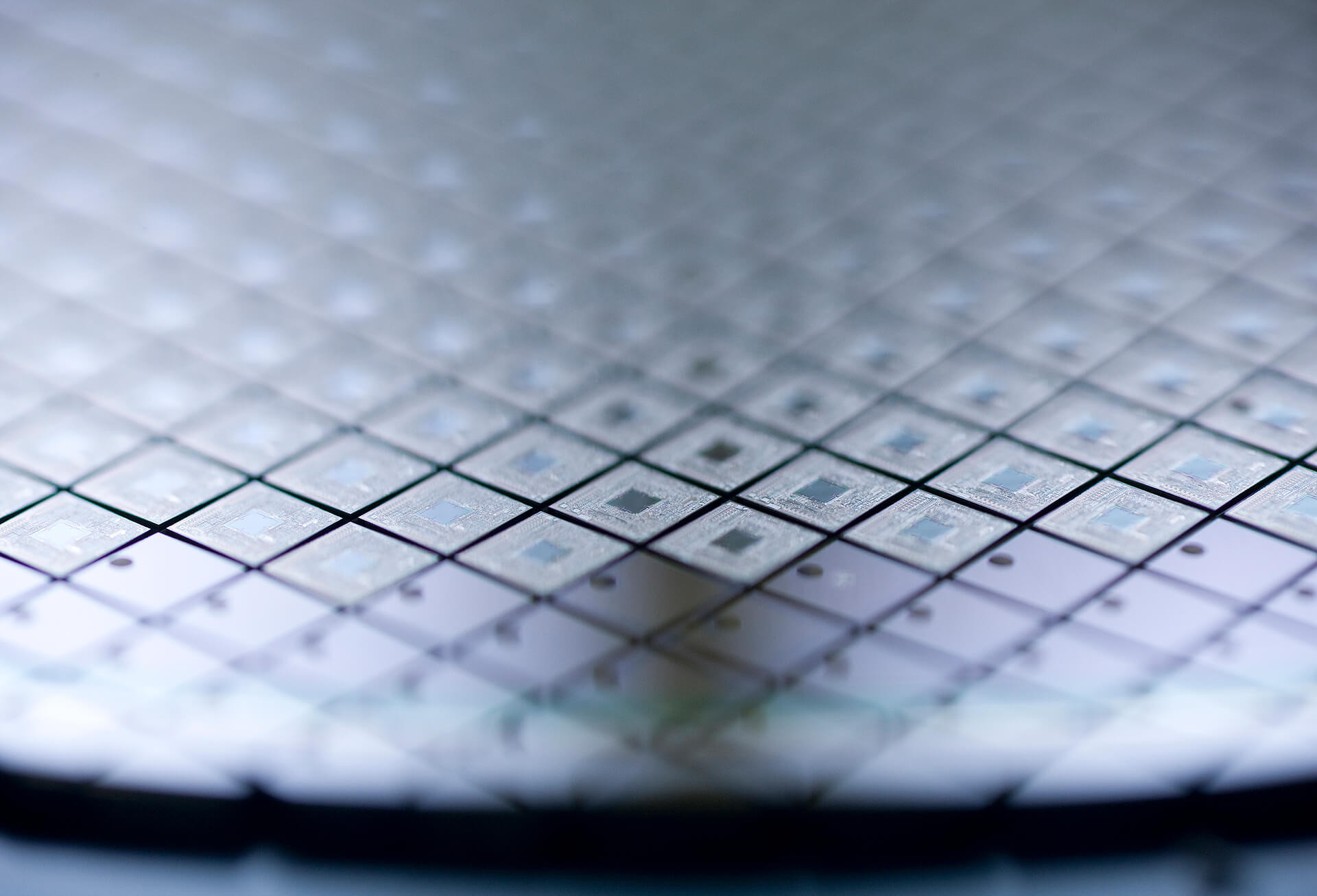
Winner 2008
Smarte Sensoren
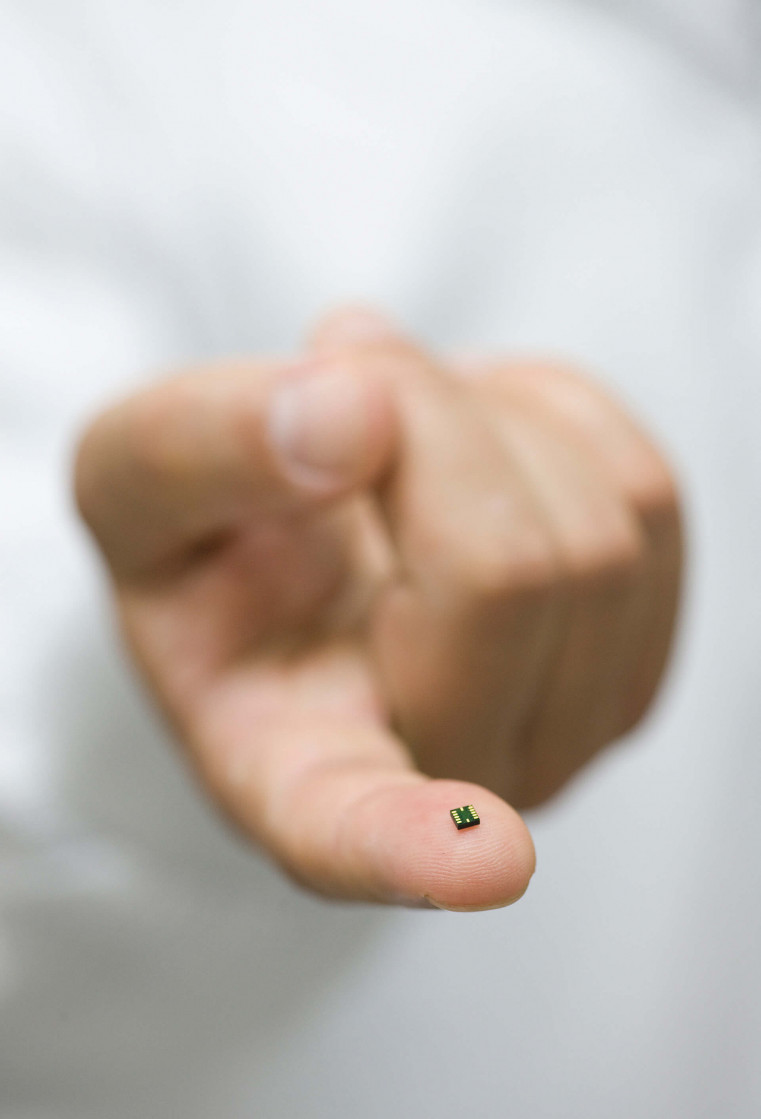
The answer: They have to be made smaller and be more cost-efficient in the production of large quantities than in the past. Jiri Marek, Michael Offenberg, and Frank Melzer have shown has it’s done. Jiri Marek is Development Manager Sensors, Michael Offenburg Group Manager Application Sensors at Robert Bosch GmbH, Frank Melzer Managing Director of Bosch Sensortec GmbH in Reutlingen.
