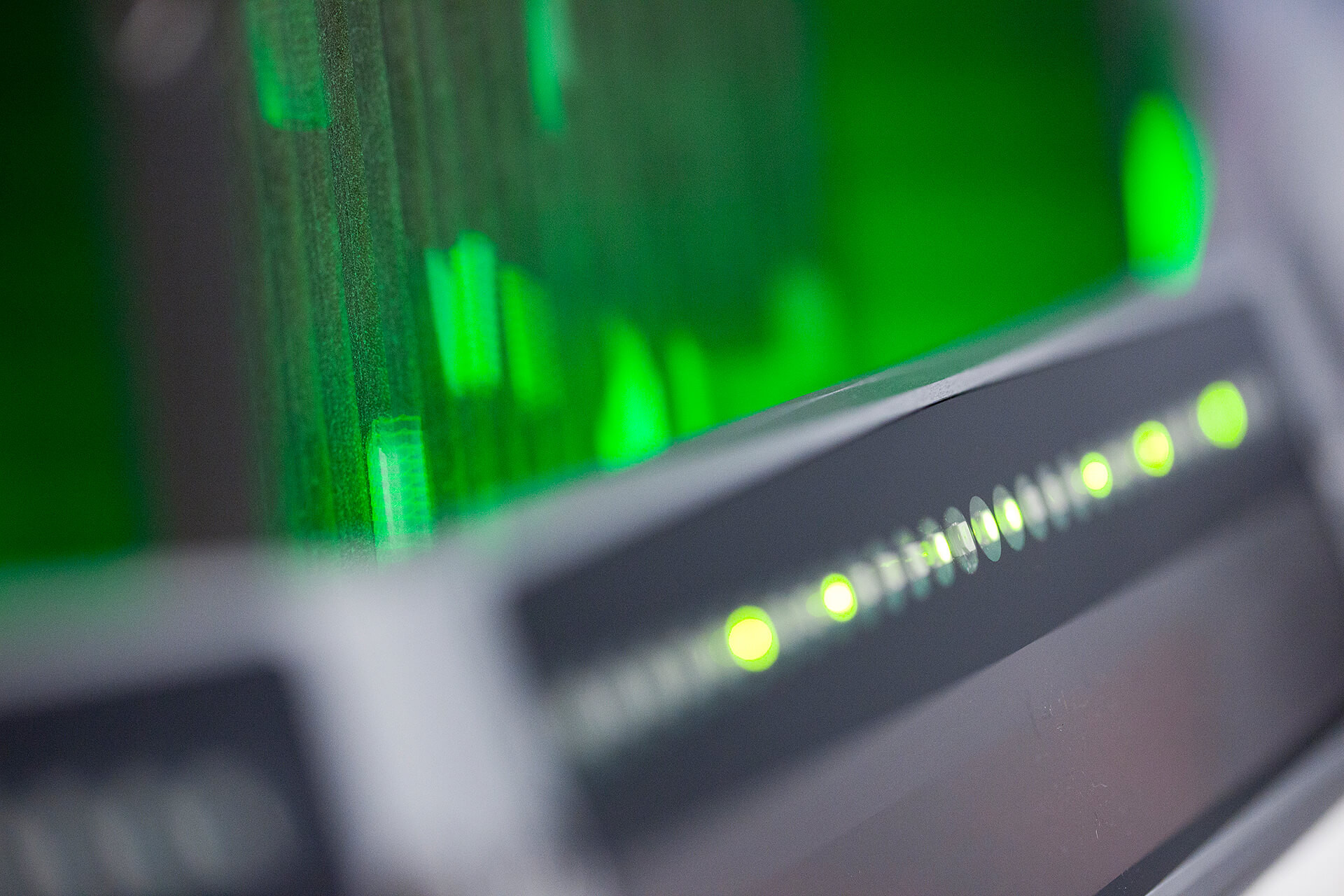
Nominee 2010
Laserlicht findet Wertstoffe
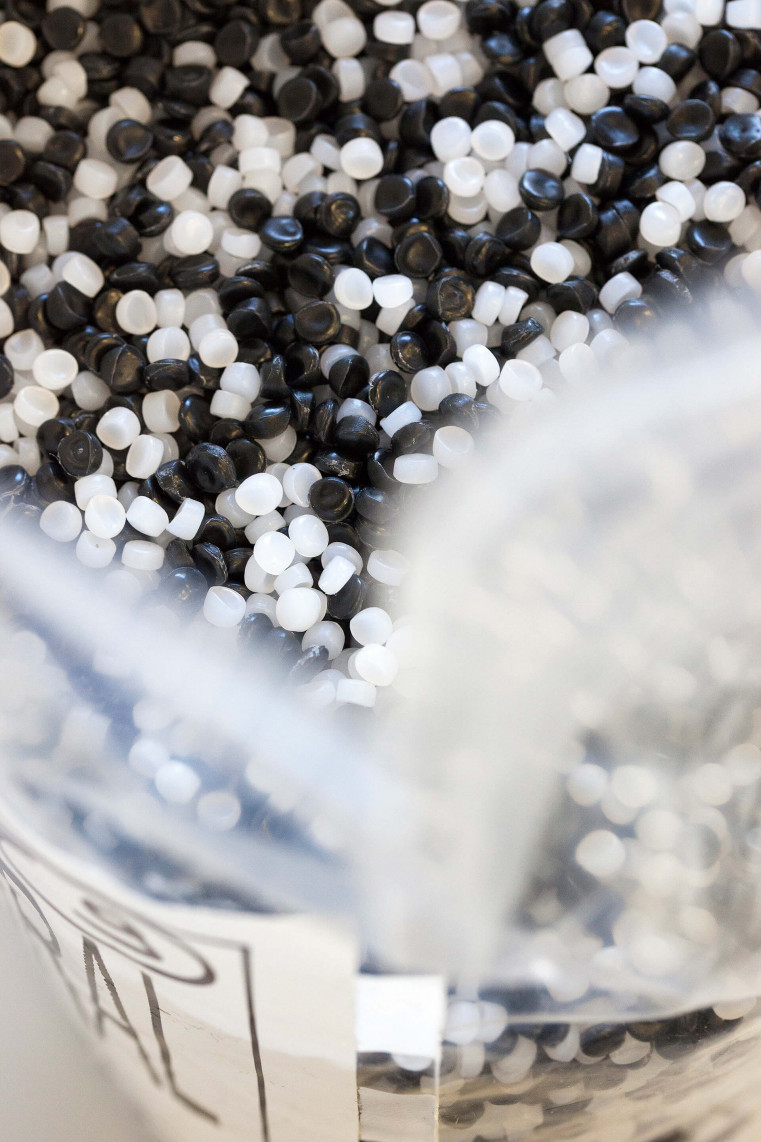
Prof.-Dr. Gunther Krieg, Dipl.-Ing. Dirk Fey and Dipl.-Ing. Jürgen Bohleber have developed a system that separates polyethylene terephthalate (PET) reliably from other materials during recycling so that even minute and virtually undetectable amounts of impurities and contaminants can be sorted out and the recycled plastic used without reservation to produce new bottles in a process that has come to be known as closed-loop or PET bottle-to-bottle recycling. Gunther Krieg heads the Transferzentrum Optoelektronik und Sensorik of the Steinbeis Foundation in Karlsruhe and founded UNISENSOR Sensorsysteme GmbH in 1990. Dirk Fey is chief technical officer at the firm, Jürgen Bohleber is project manager responsible for designing sensor machines for the recycling industry.
