. Ferdi Schüth is a scientific member and Director of the Max Planck Institute for Coal Research. He is also one of the founders of the company hte AG in Heidelberg where he also serves on the Supervisory Board. Dirk Demuth is a co-founder of the company and is CEO/COO and chairman of the Board of Directors. Wolfram Stichert is a co-founder of hte AG and has served as CFO since 2003.

At the heart of the system developed by the three nominees is the parallel reactor technology. It combines several dozen individual tubes in which the reaction medium flows over different potential catalysts simultaneously. In this way, numerous experiments can be run at the same time which in the past had to be carried out as time-consuming single experiments. New catalysts, for example for cleaner combustion processes, can be found up to 100 times faster using this process.
more details
Resumes
Prof. Dr. rer. nat. Ferdi Schüth
- 08.07.1960
- geboren in Allagen (heute Warstein)
- 1978
- Abitur
- 1978 – 1984
- Studium der Chemie, Westfälische Wilhelms Universität, Münster
- 1984
- Diplomarbeit „Reduktion von NO mit CO in Gegenwart von Sauerstoff an Palladium-haltigen Katalysatoren“, Westfälische Wilhelms Universität, Münster
- 1983 – 1988
- Studium der Rechtswissenschaften, Westfälische Wilhelms Universität, Münster
- 1984 – 1988
- Dissertation „Oszillationen der katalytischen Oxidation von CO mit NO und mit O2 – IR-spektroskopische Untersuchungen zum Mechanismus“, Westfälische Wilhelms Universität, Münster
- 1988 – 1989
- Postdoktorand an der University of Minnesota, Minneapolis, USA
- 1989
- Erstes Staatsexamen der Rechtswissenschaften, Westfälische Wilhelms Universität, Münster
- 1989 – 1994
- Wissenschaftlicher Assistent an der Johannes-Gutenberg-Universität, Mainz
- 1992 – 1994
- Habilitationsstipendium der Deutschen Forschungsgemeinschaft (DFG)
- 1993
- Visiting Assistant Professor, University of California, Santa Barbara, USA
- 1995
- Habilitation an der Johannes-Gutenberg-Universität, Mainz
- 1995 – 1998
- Professor am Lehrstuhl für Anorganische Chemie, Johann Wolfgang Goethe-Universität, Frankfurt
- Seit 1998
- Wissenschaftliches Mitglied der Max-Planck-Gesellschaft und Direktor am Max-Planck-Institut für Kohlenforschung, Mülheim an der Ruhr
- Seit 2000
- Honorarprofessor an der Ruhr-Universität Bochum
- 2007
- Honorarprofessor an der Dalian University of Technology, Dalian, China
- 2008
- Gastprofessor an der Beijing University, Beijing, China
Ehrungen:
- 1989
- Promotionspreis der Westfälischen Wilhelms Universität, Münster
- 1991
- Boehringer-Ingelheim Preis
- 2001
- Wissenschaftspreis des Stifterverbandes für die Deutsche Wissenschaft
- 2002
- Gewähltes Mitglied der acatech - Deutsche Akademie der Technikwissenschaften
- 2003
- Gottfried Wilhelm Leibniz-Preis der Deutschen Forschungsgemeinschaft (DFG)
- 2008
- Gewähltes Mitglied der Nationalen Akademie der Wissenschaften Leopoldina
- 2009
- ERC Advanced Grant
- 2010
- Heisenberg-Medaille der Alexander-von-Humboldt-Stiftung
- 2010
- Gewähltes Mitglied der Nordrhein-Westfälischen Akademie der Wissenschaften und der Künste
Weitere Tätigkeiten:
- Seit 1999
- Mitbegründer und Aufsichtsratsmitglied der hte Aktiengesellschaft
- Seit 1994
- Mitglied verschiedener Dechema-Arbeitsausschüsse
- 2004 – 2009
- Mitglied des wissenschaftlichen Ausschusses des Landes Niedersachsen
- Seit 2004
- Mitglied des Präsidiums der Gesellschaft Deutscher Chemiker (GDCh)
- Seit 2007
- Vizepräsident der Deutschen Forschungsgemeinschaft (DFG)
- Seit 2009
- Stellvertretender Vorsitzender des wissenschaftlichen Ausschusses der Max-Planck-Gesellschaft
- Seit 2009
- Stellvertretender Vorsitzender der Dechema
- Seit 2009
- Aufsichtsratsmitglied des Karlsruhe Institute of Technology (KIT)
Dr. rer. nat. Dirk Demuth
- 25.05.1966
- geboren in Trier
- 1985
- Abitur
- 1985 – 1992
- Studium der Chemie an der Johannes-Gutenberg-Universität, Mainz
- 1988 – 1989