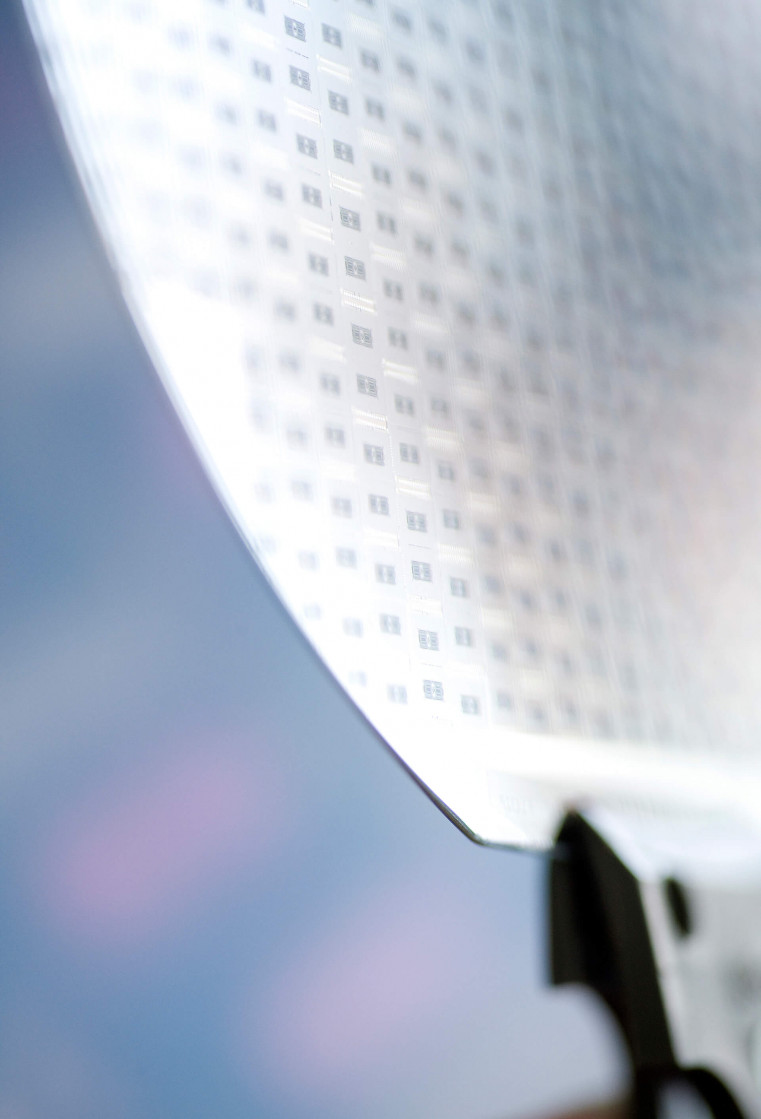
Sensors keep vehicles on their intended path and prevent skidding
The Electronic Stability Program (ESP), developed at Bosch and now fitted into most new cars, has drastically reduced the number of fatal car accidents due to skidding. At the heart of the ESP system are micromechanical sensors: minute measuring instruments made of silicon, consisting of movable components and detect skid conditions of the vehicle early enough to allow the car’s technology to take corrective action. New mid-sized class cars have up to one hundred sensors that monitor safety or provide the lowest possible fuel consumption.
more details
Resumes
Dr.-Ing. Jiri Marek
- 11.12.1956
- geboren in Prag, Tschechische Republik
- 1974 – 1979
- Studium der Elektrotechnik an der Universität Stuttgart
- 1978
- Auslandsaufenthalt an der Stanford University, USA
- 1979
- Diplomarbeit
- 1983
- Promotion am Max-Planck-Institut für Festkörperforschung in Stuttgart und an der Universität Stuttgart
- 1983
- Postdoctoral Fellow, IBM-Forschungslabor, San José, USA
- 1984 – 1986
- Entwicklungsingenieur bei Hewlett-Packard, Optical Communication Division, in Palo Alto, USA
- 1987 –1988
- Assistent der Geschäftsleitung bei der Robert Bosch GmbH, Reutlingen
- 1988 – 1989
- Gruppenleiter Design Sensoren, Robert Bosch GmbH, Reutlingen
- 1990 – 1999
- Abteilungsleiter Entwicklung Sensoren, Robert Bosch GmbH, Reutlingen
- 2000 – 2003
- Entwicklungsleiter Rückhaltesysteme und Sensoren, Robert Bosch GmbH, Reutlingen
Ernennung zum Leitenden Direktor - 2004 – 2005
- Vice President Engineering Sensors, Robert Bosch GmbH, Reutlingen
- seit 2005
- Senior Vice President Engineering Sensors, Robert Bosch GmbH, Reutlingen
Dr.-Ing. Michael Offenberg
- 24.01.1957
- geboren in Meppen
- 1976
- Studium der Elektrotechnik an der Rheinisch-Westfälische Technische Hochschule Aachen (RWTH)
- 1983
- Diplom am Institut für Werkstoffkunde der RWTH, Aachen
Thema: „Einfluß der remanenten Polarisation auf die dielektrischen Eigenschaften ferroelektrischer Keramik" - 1983 – 1988
- Promotion am Institut für Halbleitertechnik RWTH, Aachen
Thema: „Die Struktur von Defekten in dotiertem Siliciumdioxid“ - 1989 – 1990
- Postdoktorand IBM Research, T.J. Watson Research Center, Yorktown Heights, USA
- 1990 – 1997
- Entwicklung mikromechanische Prozesse, Robert Bosch GmbH, Reutlingen
- 1998 – 1999
- Projektleiter Sensorapplikation, Robert Bosch GmbH, Reutlingen
- seit 2000
- Gruppenleiter Applikation Sensoren, Robert Bosch GmbH, Reutlingen
Dr.-Ing. Frank Melzer
- 15.08.1963
- geboren in Göppingen
- 1983 – 1990
- Studium des Maschinenbaus an den Universitäten Stuttgart, Brunel, London, England und University of Arizona, USA
- 1994
- Promotion, Universität Stuttgart
- 2003
- MBA, Rotman School of Management, University of Toronto, Kanada
- 1994 – 1996
- Entwicklungsingenieur bei der Robert Bosch GmbH, Electrical Drives, Bühlertal
- 1996 – 1999