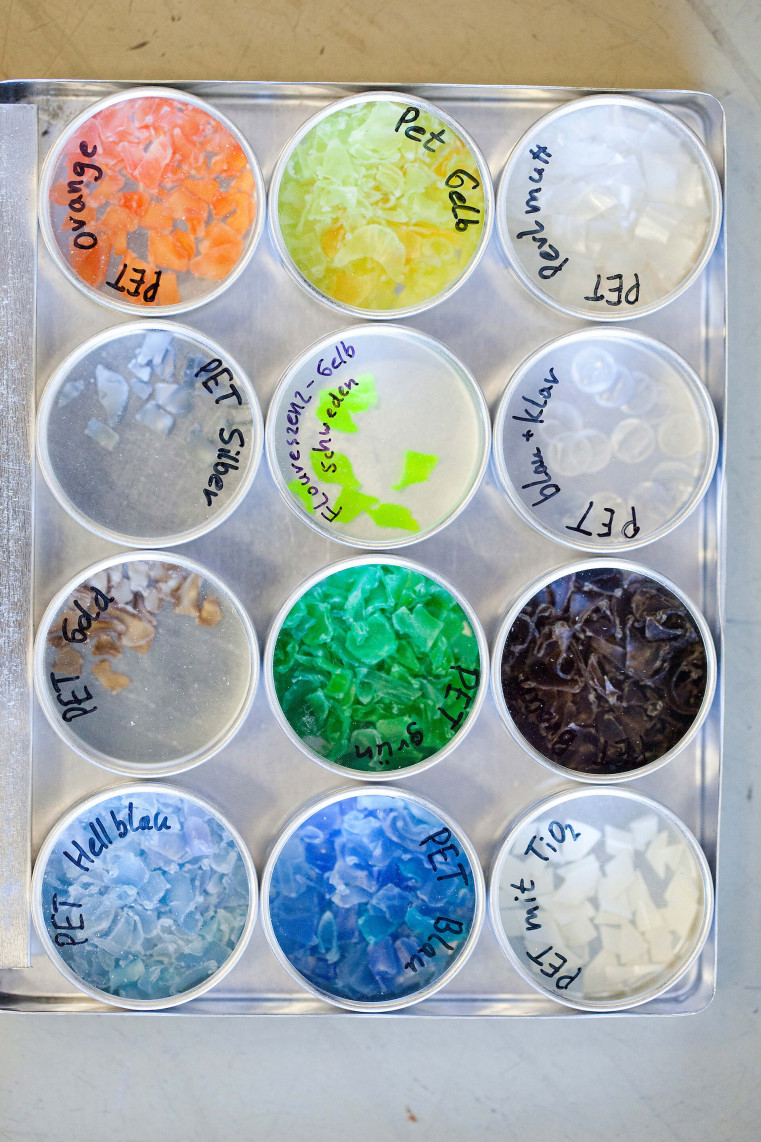
“Powersort 200”, the system they have developed, is based on ultra-high-speed laser spectroscopy. In the process used, powerful lasers expose granulate or plastics crushed into flakes to ultraviolet, visible and infrared light.
more details
Resumes
Prof. Dr.-Ing. Gunther Krieg
- 12.07.1942
- geboren in Tübingen
- 1962
- Abitur
- 1962 – 1965
- Studium der Physik und Mathe matik, Eberhard Karls Universität, Tübingen, Vordiplom in Physik
- 1965 – 1968
- Studium der Physik, Universität Karlsruhe, Karlsruhe
- 1968
- Diplom
- 1968 – 1970
- Wissenschaftlicher Assistent, Institut für Kernverfahrenstechnik der Universität Karlsruhe und des Forschungszentrums Karlsruhe (heute KIT - Karlsruhe Institute of Technology), Karlsruhe
- 1970
- Promotion, Universität Karlsruhe, Kralsruhe
- 1970 – 1973
- Wissenschaftlicher Angestellter, Institut für Kernverfahrenstechnik / Institut für Mikrostrukturtechnik der Universität Karlsruhe und des Forschungszentrums Karlsruhe (heute KIT)
- 1973 – 1980
- Wissenschaftlicher Mitarbeiter am Institut für Kernverfahrenstechnik / Institut für Mikrostrukturtechnik der Universität und des Forschungszentrums Karlsruhe(heute KIT)
- 1978
- Gruppenleiter am Institut für Kernverfahrenstechnik / Institut für Mikrostrukturtechnik der Universität und des Forschungszentrums Karlsruhe(heute KIT)
- 1980
- Berufung als Professor für den Fachbereich Naturwissenschaften der Hochschule Technik und Wirtschaft, Karlsruhe
Projektbevollmächtigter der Stabstelle für Technologietransfer des Forschungszentrums Karlsruhe(heute KIT) - 1985 – 1995
- Dekan des Fachbereichs Naturwissenschaften der Hochschule für Technik und Wirtschaft Karlsruhe
Gründer des Studiengangs Sensorsystemtechnik (1990) - seit 1985
- Leiter des Transferzentrums Optoelektronik und Sensorik der Steinbeis-Stiftung, Karlsruhe
- 1990
- Gründung der UNISENSOR Sensorsysteme GmbH Karlsruhe als Spin-Off des Forschungszentrums Karlsruhe und der Hochschule für Technik und Wirtschaft Karlsruhe unter der Schirmherrschaft des Ministerpräsidenten des Landes Baden-Württemberg
Ehrungen:
- 1984
- Preis für Technologie-Transfer aus der Forschung in die Wirtschaft des Bundesministers für Forschung und Technologie
- 1988
- Technologie-Transferpreis für herausragende Leistungen aus den Hochschulen des Bundesministers für Bildung und Wissenschaft
- 1989
- Adalbert-Seifriz-Preis von Ministerpräsident Lothar Späth
- 1991
- Adalbert-Seifriz-Preis des Landes Baden-Württemberg
- 1995
- Adalbert-Seifriz-Preis des Landes Baden-Württemberg
- 1996
- Bayerischer Staatspreis
Mitgliedschaften:
- ISBT (International Society of BeverageTechnologists)
- Deutsche Physikalische Gesellschaft/td>
Dipl.-Ing. (FH) Jürgen Bohleber
- 07.10.1965
- geboren in Freiburg im Breisgau
- 1981
- Hauptschulabschluss
- 1981 – 1985
- Berufsausbildung zum Elektromaschinenbauer
