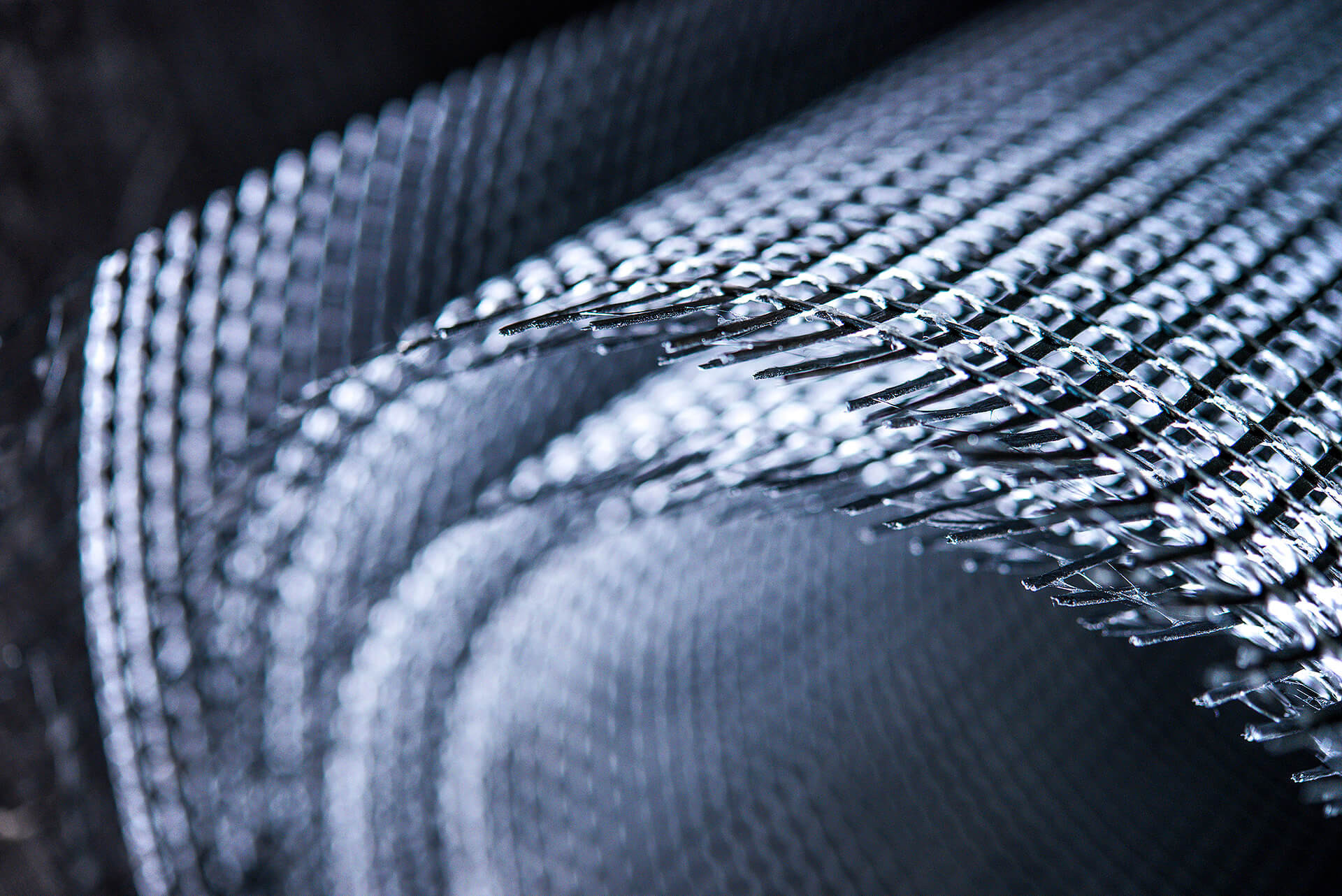
Winner 2016
Faszinierendes Material Carbonbeton

Prof. Manfred Curbach, Prof. Chokri Cherif and Prof. Peter Offermann were significantly involved in the development of one of these alternatives. They elaborated an innovative concrete-composite material that is considerably more durable than steel reinforced concrete and gives architects new design options. Instead of an iron core that is subject to corrosion, this concrete contains carbon: a fabric made of fine carbon fibres. Carbon concrete is durable, environmentally friendly and versatile in its uses. The three nominees conduct research at the Technische Universität Dresden: Manfred Curbach is head of the Institute for Solid Building Construction, Peter Offermann is Professor Emeritus at the Institute for Textile Machines and Textile High Performance Materials Science that is currently chaired by Chokri Cherif.

