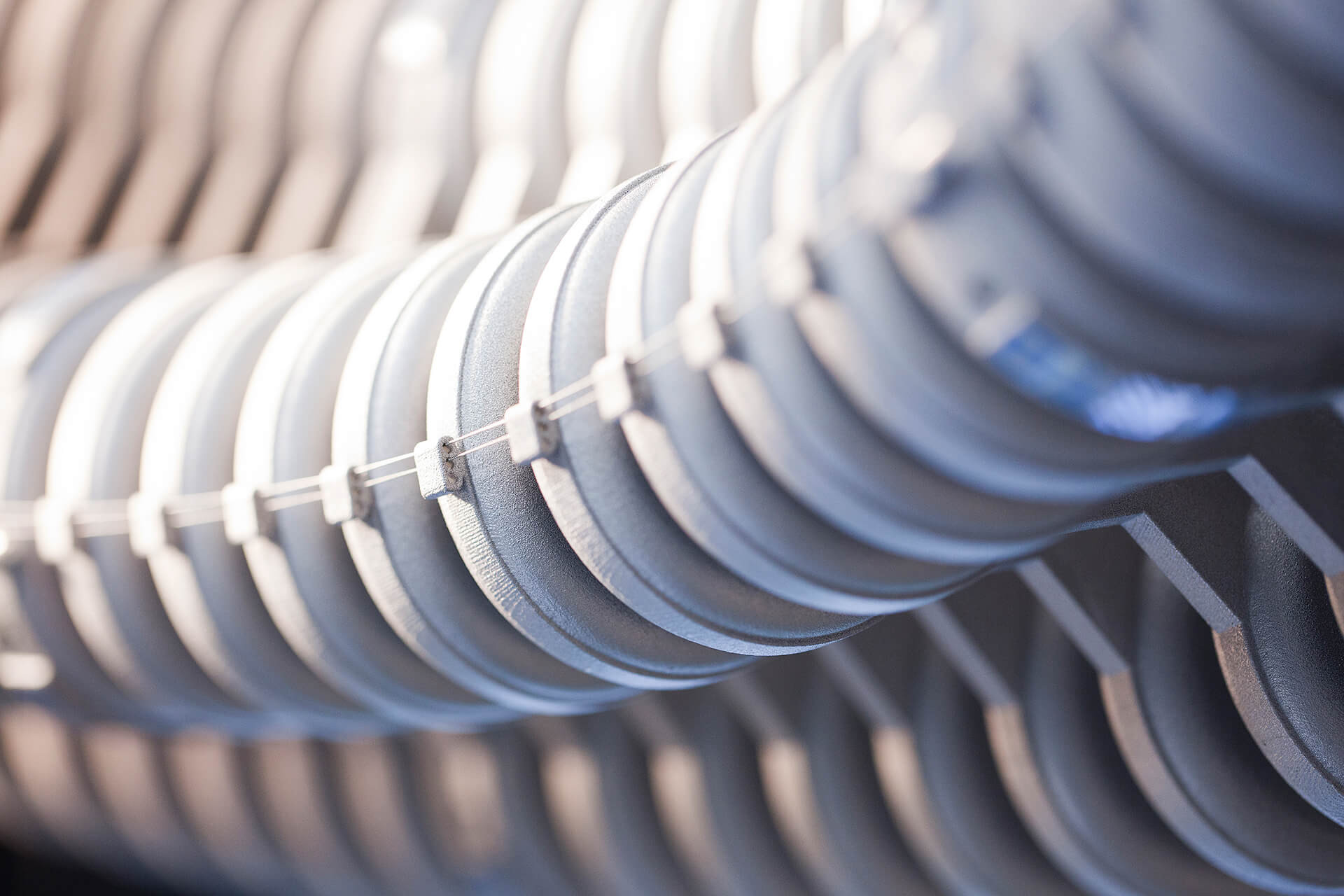
Winner 2010
Vorbild Elefantenrüssel
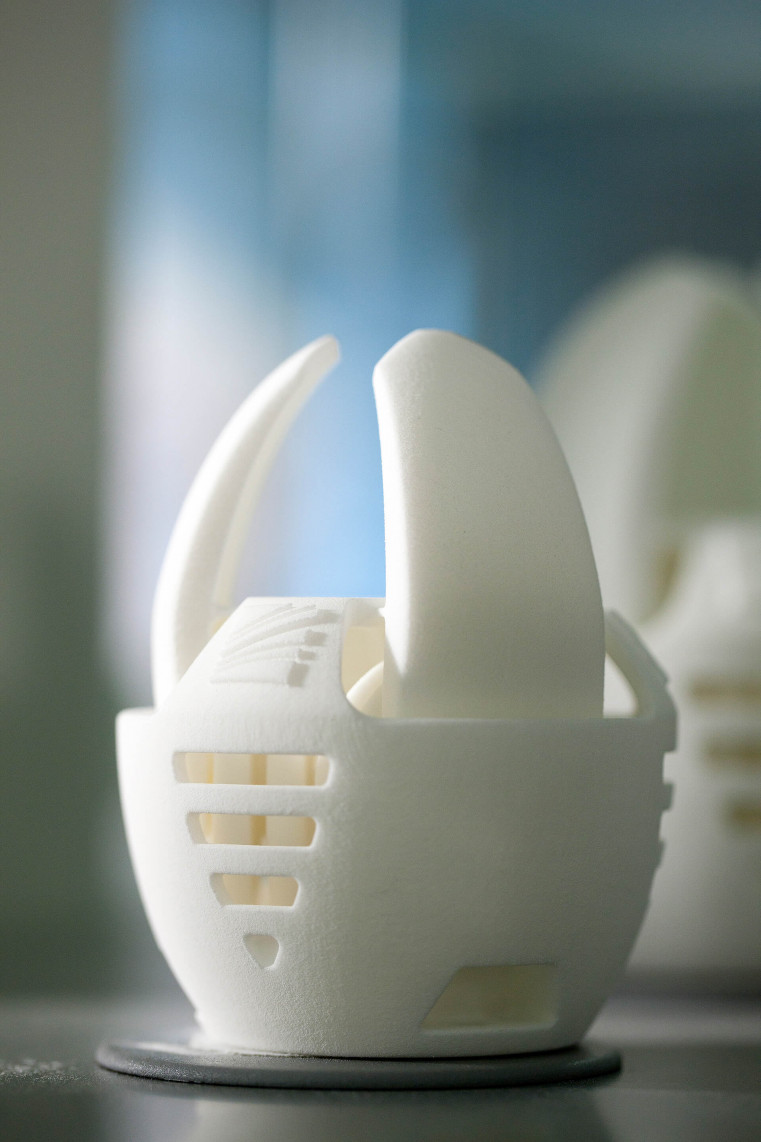
Dr.-Ing. Peter Post, Dipl.-Ing. (FH) Markus Fischer and Dipl.-Ing. (FH) Andrzej Grzesiak found the answer to this question in Nature: Using the principle of bionics, the researchers applied natural design principles to an assistance system, evolving them to create a unique handling system with almost human agility, dexterity, and flexibility – light, free-moving and compliant. It can assist humans safely. Peter Post heads the research and development project at Festo; Markus Fischer is responsible for the company’s corporate design – and established the Festo Bionic Learning Network in 2006 in which the company and universities together implement technical concepts modeled on nature. Andrzej Grezsiak is the cooperation partner for the project and head of the Generative Manufacturing group at the Fraunhofer Institute for Manufacturing Engineering and Automation IPA.