Schneider Elektrotechnik, Offenburg - 1985 – 1987
- Konstrukteur Transformatorenbau
Schneider Elektrotechnik, Offenburg
berufsbegleitend: Abendrealschule Offenburg - 1987
- Mittlere Reife
- 1987 – 1988
- Fachhochschulreife, Fachhochschule Offenburg
- 1989 – 1992
- Studium der Elektrischen Energietechnik
Hochschule Karlsruhe Technik und Wirtschaft
Stipendium der Stiftung für Begabtenförderung im Handwerk - 1992
- Abschluss als Diplom-Ingenieur (FH)
- 1993 – 1996
- Inbetriebnahmeingenieur für Anlagentechnik, Siemens AG, Karlsruhe
- 1996 – 1997
- Konstruktionsingenieur Sortiermaschinen, Walter Grässle GmbH & Co. oHG, Pfinztal-Berghausen
- 1997
- Projektleiter Konstruktion Sortiermaschinen, Unisensor Sensorsysteme GmbH, Karlsruhe
- seit 2006
- Stellvertretender Technischer Leiter, Unisensor Sensorsysteme GmbH, Karlsruhe
Ehrungen:
- 1985
- Bundessieger im praktischen Leistungswettbewerb
Zentralverband des Deutschen Elektrohandwerks (ZVEH)
Dipl.-Ing. (FH) Dirk Christian Fey
- 11.03.1968
- geboren in Karlsruhe
- 1984
- Mittlere Reife
- 1984 – 1987
- Berufsausbildung zum Informationselektroniker
(Berufsschule mit Berufskolleg) bei der Siemens AG Karlsruhe - 1987 – 1988
- Fachhochschulreife
- 1988 – 1989
- Grundwehrdienst
- 1989 – 1993
- Studium der Nachrichtentechnik an der Hochschule Karlsruhe Technik und Wirtschaft
- 1989
- Abschluss als Dipl.-Ing. (FH)
- 1993 – 1996
- Entwicklungsingenieur, Steinbeis-Transferzentrum für Optoelektronik und Sensorik, Karlsruhe
- 1996 – 2000
- Projektleiter für Getränketechnologie
UNISENSOR Sensorsysteme GmbH, Karlsruhe - 2000 – 2005
- Entwicklungsleiter für Sensorsysteme und optische Messtechnik
UNISENSOR Sensorsysteme GmbH, Karlsruhe - seit 2005
- Technischer Leiter der UNISENSOR Sensorsysteme GmbH Karlsruhe
Ehrungen:
- 1996
- Bayerischer Staatspreis
Mitgliedschaften :
- ISBT International Society of Beverage Technologists
Contact
Spokensperson
Prof. Dr.-Ing. Gunther Krieg
Unternehmensgründer und Vorsitzender des wissenschaftlichen Beirates
UNISENSOR Sensorsysteme GmbH
Am Sandfeld 11
76149 Karlsruhe
Mobil: +49 (0) 163 / 97 88 414
E-Mail: g.krieg@unisensor.de
Web: www.unisensor.de
Press
Dipl.-Ing. (FH) Oliver Krieg
Assistent to the Management
UNISENSOR Sensorsysteme GmbH
Am Sandfeld 11
76149 Karlsruhe
Tel.: +49 (0) 721 / 97 88 413
Fax: +49 (0) 721 / 97 88 444
Mobil: +49 (0) 179 / 39 25 919
E-Mail: o.krieg@unisensor.de
Web: www.unisensor.de
A description provided by the institutes and companies regarding their nominated projects
The supply of oil is limited. Consequently, the recycling of plastics is becoming increasingly important. How can these valuable recyclable materials be detected in mixed material streams and reused? It is this extremely challenging task which the team surrounding Prof. Dr. Gunther Krieg, Dirk Fey, and Jürgen Bohleber has been addressing for over a decade. The result of this large-scale research and development project bears the name Powersort 200. In developing this product, Unisensor Sensorsysteme GmbH has made a unique technology available to industry that presents entirely new opportunities in the area of material sorting and in the recycling of starting materials.