Reinforced concrete (RC) has been the material most frequently used in residential and industrial buildings, factories, bridges, tunnels, towers and concrete masts since the 1950's. As rebar, ribbed steel rods are placed in concrete to improve stability since it combines the compressive strength of concrete with the tensile strength of steel. Yet it has its disadvantages as well. RC manufacture uses a lot of energy and accounts for a high percentage of the construction industry's CO2 emissions. Reinforced concrete structures are also an increasing safety risk: since steel is threatened by corrosion, structures have a limited life span of around 40 to 80 years. This is one of the reasons why many of the 120,000 bridges in Germany will need maintenance work in the next few years. This goes hand-in-hand with costs totalling billions of Euros. Replacing steel-reinforced concrete with carbon concrete can largely avoid expensive repairs and also lower the use of resources.
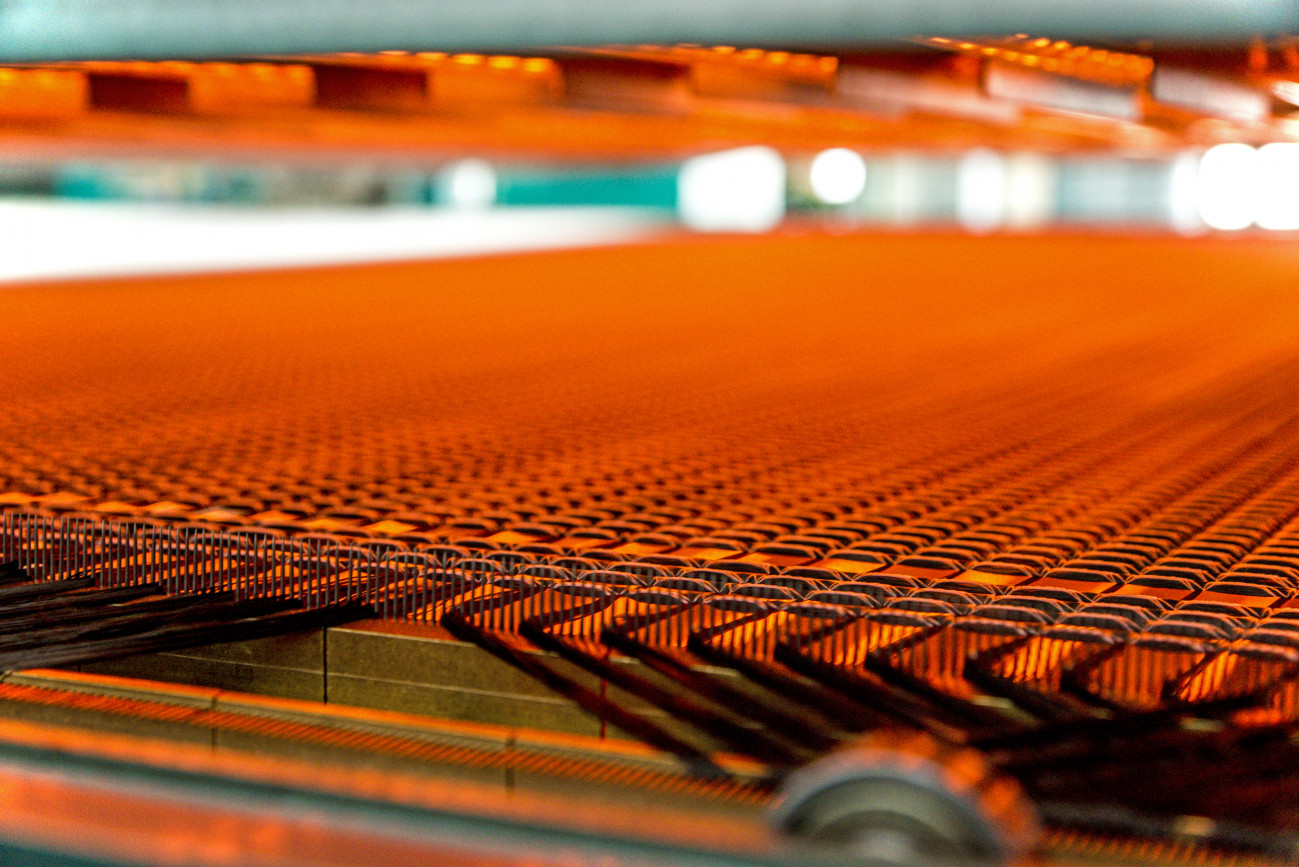
Inhalt konnte nicht geladen werden
Bitte ändern Sie ihre Privatsphäreneinstellung und aktivieren sie die Kategorie "Externe Inhalte"
Jetzt ändernDeutscher Zukunftspreis 2016 Erklärfilm ZDF Team 1
more details
Resumes
Prof. Dr.-Ing. Manfred Curbach
- 28.09.1956
- Born in Dortmund
- 1963 – 1967
- Dietrich-Bonhoeffer-Elementary School in Dortmund
- 1967 – 1976
- Einstein-Grammar School in Dortmund
- 1976 – 1977
- Military service 3./FlaRakBtl 26 in Wiesmoor
- 1977 – 1982
- University of Dortmund, study of Civil Engineering, Structural engineering
- 1980
- Admission to the German Academic Scholarship Foundation of the Federal Republic of Germany
- 1982
- Study abroad at Princeton University, New Jersey, USA, Prof. Billington, with the main emphasis on “Bridge construction in the USA” and “Maillart”, as scholarship holder for the German Academic Scholarship Foundation of the Federal Republic of Germany
- 1982 – 1983
- Research associate at the University of Dortmund, Chair for Concrete and steel reinforced concrete construction, Prof. Eibl
- 1984 – 1988
- Research associate at the University of Karlsruhe, Institute for Concrete Structures and Material Technology, Prof. Eibl
- 1987
- Doctorate in Civil Engineering, University of Karlsruhe, Degree: Dr.-Ing. (magna cum laude)