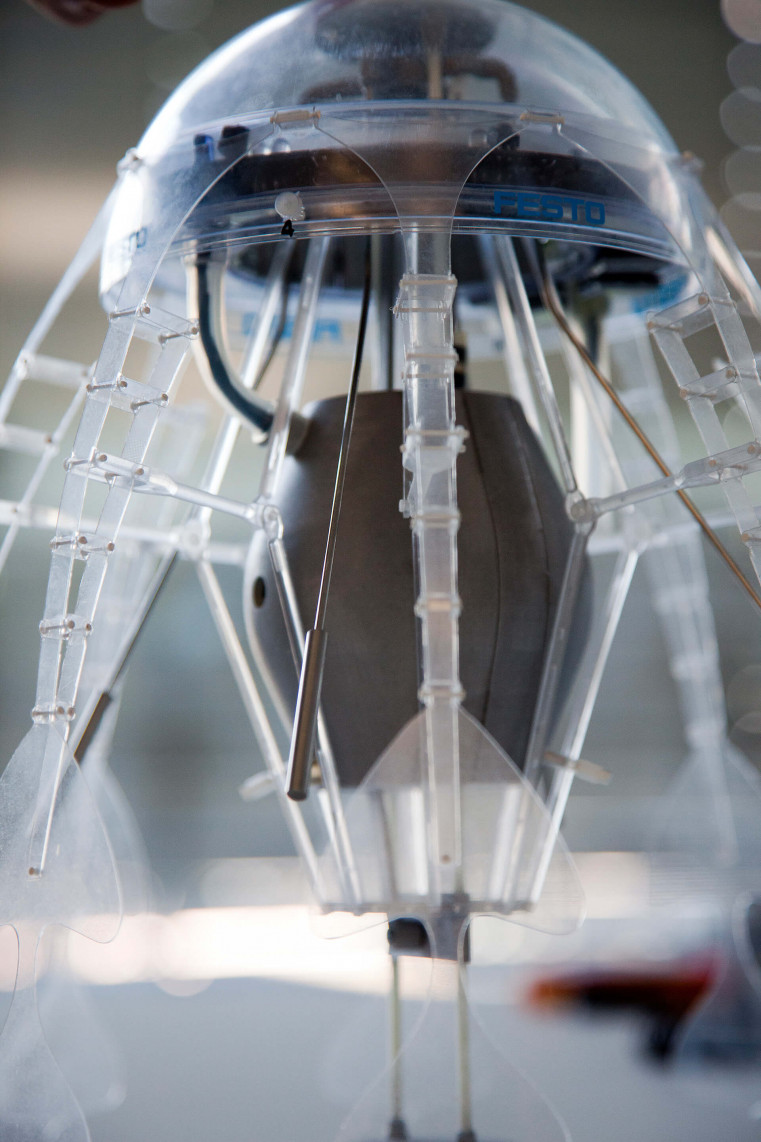
The prototype of the “Bionic Handling Assistant” which the three nominated scientists developed resembles an elephant’s trunk. It consists of an artificial trunk, a hand axis and a gripper with three fingers.
more details
Resumes
Dr.-Ing. Peter Post
- 30.07.1959
- geboren in Haiger/Hessen
- 1975 – 1978
- Facharbeiterausbildung zum Werkzeugmacher
- 1980 – 1984
- Studium Allgemeiner Maschinenbau an der Universität Siegen, Siegen
- 1984
- Diplomarbeit, Thema: Interaktive Lösungsverfahren nichtlinearer Vektoroptimierungsprobleme aus der Strukturmechanik
- 1984 – 1989
- Wissenschaftlicher Mitarbeiter, Institut für Mechanik und Regelungstechnik an der Universität Siegen, Forschungschwerpunkt "Strukturoptimierung von Large-Scale- Systemen"
- 1988
- Promotion, Thema: Optimierung von Verbundbauweisen unter Berücksichtigung des zeitabhängigen Materialverhaltens
- 1989 – 1991
- Forschungsingenieur, Festo AG & Co. KG, Esslingen
- 1991 – 1995
- Leiter Computer Aided Engineering, Festo AG & Co. KG, Esslingen
- 1995 – 2008
- Leiter Forschung, Festo AG & Co. KG, Esslingen
- Seit 2009
- Leiter Research and Programme Strategy, Festo AG & Co. KG, Esslingen
Weitere Tätigkeiten:
- Vorsitzender des Forschungsfond des VDMA Fachverbands Fluidtechnik
- Stellvertretender Aufsichtsratsvorsitzender Hahn Schickard Gesellschaft, Stuttgart
- Member of the Board EFFRA - European Factory of the Future Research Association
- Sprecher Manufuture Germany, Technologieplattform Manufuture
Ehrungen:
- 1985
- Alfred Schaber Medaille der Universität Siegen
Dipl.-Ing. (FH) Markus Fischer
- 18.09.1966
- geboren in Kirchheim unter Teck, Baden-Württemberg
- 1983
- Realschulabschluss, Realschule Weilheim a. d. Teck
- 1983 – 1986
- Ausbildung zum Werkzeugmacher, Firma Kammerer, Holzmaden
- 1986 – 1988
- Fachgebundene Hochschulreife, Technische Oberschule Stuttgart
- 1988 – 1989
- Grundwehrdienst, Panzergrenadierbataillon 282, Dornstadt
- 1989 – 1991
- Studium der Holztechnik, Fachhochschule Rosenheim
- 1991 – 1996
- Studium der Architektur, Fachhochschule Augsburg
Diplomarbeit: „Systemstudie wohnen“ in Kooperation mit dem Institut für Biologie und Umwelt GmbH von Prof. Dr. Dr. h.c. Frederic Vester in München - 1996 – 1997
- Freie Mitarbeit im Büro für Gestaltung Prof. Eberhard Stauß und Ursula Wangler, München
- 1998 – 2000
- Gesellschafter im Planungs- und Gestaltungsbüro Baldauf & Fischer, Baienfurt, Baden-Württemberg
- 2000 – 2001
- Gestalter, Büro Uebele, visuelle Kommunikation, Stuttgart
- 2001 – 2005
- Corporate Designer Festo AG & Co. KG, Esslingen
- Seit 2006