Plastic is everywhere today, as PET bottles, as housings for electronic equipment and other devices, in vehicle interiors, as food packaging and in many other applications. It is made of valuable raw materials, such as oil or natural gas. 1.9 kilograms of petroleum, for example, and vast amounts of energy are needed to produce one kilogram of polyethylene terephthalate (PET). Yet the supply is limited, and what could be more obvious than to recycle plastics on a large scale? This ensures not only an efficient use of resources, but prevents enormous mountains of waste from accumulating. And ultimately higher profits can also be made with high-quality recycled plastic.
One source of potential difficulty, however, is the proper separation of the individual materials because mixed plastic recycling streams contain not only recyclables, but frequently also other types of plastics, plastics with chlorine or heavy metal compounds as well as contaminants and additives. Using visual, camera-based or other conventional methods, many of these unwanted substances are not able to be identified at all during the recycling process or only to a limited extent. They are often unable to be differentiated by color or any other standard parameters. Even minute particle sizes pose a problem for conventional sorting systems. If the level of impurities in the recycled material is too high, the material is considered poor grade and is limited in the extent to which it can be reused.
Ultra-High-Speed Laser Spectroscopy with Powersort 200
Powersort 200 starts where visual or other established systems and detection processes reach their limits. The system uses a highly efficient and accurate detection process based on ultra-high-speed laser spectroscopy: it identifies the material in a plastic flake or granulate stream based on its specific optoelectronic spectrum and sorts it in only one process step, separating various impurities and contaminants from the stream.
The system was originally developed at the instigation of a major beverage producer with the goal of returning 100 percent of the PET non-returnable bottles they put into circulation back into a closed recycling loop and of stopping the accumulation of mountains of waste. Powersort 200 makes PET recycling possible today in food-grade quality within the framework of bottle-to-bottle recycling, for example.
The powerful, efficient system also reveals its strengths in other areas of plastics recycling. It can also reliably separate dark or black mixed plastics found in the interiors of all vehicles, for example.