- Stipendium des Deutscher Akademischer Austauschdiensts (DAAD),
/Auslandsstudium an der University of California, Irvine, USA - 1991 – 1992
- Diplomarbeit „Präparation und Charakterisierung von modifizierten Alumophosphaten für optische Anwendungen“ an der Johannes-Gutenberg-Universität, Mainz
- 1992 – 1994
- Dissertation „Synthese und Charakterisierung von modifizierten Alumophosphaten für optische Anwendungen“ an der Johannes-Gutenberg-Universität, Mainz
- 1993 – 1994
- Forschungsaufenthalt, University of California, Santa Barbara, USA
- 1995
- Forschungsaufenthalt, Fritz-Haber-Institut der Max-Planck-Gesellschaft, Berlin
- 1995 – 1999
- Projektleiter Katalysatorforschung, BASF Aktiengesellschaft, Ludwigshafen
- 1999 – 2000
- Mitbegründer und Geschäftsführer hte GmbH, Heidelberg
- Seit 2000
- Vorstandsvorsitzender der hte Aktiengesellschaft, Heidelberg
Ehrungen:
- 1995
- Promotionspreis der Johannes-Gutenberg-Universität, Mainz
- 2002
- Wissenschaftspreis des Stifterverbandes für die Deutsche Wissenschaft
Weitere Tätigkeiten:
- Seit 2000
- Mitglied in unterschiedlichen Gremien der Dechema, VCI und BDI zu Katalyse, High Throughput Experimentation und Chemie Start-ups
- 2000 – 2005
- Aufsichtsratsmitglied von hte North America Inc., später Fqubed Inc., Princeton, NJ bzw. San Diego, USA
- 2004 – 2008
- Vorstandsmitglied von ConNeCat (Kompetenznetzwerk Katalyse)
- Seit 2009
- Mitglied der beratenden Kommission der Deutschen Gesellschaft für Katalyse
- Seit 2010
- Kuratoriumsmitglied der Zeitschrift Chemie Ingenieur Technik
Dr. rer. nat. Wolfram Stichert
- 15.04.1970
- geboren in Frankfurt am Main
- 1989
- Abitur
- 1990 – 1996
- Studium der Chemie, Johannes-Gutenberg-Universität, Mainz und Johann Wolfgang Goethe-Universität, Frankfurt
- 1996
- Diplomarbeit „Zur Herstellung von Zirconiumoxid“ an der Johann Wolfgang Goethe-Universität, Frankfurt
- 1996 – 1998
- Wissenschaftlicher Mitarbeiter am Institut für anorganische und analytische Chemie der Johann Wolfgang Goethe-Universität, Frankfurt
- 1998 – 1999
- Wissenschaftlicher Mitarbeiter, Max-Planck-Institut für Kohlenforschung, Mülheim
- 1999
- Dissertation „Steuerung der Eigenschaften von Zirconiumoxid durch Kontrolle der Herstellungsparameter“ an der Johann Wolfgang Goethe-Universität, Frankfurt
- 1999
- Postdoktorand, Industrielle Katalyse, BASF Aktiengesellschaft, Ludwigshafen
- 1999
- Mitbegründer und Forschungschemiker bei der hte GmbH, Heidelberg
- Seit 2000
- Mitglied des Vorstandes bei der hte Aktiengesellschaft, Heidelberg
- 2001 – 2005
- Berufsbegleitendes Studium der Betriebswirtschaftslehre an der Fernuniversität Hagen
- 2005
- Diplomarbeit „Unternehmensbewertung in dominierten Konfliktsituationen“ an der Fernuniversität Hagen
Weitere Tätigkeiten:
- 2000 – 2005
- Aufsichtsratsmitglied von hte North America Inc., später Fqubed Inc., Princeton, NJ bzw. San Diego, USA
Contact
Spokesperson
Prof. Dr. rer. nat. Ferdi Schüth
Direktor
Max-Planck-Institut für Kohlenforschung
Kaiser-Wilhelm-Platz 1
45470 Mülheim
Tel.: +49 (0) 208 / 30 62 373
Fax: +49 (0) 208 / 30 62 995
E-Mail: schueth@mpi-muelheim.mpg.de
Web: www.mpi-muelheim.mpg.de
Press
Dr. Michael Paul
Business Development Manager & Head of Marketing
hte Aktiengesellschaft
Kurpfalzring 104
69123 Heidelberg
Tel.: +49 (0) 6221 / 74 97 282
Fax: +49 (0) 6221 / 74 97 134
Mobil: +49 (0) 160 / 36 36 456
E-Mail: Michael.Paul@hte-company.de
Web: www.hte-company.de
A description provided by the institutes and companies regarding their nominated projects
Clever solutions to our energy problems often stem from a source that is rarely acknowledged by the general public– from research on catalysts. Catalysts help save energy and tap new energy sources. They accelerate chemical reactions by reducing the energy required to trigger almost every chemical transformation. Some chemical transformations would even be impossible without catalysts or would above all deliver a product that the chemist was not targeting.