- Leiter Corporate Design, Festo AG & Co. KG, Esslingen
Ehrungen:
- 2001
- Red Dot Award
Type Directors Club New York
DDC Silber
ISTD, International TypoGraphic Award London - 2002
- Art Directors Club New York
Art Directors Club Berlin - 2003
- IF Award
Chicago Athenaeum Award - 2007
- Red Dot Award
Design Management Award Europe - 2009
- Invention Award, Festo AG
- 2010
- Designpreis der Bundesrepublik Deutschland
Dipl.-Ing. Andrzej Grzesiak
- 2.11.1972
- geboren in Wroclaw (Breslau), Polen
- 1992
- Abitur, Elektroniczne Naukowe ELWRO Wrocław (Polen)
- 1992 – 1994
- Studium der Elektrotechnik an der Technischen Universität Wroclaw (Polen)
- 1994 – 2003
- Studium der Elektrotechnik an der Universität Stuttgart
Diplom Thema: Analysis of the applicability of SQMA to fault analysis - 2003 – 2006
- Wissenschaftliche Mitarbeiter am Institut für Industrielle Fertigung und Fabrikbetrieb (IFF) der Universität Stuttgart
- Seit 2006
- Gruppenleiter am Fraunhofer-Institut für Produktionstechnik und Automatisierung IPA in Stuttgart
- Seit 2008
- Sprecher der Fraunhofer-Allianz Generative Fertigung
Weitere Tätigkeiten:
- Germany representative of The Global Alliance of Rapid Prototyping Associations (GARPA)
- Management-Board der Europäischen Rapid Manufacturing Platform (Additive Manufacturing) und Koordination der Deutschen Rapid Manufacturing Plattform
- Mitglied des VDI Fachausschusses Rapid Prototyping /Rapid Manufacturing
Contact
Spokesperson
Dr. Peter Post
Leiter Research and Programme Strategy
Festo AG & Co. KG
Ruiter Straße 82
73734 Esslingen
Tel.: +49 (0) 711 / 34 73 144
Fax: +49 (0) 711 / 34 75 44 078
E-Mail: pos@de.festo.com
Web: www.festo.com
Press
Paul Kho
Leiter Technical Corporate Communication
Festo AG & Co. KG
Abteilung CC-T
Ruiter Straße 82
73734 Esslingen
Tel.: +49 (0) 711 / 34 74 078
Mobil: +49 (0) 173 / 31 93 795
Fax: +49 (0) 711 / 347 54 – 40 78
E-Mail: pkh@de.festo.com
Web: www.festo.com
Dipl.-Wirt.-Ing. (FH) Axel Storz
Fraunhofer-Institut für Produktionstechnik und Automatisierung IPA
Presse und Öffentlichkeitsarbeit, Marketing
Nobelstr. 12
70569 Stuttgart
Germany
Tel.: +49 (0) 711 / 97 03 660
Fax: +49 (0) 711 / 97 01 400
Mobil: +49 (0) 172 / 71 48 542
E-Mail: axel.storz@ipa.fraunhofer.de
Web: www.ipa.fraunhofer.de
A description provided by the institutes and companies regarding their nominated projects
A look at the latest technical developments in private and industrial domains clearly reveals that these developments will only be considered innovations and accepted by the market when they effectively combine an affordable price, user friendliness, and new technological principles.