- Gruppen- und Abteilungsleiter Vorausentwicklung bei der Robert Bosch GmbH, Electrical Drives, Bühlertal
- 1999 – 2001
- Assistent der Geschäftsführung bei der Robert Bosch GmbH, Stuttgart
- 2001 – 2003
- Produktbereichsleiter Filter bei der Robert Bosch España Gasoline Systems S.A, Alcalá de Henares, Spanien
- 2003 – 2004
- Restrukturierungsteam bei der Robert Bosch GmbH, Stuttgart
- seit 2004
- Geschäftsführer bei der Bosch Sensortec GmbH, Reutlingen
Contact
Spokesperson
Dr.-Ing. Jiri Marek
Entwicklungsleiter Sensoren
Automotive Electronics
Robert Bosch GmbH
AE/NE4
Tübinger Straße 123
72762 Reutlingen
Tel.: +49 (0) 7121 / 35 43 00
E-Mail: jiri.marek@de.bosch.com
Web: www.bosch.de
Press
Thomas Knoll
Forschung und Vorausentwicklung und Kraftfahrzeugtechnik
Robert Bosch GmbH
Corporate Communications
Postfach 10 60 50
70049 Stuttgart
Tel.: +49 (0) 711 / 81 17 088
Fax: +49 (0) 711 / 81 17 656
E-Mail: thomas.knoll@bosch.com
Web: www.bosch.de
A description provided by the institutes and companies regarding their nominated projects
The World of Micromechanics
Micromechanics evolved from semiconductor technology in the eighties. Its goal is to apply the methods used in semiconductor micromanufacturing (coating, structuring, etching) to silicon disks, so-called wafers, to machine very small mechanical structures and components. One of the best known systems that uses these kinds of micromechanical sensors is the Electronic Stability Program (ESP) for motor vehicles developed by Bosch which, according to recent studies, is capable of reducing by 30 to 50% the number of fatal accidents due to skidding.
The merits of micromechanics are:
- minute structure dimensions of just a few micrometers as a prerequisite for miniature sensors;
- using the cost-effective methods of semiconductor technology to manufacture small, powerful, and energy-saving sensors;
- Low-cost fabrication of many thousands of components on one silicon wafer.
Two fundamentally different methods are currently used to produce these components: bulk micromachining and surface micromachining.
- In bulk micromachining, the required structures are machined over a relatively large surface area of a silicon wafer.
- Surface micromachining, in contrast, layers freely movable structures onto the surface of the silicon wafer – masses and spring elements; this has the advantage that the structures are considerably smaller and can easily be machined with the processes used for semiconductors.
Micromechanical sensors have in the past almost exclusively been used in the automotive sector to lower fuel consumption and emissions, to protect passengers with passive safety systems, such as airbag systems, or to prevent skidding by means of active safety systems such as Bosch’s ESP system. Widespread use in consumer electronics, however, was completely out of the question in the past. Sensors were too large, used too much power, and were too expensive in production.