The Physical “Fingerprint”
Powersort 200 identifies the different plastics on the basis of their characteristic optical spectrum, their physical “fingerprint”. In this process, high-energy laser light excites individual components to fluoresce or to Raman scattering. The light emitted by the materials is recorded for subsequent spectroscope analysis wherein the measured range extends from ultraviolet to visible light to the near infrared. This wide-band and highly differentiated spectrum makes an accurate material analysis possible and thus a differentiation between recyclable material and impurities. In principle, all material streams can be detected and separated in this way whose molecules can be excited to fluoresce or are Raman-active.
Due to the system’s multispectral, fast optical design as well as an incredibly fast signal processing speed with powerful signal processors, up to one million spectra are generated and evaluated per second. With the help of this high resolution even minute particles with a surface area of only one square millimeter can be analyzed and sorted.
Once a particle in the input stream is identified as an impurity, a number of supersonic air jets remove it from the material stream. The distance between measuring field and air blast mechanism is extremely short and, together with the option of setting detection thresholds and air blast unit for specific materials, results in a very low incorrect reject rate. Depending on the type of impurity or contaminant, Powersort 200 can remove over 98 percent with a minimal loss of recycled material.
PET in Food-grade Quality
Plastic recyclables contaminated by impurities can cause considerable problems and compromise quality during downstream processing. In the area of PET recycling, for example, these are PVC, nylon, silicone, PET with TiO2, PLA, PC, glue / salt or paper as well as flakes with barrier materials (such as scavenger, blends, or multilayers) – typical impurities which are not easily differentiated visually from PET material. These contaminants result in lower transparency, discoloration, and ultimately to poor quality due to cracks or inclusions during subsequent processing, such as during the production of new PET bottles for beverages, for example.
Powersort 200 detects impurities and contaminants, separates them from the material stream and thus ensures the high quality of the recyclate, ensuring even its suitability for direct food contact applications. This is where conventional detection systems are unsuccessful because PET contaminated with transparent, PVC, nylon or other materials cannot or only with great effort be differentiated visually from pure PET in crushed form. It is not until the flakes or granulates undergo further processing and are thus subjected to high temperatures that these impurities become visible in the final product as discolorations. It is also difficult, for example, to detect brown wood and glue residues in brown PET. Powersort 200, however, is able to detect and sort out the different materials reliably on the basis of their specific spectrum, the physical fingerprint. This method also works for the fractionation of black mixed plastics.
Following a successful market launch in 2008, the Powersort system is now being used worldwide by leading recyclers. One of these companies is NURRC in Spartanburg, USA that produces up to 50,000 tons of recycled food-grade PET annually using Powersort 200. According to the company, global carbon footprint is reduced by a million tons by the plant in Spartanburg alone. To achieve the same results, 215,000 cars would have to be taken off the streets.
The Challenge of Waste Electrical and Electronic Equipment
The greatest challenge for the immediate future is the recycling of crushed plastic waste from waste electrical and electronic equipment, for example, the casings of computers, TV’s or household appliances. Several hundred-thousand tons of waste are produced in Germany alone by recycling waste electrical and electronic equipment. To date, the bulk of this plastic waste was only thermally treated or exported to Asia where poor quality plastic recyclates are produced from waste under conditions that are questionable in regard to their toxicity for humans and the environment. For value-based recycling, the different polymer grades must be identified and sorted. It is also necessary to remove waste plastics containing hazardous substances , such as toxic fire retardants, which may no longer be used. By removing them from the material stream by means of laser spectroscope, electrical and electronic waste can be reused in new electrical and electronic equipment in the future. Waste thus becomes a valuable resource.
About Unisensor:
Unisensor Sensorsysteme GmbH is a family-run, innovative high-tech company in the field of process technology. Unisensor’s product portfolio includes internationally patented systems for the beverage, gas, printing and recycling industry as well as for the field of energy technology.
Twenty years ago, Prof. Dr. Gunther Krieg paved the way for extraordinary innovations with the founding of the company and his many years of experience in the field of optoelectronics and sensor technology. Since then a team of highly qualified staff working closely with industry and technical universities have been developing groundbreaking technical solutions and products which are used around the world and have set new standards in process technology.
The right to nominate outstanding achievements for the Deutscher Zukunftspreis is incumbent upon leading German institutions in Science and Industry as well as foundations.