Considering technologies are playing an ever more important role in our lives and the increasing use of technology in our lives, the time has come to take a close look at the new constellations of man and technology in all its complexity. The greatest potential is in the cooperation between humans and technology, which provides a platform on which to perform pioneering research on the efficient interaction of man and machine. The ever more important field of health research is also looking for systems which use technology to enable independent, self-determined life.
Taking inspiration from nature, Festo has developed the Bionic Handling Assistant modeled on an elephant’s trunk. It is an adaptable assistance system that allows man and machine to interact effectively as a team and without risk. What makes the Bionic Handling Assistant system so unique is its safe and compliant behavior. Conventional systems and industrial robots are not compliant. They are designed for stiffness, resulting in heavy configurations that are not entirely without danger for the operator. Contact between man and robot is only possible with permanently installed safety devices such as protective screens or the use of costly shielding.
The Bionic Handling Assistant is a pioneering step towards identifying practical applications which improve the quality of life for people in all stages of life. The merging of new technologies and the social environment can pave the way for handling assistant systems used in industry and the private home – and on terms that are well below the price segment of conventional handling systems and robots.
The project was developed within the framework of Festo’s Bionic Learning Network. The Bionic Learning Network is group of affiliated universities, institutes and development companies dedicated to applying bionics, i.e. transferring principles of biology to technology, to produce leading-edge technologies. With bionics, automatic sequences of motion can be designed to be even more energy efficient and productive, providing industry with innovative solutions to be put into practice. Drawing on nature, the focus is on effective principles that “follow the model of nature”.
The Bionic Handling Assistant: a combination of numerous cross-functional technologies
The engineers and designers at Festo and the Fraunhofer IPA make use of new generative manufacturing technologies combined with mechatronics, handling technologies and bionics. They are at the foundation of the innovative design of the Bionic Handling Assistant which is similar in function to that of an elephant’s trunk. The project was based on the development of pneumatic lightweight structures by Professor Dieter Mankau at the Offenbach Academy of Art and Design (HfG). The Bionic Handling Assistant’s configuration was based on this design, consisting of three basic elements for spatial movement, along with a hand axis and a gripper with adaptive fingers.
Together these technological advantages offer an innovative potential that can be used as an autonomous assistance system. A similar project entitled Ambient Assisted Living (AAL) is currently being conducted by the Federal Ministry of Education and Research (BMBF) which is referred to in Germany’s high-tech strategy 2020. The focus of the project includes health research in particular and promotes systems that will simplify autonomous living through the use of technology. These aids will require assistance systems which are absolutely user-friendly and can thus be safely integrated directly in living environments.
The Fraunhofer-Gesellschaft, Europe’s largest application-oriented research organization, identified direct contact between man and technology as a leading field of innovation as early as 2003. Research focuses on the complex interaction of human and technical change. Considering technologies are playing an ever more important role in our lives and the increasing use of technology in our everyday existence, it is time to take a close look at the innovative constellations of man and technology in all its complexity. Technological innovations like the Bionic Handling Assistant push research in Ambient Assisted Living and envision the duet of “Man and Technology” as a team with a future.