- 1988 – 1994
- Project manager with Köhler + Seitz Engineers, Nürnberg / Dresden / München
- 1994
- Lectures on Concrete Structures at the Technische Universität Dresden (TU Dresden)
- 1994 – 2004
- Partner at Köhler + Seitz Engineers, Nürnberg / Dresden / München
- since 1994
- University professor (C4), Holder of the Chair for Concrete Structures at TU Dresden
- 1997
- Approval as inspection engineer for structural analysis for concrete structures
- since 1999
- Member of the scientific advisory board for the German periodical "Beton- und Stahlbetonbau"
- 1999 – 2011
- Spokesman of the Collaborative Research Centre 528 of the Deutsche Forschungsgemeinschaft DFG (German Research Association) "Textile Bewehrungen zur bautechnischen Verstärkung und Instandsetzung" (Textile reinforcements for structural strenghtening and repair)
- 2000 – 2002
- Expert for the Deutsche Forschungsgemeinschaft - DFG
- 2002 – 2008
- Member of the senate of the DFG
- 2003 – 2008
- Chairman of the Verein Deutscher Ingenieure Gesellschaft - VDI, Fachbereich Bautechnik (Association of German Engineers - Division Civil Engineering)
- 2004 – 2012
- Chairman of the immediate managing board of the Deutscher Ausschuss für Stahlbeton e. V. - DAfStb (German Committee for Structural Concrete)
- since 2005
- Partner at Curbach Bösche Ingenieurpartner, Dresden
- 2006 – 2010
- Vice-Rector for Structure and Development
- since 2010
- Head of the German delegation of the International Federation for Structural Concrete fib (fédération internationale du béton)
- since 2011
- Spokesman of the Priority Programme SPP 1542 “Leicht Bauen mit Beton“ funded by the DFG
- since 2013
- Spokesman of the consortium C³ – Carbon Concrete Composite funded by the Federal Ministry of Education and Research (BMBF)
- since 2014
- Chairman of the scientific advisory board of the Bundesanstalt für Wasserbau (BAW) (Federal Waterways Engineering and Research Institute)
Further functionings
- National delegation for the fib for Germany , until May 2008 for the previous association called European Committee for Concrete (CEB)
- Convenor of the fib Task Group 1.6 History of Concrete Structures
- Member of the research board of the DAfStb
- Member of the committee "Design and Construction" of the DIN e.V.