Consumer electronics make other demands of micromechanical sensors:
- the available package dimensions are extremely limited, for example, in mobile phones, laptops, or mobile GPS navigation systems;
- power consumption must be minimal so that mobile energy stores such as batteries have a long lifetime;
- given the extremely short lifecycles of products, the development times have to be short;
- the cost of fabrication must be considerably lower than for the automotive sector.
The current innovation
The nominated Bosch research team succeeded in developing a series of processes for surface micromachining and to transfer them to large batch production. The sensors fabricated using this process meet the demands of consumer electronics and open up an unexpected range of new functions. Experts consider the processes developed by Bosch to be a technical breakthrough for the industrial use of surface micromachining. The five key processes developed at Bosch are:
- The deposition and structuring of layers made of polycrystalline silicon to create a layer no more than 20 micrometers thick – which are necessary for the largest possible, freely moving masses in the smallest package, as are needed in acceleration sensors.
- Deep Reactive Ion Etching – DRIE – or the “Bosch process”. This method is used to produce dimensionally accurate deep structures with vertical walls.
- Sacrificial etching to remove the sacrificial layer easily and reliably.
- The thin-film cap in the “MEMS-first process”. It hermetically seals micromechanical components in very limited space from environmental influences.
- The “APSM process” (Advanced Porous Silicon Membrane) for pressure sensors. It produces a precisely defined cavity with a vacuum under a monocrystalline silicon membrane. This process is able to produce high-precision, small and cost-efficient pressure sensors together with evaluation circuits on one chip.
Significance of the Innovation
Surface micromachining has already resulted in products that give an idea of the future market opportunities: Bosch acceleration sensors measure accelerations with ultra-low power consumption and even have a wake-up function which is motion sensitive and is triggered automatically. These sensors are used in laptops to protect the hard drive from shock and vibrations or in mobile phones to allow the user to navigate the menu by tilting the device.
Mobile phones can be operated using acceleration sensors. When the phone is put down in a certain position, it automatically switches incoming calls to vibrate. Using motion-sensitive remote control devices, televisions can be controlled “with a flick of the wrist”.
Acceleration sensors in sportswear analyze an athlete’s sequences of motion to optimize training sessions.
Pressure sensors from Bosch Sensortec are used in high-precision GPS navigation systems. In large buildings, the advanced technology is accurate to within 25 centimeters, thus providing users with truly mobile navigation capabilities.
Modern middle-size class cars already incorporate some 100 high-precision, intelligent sensors to make driving safer, cleaner, more economical, and comfortable. The smaller, more robust, and cost effective sensors open up additional potential uses, particularly in regard to lowering fuel consumption and emissions as well as improving safety.
The “APSM process” paves the way for extremely thin, high-quality semiconductor chips which are in increasingly high demand in mobile electronics, such as electronic passes or RFID tags.
Micromechanics for Consumer Electronics
Most micromechanical components are found today in ink-jet printer heads and as micromirrors in video/data projectors. The Bosch Group is the world’s leading manufacturer in the specialized sector of micromechanical sensors. In 2006, Bosch turned over several hundred million dollars with micromechanical sensors for the automotive industry. More than 200 million units are now produced annually.
The market for consumer electronics applications is opening up with high growth rates thanks to the new processes of surface micromachining. Over the next five years, according to market forecasts, sales of micromechanical sensors are expected to double. The automotive sector will continue to be an important pillar of the company’s success. Bosch currently employs 2,000 for automotive applications alone. Linked to the growth in sensors, there is also an increased demand for the necessary integrated evaluation circuits. This is one of the reasons Bosch is building a new semiconductor fabrication factory in Reutlingen. It is the company’s largest single investment with 600 million Euros. It will create 800 new jobs.
With the founding of Bosch Sensortec GmbH (http://www.bosch-sensortec.com) in 2005 Bosch brings their experience in micromechanical sensors to new markets outside of the automotive sector. This in turn creates additional new jobs. Bosch Sensortec employs more than 50 people worldwide. Further growth is foreseeable in this runaway market.