There is great potential in industry to integrate the Bionic Handling Assistant in automation and production technology as a handling system to assist assembly. Areas of application include inspection and quality assurance, for example of machine frames, or also maintenance and cleaning tasks in areas difficult to access, but in which the Bionic Handling Assistant can make use of its advantages because of its free maneuverability. The Bionic Handling Assistant can also provide valuable services in preventive maintenance.
Compliance due to compressed air – Safe interaction between man and machine
The unique selling proposition of the Bionic Handling Assistant is its safe flexible and compliant behavior. Flexibility in this case is defined both as the structure – specifically, the material and design – as well as control and actuation. The mechanical structure of the Bionic Handling Assistant is flexible and can be programmed to execute a defined motion in space. Even in the event of a collision or a malfunction, the Bionic Handling Assistant poses no risk to persons, objects or individuals in its environment.
The compliant behavior is determined by the system’s pneumatics since air is compressible medium. This drive technology is thus predestined to achieve closer cooperation between man and machine. Compressed air moves the structure and the grippers. The function of the grippers is based on the bionic Fin Ray Effect® of Leif Kniese (Evologics GmbH). The fingers of the gripper adapt to the contour of the object to be grasped while exerting lateral pressure, thereby fixing the hold on similarly sized parts. Given the state of the art, other industrial grippers cannot guarantee their grasp of dissimilar objects because of their rigid mechanisms and hard materials.
Lightweight design with generative manufacturing technologies
The key word is manufacture: by using the latest findings in generative manufacturing technology, additional innovative features become available for the Bionic Handling Assistant. Additive manufacturing is used to produce customized, movable system parts made of polyamide applied in thin layers to a substrate during production. Every layer is fused with the layer below using a laser and only hardens in the areas defined by the control program. This enables 3D printing of sophisticated product geometries.
The result is lightweight flexible structures capable of exerting ample force. Another advantage: these sophisticated systems are produce without extravagant assembly processes and expensive tool costs. The high flexibility and low density of the polyamide at only 0.95 gm per cubic centimeter are ideal for the optimal strength to weight ratio of the Bionic Handling Assistant. Its entire body including the grippers is produced using additive manufacturing.
In future, generative manufacturing technologies will enable customized and sustainable manufacturing of sophisticated products due to its high flexibility and low resource consumption – even in process chain in which a large number of integrated functions is required. This technology paved the way for the cooperation between Festo and the Fraunhofer IPA on the development of the Bionic Handling Assistant.
Partnership between Festo and Fraunhofer IPA
Festo has been chiefly responsible for the development and design of the Bionic Handling Assistant. To complement their own core competence the Festo team enlisted the support of generative manufacturing experts from the Fraunhofer Institute for Manufacturing Engineering and Automation IPA as partner. The team was able to utilize the expertise of Fraunhofer IPA in the area of rapid manufacturing, particularly for the development of the expansion bellows.
As a system provider of automation technology, Festo’s Bionic Handling Assistant is a prototype that virtually triggers industrial applications in assembly support. The evolution curve of a classic handling system starts with a standard linear axis, finds its continuation over the space portal and the classic tripod to the bionic tripod. This now culminates in the Bionic Handling Assistant with its compliant handling kinematics and highly innovative individual components – grippers, control and actuation –.
About Festo
Festo is a leading international supplier of automation technology. With its innovations and problem-solving expertise in the field of pneumatics and electronics, the company has established itself as the performance leader in its sector. Festo’s innovative strength is demonstrated by over 100 new products which it launches every year and the 2,900 patents it holds worldwide. Its new approach to product development using bionics and biomechatronics within the framework of the Bionic Learning Network, represents a true first in the field of automation technology.
About Fraunhofer IPA
The research and development focus of the Fraunhofer Institute for Manufacturing Engineering and Automation IPA is on organizational and technological tasks related to production. Since 2005, the institute has been aiding partners and clients both in the planning and design of new products as well as the redesigning and optimization of existing product lines using generative manufacturing processes.
The right to nominate outstanding achievements for the Deutscher Zukunftspreis is incumbent upon leading German institutions in Science and Industry as well as foundations.