The project “Laser Light finds Recyclable Materials – Resources for Our Future” was nominated by the AiF – The German Federation of Industrial Research Institutions.
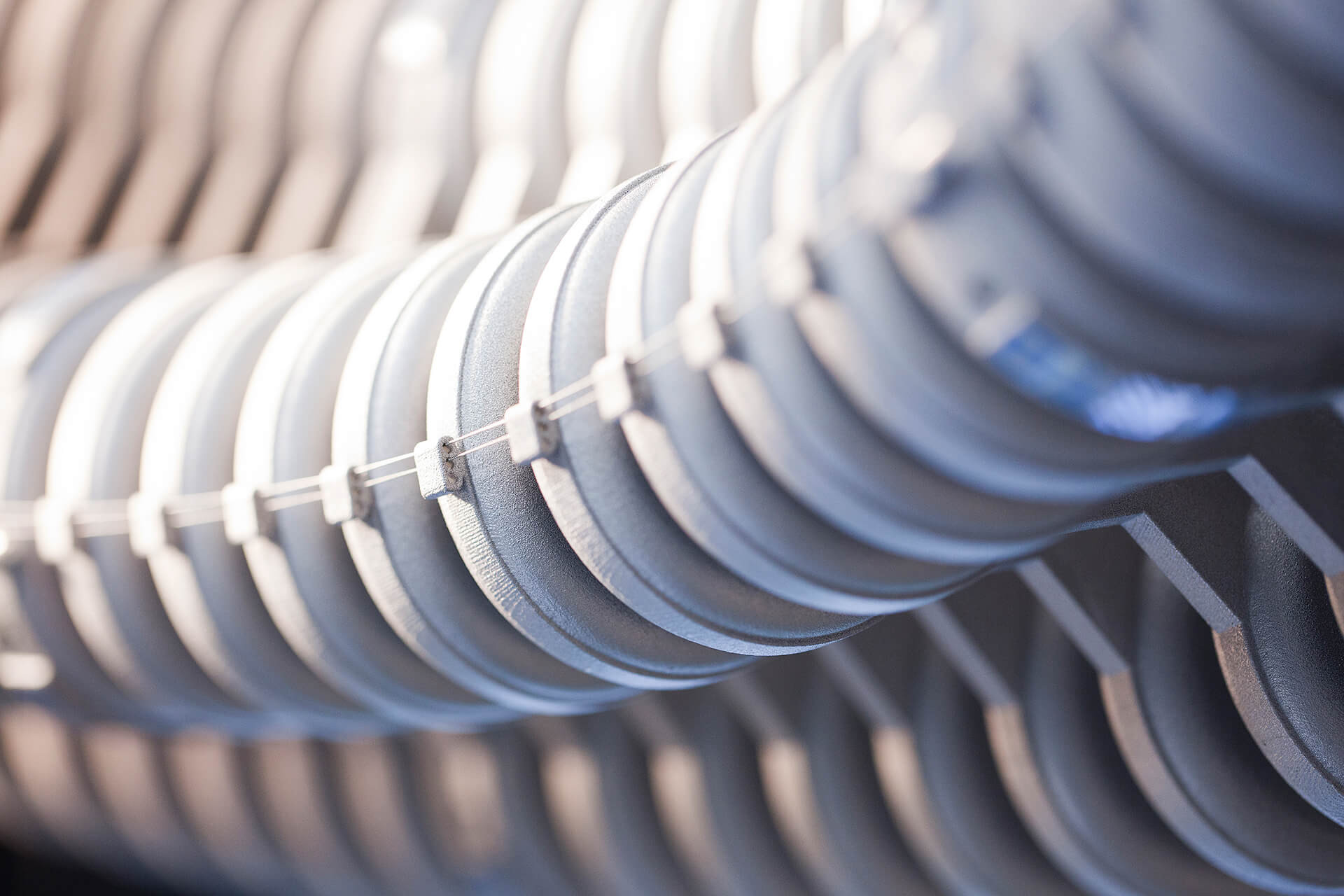