- Member of the research board of the University of Kaiserslautern
- Convenor of the expert‘s committee „Bearing surface insulation of LAU-systems (storage, filling and handling)“ of the Deutsches Institut für Bautechnik - DIBt (Centre of Competence for Construction)
- Member of ACI, ASCE, DAfStb, IngKammer, PCI, RILEM, VDI, VPI
Research emphasis
- Carbon reinforced concrete
- Material behaviour of concrete under high loading rates
- Behaviour of concrete components under impact
- Multiaxial concrete strength
- Composite behaviour of high-performance concrete and reinforcement steel under fatigue load
- Reinforcement and repair of old concrete constructions
- Bridge construction
Honors
- 2003
- Innovation Award of the TechTextil
- 2006
- Award for Outstanding Concrete Structures of the fib – fédération internationale du béton
- 2011
- Honorary doctorate of the University of Kaiserslautern
- 2012
- Winner of the German Bridge Construction Prize in the category Road and Rail Bridges
- 2013
- Admission to the German National Academy of Sciences Leopoldina
- 2014
- Conferment of the Wolfgang-Zerna medal of honour by the VDI – Division Civil Engineering and Building Services
- 2014
- GreenTec-Award
- 2015
- National German Sustainability Award by the BMBF, category Research
- 2015
- Deutscher Rohstoffeffizienz-Preis by the Federal Ministry of Economic Affairs and Energy (BMWi)
- 2016
- Election as full member to the Technikwissenschaftlichen Klasse (Class of Engineering Sciences) of the Sächsische Akademie der Wissenschaften zu Leipzig (Saxon Academy of Sciences in Leipzig)
- 2016
- Conferment of the George Sarton medal of honour of the History of Science Society, University of Gent
Prof. Dr.-Ing. habil. Dipl.-Wirt. Ing. Chokri Cherif
- 24.05.1966
- Born in Bourouis, Tunisia
- 1986 – 1992
- RWTH Aachen University, study of Mechanical Engineering, Textile Technology
- 1992 – 1993
- Research Associate at RWTH Aachen University, Institute of General Mechanics
- 1992 – 1995
- RWTH Aachen University, study of Business and Economics
- 1993 – 2001
- Research Associate at RWTH Aachen University, Institute of Textile Technology
- 2001 – 2005
- Associate professor at RTWH Aachen University, Faculty of Mechanical Engineering, VENIA LEGENDI for Textile Production Technology
- 2002 – 2003
- Coordinator technology and Head of technology development at Rieter Ingolstadt Spinnereimaschinenbau AG
- 2004 – 2005
- Department Manager development and instruction, member of the management, Business Unit at Rieter Ingolstadt Spinnereimaschinenbau AG
- since 2005
- Director of the Institute of Textile Machinery and High Performance Material Technnology (ITM) at the University of Dresden
- since 2009
- Managing director of the TUDATEX GmbH
Further functionings (abridged version)
- since 2007
- Main organizer (in collaboration with the DWI and RWTH Aachen University as well as the Institut für Textil- und Verfahrenstechnik (ITV) Denkendorf) (Institute of Textile and Process Technology)) of the Aachen-Dresden-Denkendorf International Textile Conference (>700 participants)
- since 2008
- Mentor for the founding of new businesses
- since 2009
- Member of the faculty board and the Strukturkommission of the Faculty of Mechanical Engineering at the University of Dresden
- since 2009
- Review Board of the Deutsche Forschungsgemeinschaft - DFG ( German Research Association), division „Lightweight Construction, Textile Technology“
- 2010 – 2013
- Chairman AUTEX – International Association of Universities for Textiles
- 2013 – 2015
- Vice-chairman AUTEX - International Association of Universities for Textiles
- since 2014
- Founding member C³ - Carbon Concrete Composites e. V.