The right to nominate outstanding achievements for the German Future Award is incumbent on leading German institutions in Science and Industry as well as foundations.
The Project “Smart Sensors Take Over Consumer Electronics, Industry, and Medicine” was nominated by the Federation of German Industries (BDI).
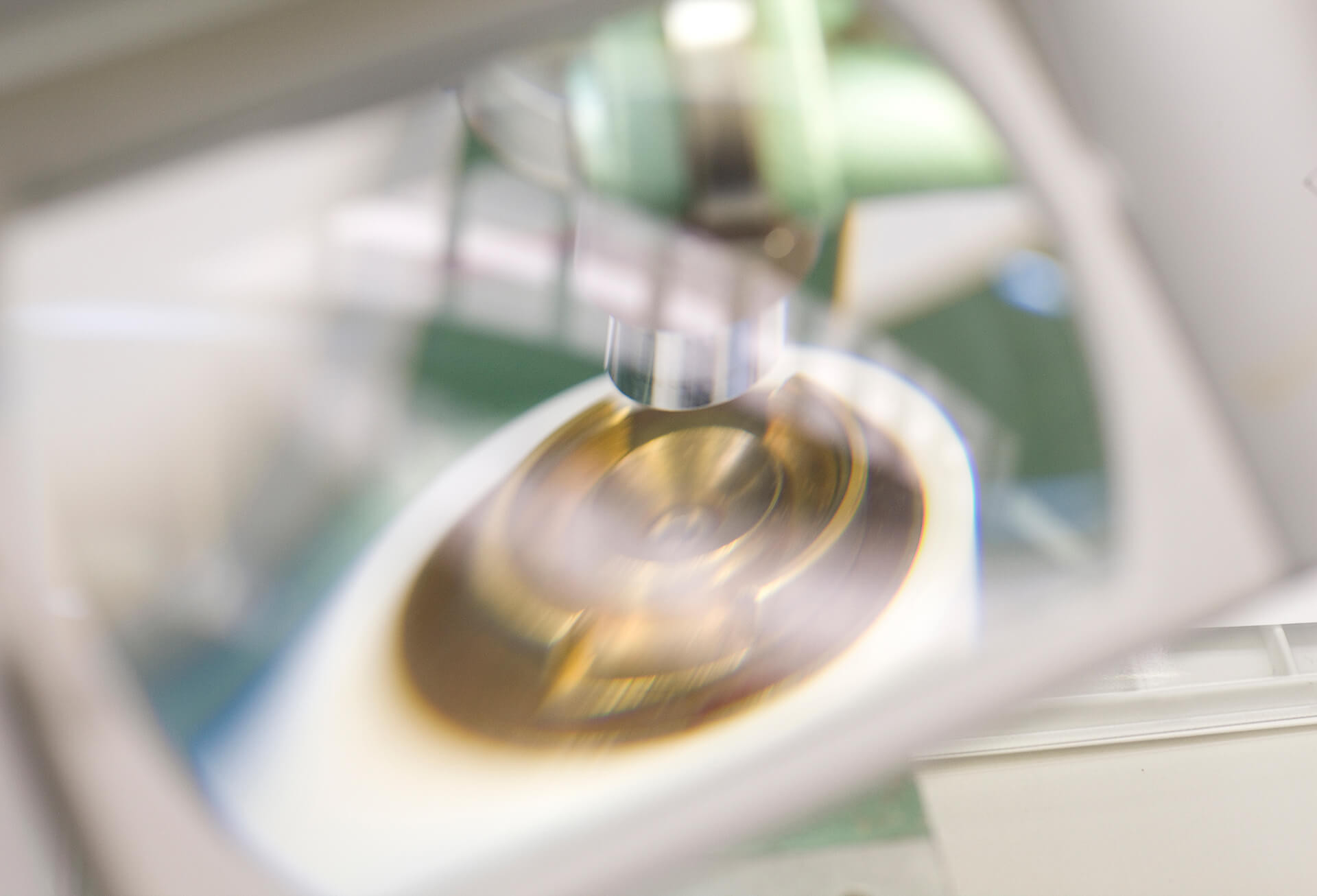