New, more efficient catalysts can be identified up to 10 to 100 times faster and also much more reasonably with the innovation developed by Ferdi Schüth and the scientists at hte AG headed by Dirk Demuth and Wolfram Stichert. Their technology platform supports testing using a high throughput experimentation process so that even a small team can analyze thousands of these reaction accelerators every year. Without the platform, even a large-scale lab would only be able to conduct several hundred tests – if all goes well. This method is now used by almost all petrochemical companies to customize catalysts to extract more fuel from a barrel of petroleum and to obtain the starting materials for pharmaceuticals, dyes or plastics. Or, to be able to utilize lower quality petroleum as found in oil sands, for example. Industry also hopes to use this method to find catalysts for converting natural gas into liquid fuels or to produce fuels and valuable basic chemicals from biomass, possibly even from wood scraps or straw. Innovative techniques have already helped lower the amount of platinum, an expensive precious metal in catalytic converters for automobiles and to desulfurize fuels more effectively.
They thought it couldn’t be done
Ferdi Schüth and his colleagues at hte AG have dramatically cut the amount of time needed to search for catalysts with their development of an automatic and parallel testing process in the late 1990’s. Several academic institutions as well as an American company were working on the same idea at the time, but their technologies were further away from becoming an industrial reality and consequently not as successful in the end. The pharmaceuticals industry was already successfully using the high throughput experimentation process to synthesize active ingredients. Most experts doubted, however, that this principle could be applied to catalyst research. This was because pharmaceutical ingredients are almost always manufactured at temperatures of below 100 degrees centigrade and at low pressures. Moreover, syntheses always takes place in closed vessels in which conditions are easily controlled, particularly since the reactions in this case only take a few hours.
Experiments under harsh conditions
In contrast, scientists usually test their catalyst candidates at pressures that far exceed atmospheric pressure as well as at temperatures of around 500 degrees, sometimes even as high as 1000 degrees centigrade. And, additional heat is also often released during the reaction. Catalysts also usually have to be kept moving. This means the reactants flow constantly through the reaction bed in a liquid or gaseous state – and often for weeks at a time. Under these circumstances, most experts agreed it was impossible to guarantee uniform conditions in all reactors of a parallel system. And then there is the problem of chemical analysis. Pharmaceutical engineers can simply take a sample after synthesis and analyze the products. Catalyst researchers usually only obtain results relevant for industry if they observe live processes in the reactor and reliably analyze even complex reaction mixtures in a very short period of time.
Moreover, industry in principle also doubted that their parallel reactor tests could help in the search for catalysts. This was because until recently parallel testing also always went hand-in-hand with miniaturization – a welcome effect in the pharmaceuticals industry in which minute amounts of substances provide explicit results, not least of all because the industry also works on the scale of kilograms in production and thus can save on chemicals.
In catalyst research, it is essential to duplicate the conditions of industrial processes as closely as possible from the very beginning. This primarily means that the amounts of test specimens may not be too small: the starting materials simply flow differently through a pinch of catalyst material than they would through a pile weighing tons.
Close to the industrial process from the outset
Ferdi Schüth and his colleagues at hte AG did not allow themselves to be put off by the initial skepticism and also convinced BASF AG of the viability of their concept in 1999. BASF gave the start-up originally founded as a German limited liability company (GmbH) a development contract and made € 16m available for five years. Shortly thereafter an agreement was reached with the Chevron oil company which provided an additional € 4.4m.
The researchers used the start-up capital to develop the reactor system which is similar in function to a pharmaceutical high throughput experimentation process, but is completely different in design in every technical detail. Schüth and researchers at hte AG used several grams of substance for certain tests and designed the tests in such a way that their results could also be applied to industrial processes. For example, they selected base materials important to industry and considered whether the catalyst would ultimately be used in powder or pellet form. They also ensured that the starting materials in all reactors were in contact with the catalysts for exactly the same amount of time and approximately as long as they would in the industrial process. The materials for the reactor tubes were adapted specifically to the respective reaction to ensure that they would withstand the aggressive conditions and chemicals.