The project “Modeled on an Elephant’s Trunk – A High-tech Helper for Industry and the Home” was nominated by acatech – The German Academy of Science and Engineering.
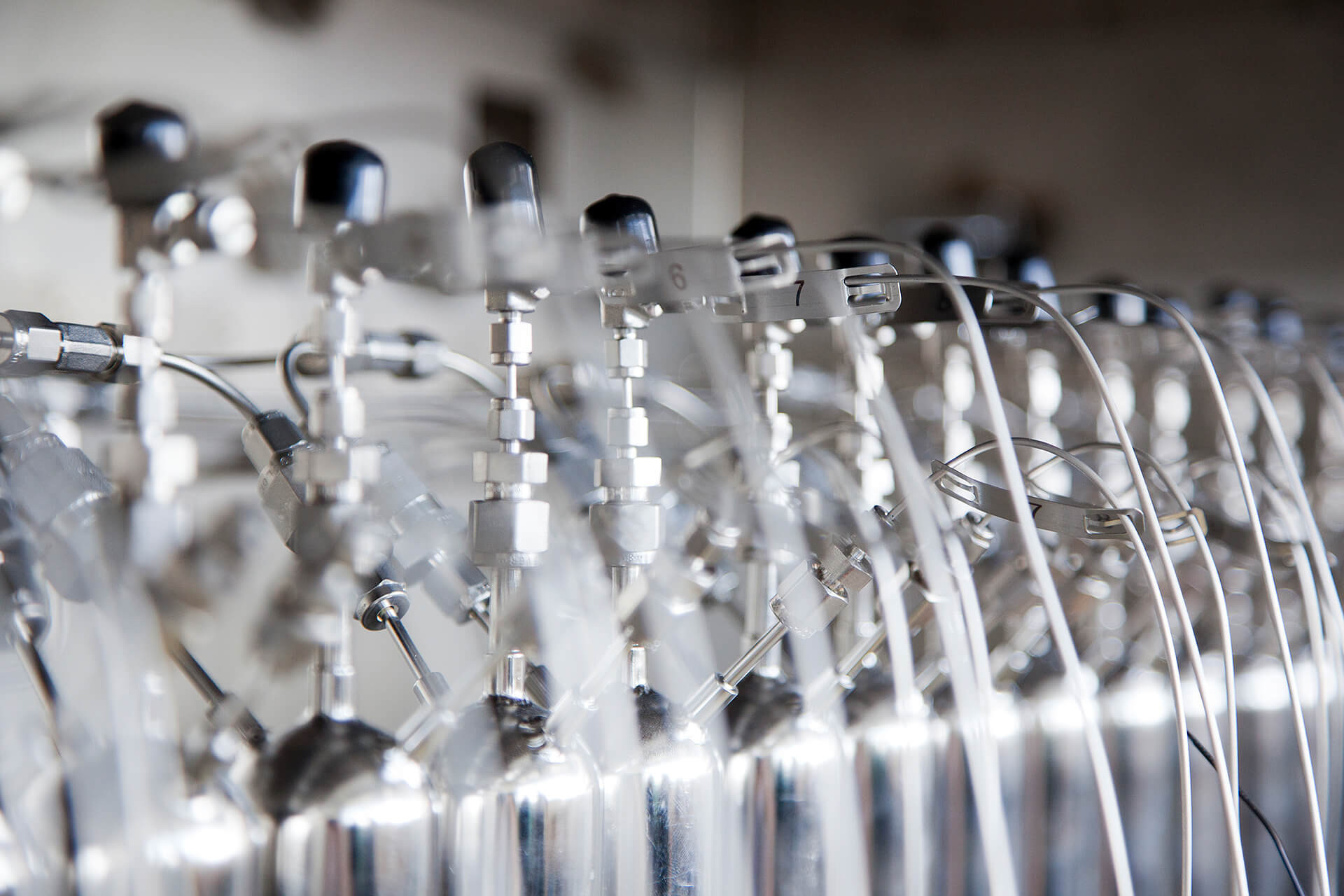