Automatic analysis of the products
Typically up to 48 individual reactors are run simultaneously today, but above to several hundred are possible. To ensure that all reactors reach the same temperature, the researchers heat the tubes in blocks made of an alloy that is extremely thermally conductive, sometimes even enclosing the individual reactors in a heating unit. The gaseous and liquid starting materials pass through a common supply line into the reactors. If necessary, automatic valves are used to control the individual tubes sequentially.
The chemical analysis was especially challenging. It reveals whether a catalyst is active and whether it is actually doing what it’s supposed to. How fast the processes run in the individual reactors ultimately decides how fast the search for effective catalysts runs overall. Thus a system of specially designed valves automatically captures gaseous products from every single reactor while a robotic arm draws off liquid products.
Ultimately, which method the system then uses to analyze the products depends on what the chemists know about the reaction ahead of time. They often already have a good idea what will happen in the reactor. They then use a gas-phase chromatograph calibrated to the expected substances to analyze the products. However, if they expect numerous and possibly unexpected by-products, they will add a mass spectrometer after the gas-phase chromatograph. They are also sometimes able to determine the composition in the product mix using more sophisticated methods which react specifically, for example, to sulfur or nitrogen compounds.
Filter for the high volume of data
For a useful parallel testing, the scientists at hte AG had to develop an automatic process to evaluate the measured data. This can be up to several terabytes in every project. Consequently, 18 software developers at hte AG concentrate on creating programs to filter the information chemists actually need to know from the masses of data collected.
The measuring results from the reactor system are in the meantime just as accurate as data from pilot installations. This is not least of all due to the fact that hte AG adapts the system by adding numerous existing modules and special developments tailored to a customer’s specific requirements. Every industrial process takes place under its own boundary conditions. The more they are factored in, the shorter the development time for a new catalyst. In addition to individually customized reactor systems, hte AG also offers services to search for a catalyst. To this end, they offer the full range of possibilities afforded by their platform in different systems.
160 jobs with potential for growth
Just how well hte AG has done with the concept developed by Ferdi Schüth, Dirk Demuth and Wolfram Stichert is not merely evident in the fact that all competitors soon began taking similar approaches. It is also apparent in the economic figures: the company has created 160 jobs – for scientists, engineers, and highly qualified skilled workers in laboratories, precision mechanics and electronics. Turnover for hte AG which BASF in 2008 acquired a stake in has reached € 100m over the past ten years. A good majority of hte AG sales were realized abroad. Their success thus demonstrates that high-tech innovations from Germany not only strengthen the country as a base of economic activity, but also contributes to the export success of German industry.
In future, the company expects continued healthy growth – both concerning headcount as well as regarding turnover and profit. It is to be expected that fossil energy carriers will become ever scarcer and climate change ever more alarming. The efficient search for catalysts that extract more from fossil raw materials and tap alternative energy carriers will thus be even more important in the years to come. Moreover, scientists hope to apply the high throughput experimentation process to other areas and continue to develop the platform – for instance to search for powerful energy stores. The fact that they may perhaps run into major obstacles and persistent doubt more often will hardly put off the scientists – they have already repeatedly overcome them in the past.
About hte Aktiengesellschaft, Heidelberg
hte Aktiengesellschaft is a leading provider of technology solutions and services for customers in the energy, refinery, chemical and environmental sector. The hte offerings make research and development in the area of heterogeneous catalysis much faster and productive. As a reliable partner for the high throughput experimentation, hte offers extensive expertise supported by complementary products and services: 1) technology solutions – customized, integrated hardware and software systems, turn-key installations for customers; 2) R&D solutions – research programs carried out at the hte facility in Heidelberg. hte provides high-quality services to customers searching for solutions to the global challenges posed by environmental and climate protection as well as energy efficiency and mobility. hte – the high throughput experimentation company.
About the Max Planck Institute for Coal Research, Mülheim an der Ruhr
The almost 100-year-old Max Planck Institute for Coal Research in Mülheim an der Ruhr is one of the oldest institutes of the Max Planck Society. Research at the institute conducted by a staff of more than 300 focuses on chemical reactions that are both energy efficient and conserve resources, wherein catalysis in all of its facets is at the focus of their work. The Max Planck Society conducts top-level research in the area of basic research: Nevertheless important technological stimuli have repeatedly been provided by the MPI for Coal Research, including the Fischer-Tropsch synthesis used to produce fuels from coal, gas or biomass, the ziegler catalysts for producing the most important bulk plastics, decaffeination of coffee, and the recent development of high throughput experimentation methods in catalyst research.
The right to nominate outstanding achievements for the Deutscher Zukunftspreis is incumbent upon leading German institutions in Science and Industry as well as foundations.
The project “Turbo-test for Chemical Accelerators – New Catalysts create Energy Options” was nominated by the Max Planck Society for the Advancement of Science together with the Germany Academy of Science Leopoldina and the Innovation Prize of the state of North Rhine-Westphalia.
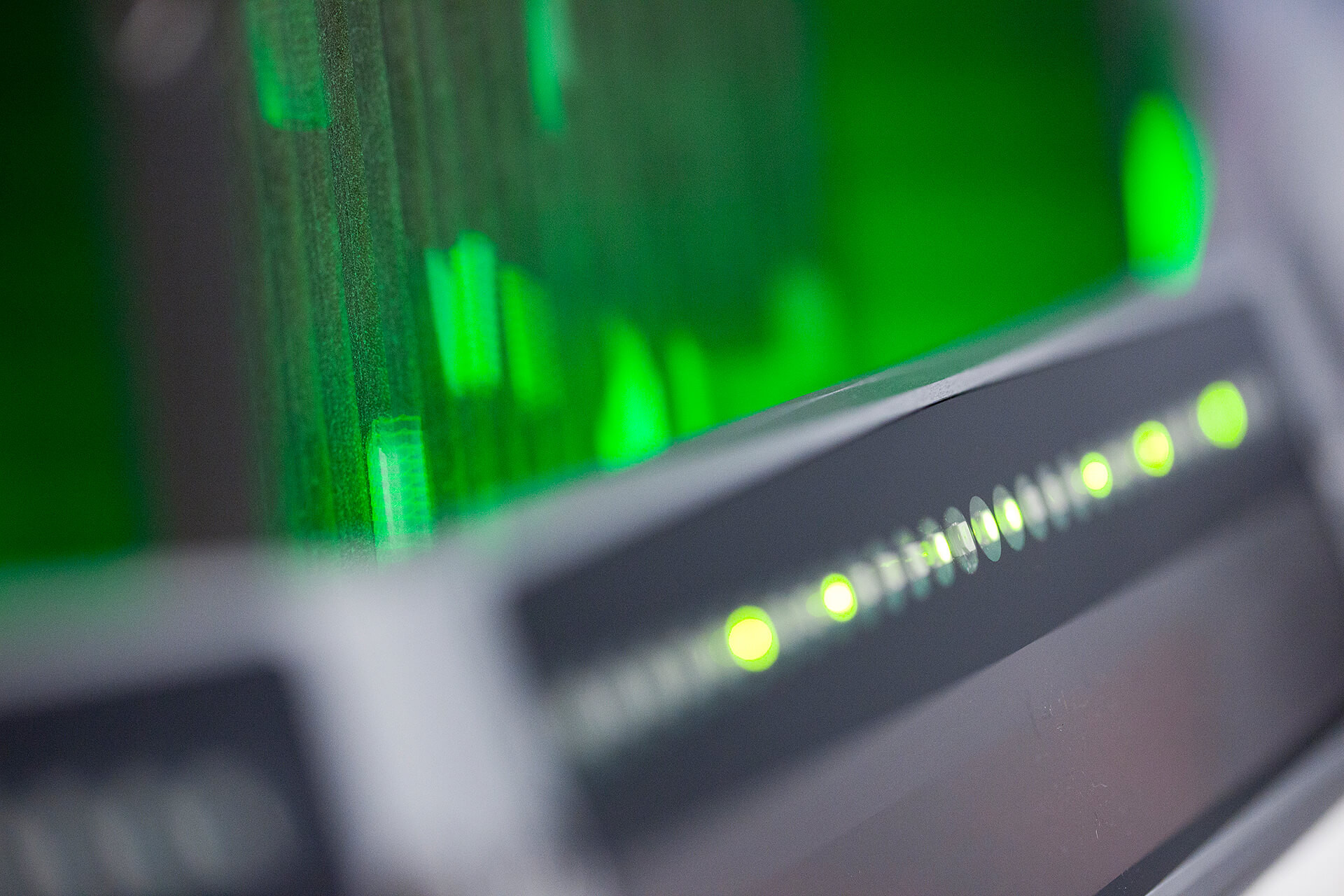