- since 2015
- Member of the university council at Hof University
- since 2015
- Member of the academic council of the Arbeitsgemeinschaft industrieller Forschungsvereinigungen „Otto von Guericke“ e.V. – AiF (German Federation of Industrial Research Associations) / Chairman expert’s group 5
- since 2016
- Founding member of the „Research Center Carbon Fibers Saxony (RCCF)”
Publications and patents
- 1.500 national and international publications in periodicals as well as written lectures in reference books and research journals
- 230 national und international patents
- 5 reference books
Honours
- Since 2005 more than 60 prizes have been awarded to outstanding student research projects, dissertations and scientific projects which have been supervised by the ITM:
- 2010
- „Théophile Legrand International Award for Textile Innovation” 2010(in Roubaix/FR and 2016 in Paris/FR
- 2011
- Paul Schlack Award 2011
- 2013
- Max-Kehren-medal of honour 2013
- 2014
- AVK-Innovation-Award Research/Science 2014
- 2014
- mtex-Innovation-Award 2014
- 2014
- Paul Schlack Award 2014
- 2015
- Otto von Guericke-Award 2015
- 2015
- JEC Innovation Award Europe 2015
Prof. Dr.-Ing. habil. Peter Offermann
- 13.07.1940
- Born in Görlitz
- 1958
- Grammar school in Zittau
- 1958 – 1964
- Mechanical Engineering, College of Technology Dresden and Technische Universität Dresden respectively, textile technology
- 1964 – 1968
- Research associate at the Technische Universität Dresden (TU Dresden), Institute of Textile Technology
- 1968
- Doctorate: Mechanical Engineering in 1968, TU Dresden, Degree: Dr.-Ing. (magna cum laude)
- 1975
- Habilitation: Mechanical Engineering, TU Dresden
- 1968 – 1969
- Head of the main research and development center at VEB Tüllgardinen- und Spitzenwerke Dresden
- 1969 – 1974
- Vice director for research and development at VEB Textilkombinat Cottbus
- 1970
- Appointment to honorary lecturer für textile technology at TU Dresden
- 1974
- Appointment to assistant professor for textile technology at TU Dresden
- 1977 – 1990
- Vice research division manager of the division Textile and Ready-Made Technology, TU Dresden
- 1984
- Appointment to university professor
- 1990 – 1997
- Vice-Rector for structure and development of the TU Dresden, 1st deputy of the Rector
- 1990 – 2005
- Director of the Institute of Textile and Ready-Made Technology at TU Dresden (now known as Institute of Textile Machinery and High Performance Material Technology)
- 1991 – 1998
- Member of the committee "Planning, capacity and organizational issues” of the Hochschulrektorenkonferenz (Conference of University Rectors) of Germany
- 1997 – 2003
- Member of the faculty board of the Faculty of Mechanical Engineering and Science of the TU Dresden
- 2000 – 2005
- Reviewer for the Deutsche Forschungsgemeinschaft – DFG (German Research Foundation)
- since 2005
- Scientific adviser and adviser for the transfer of technology, in particular for the Collaborative Research Centre 528 of the DFG
- since 2005
- Retirement
- 2000 – 2009
- Chairman of the TUDAG, Technische Universität Dresden AG
- since 2007
- Scientific adviser for the Deutsches Zentrum Textilbeton – DZT (German Center for Textile-Reinforced Concrete) at the TUDAG
- since 2009
- Organisator of the Anwendertagung Textilbeton
- since 2009
- Initiator and chairman of the board of management of the association and quality label TUDALIT e. V.
Further functionings (abridged version)
- Expert for the academic council for the Arbeitsgemeinschaft industrieller Forschungsvereinigungen „Otto von Guericke“ e.V. – AiF (German Federation of Industrial Research Associations) Full member of the Saxon Academy of Sciences in Leipzig Member of the National Academy of Science and Engineering acatech Member of the university council at Hof University from 1995 to 2015 Committee member of several well-known international textile conferences Member of the Sächsisches Textilforschungsinstitut Chemnitz e. V., (Saxon Textile Research Institute Chemnitz), Technical University of Chemnitz (TU Chemnitz) Member of the Int. Federation of Knitting Technology (IFKT) Honory Citizen of Buda Tech, Technical University of Budapest Scientific advisory board for the journal Melliand-Textilberichte (Melliand-textile reports), Melliand-International and Melliand-China
Honors
- Between 1990 and 2005 more than 20 prizes have been awarded to outstanding student research projects, dissertations and scientific projects which have been supervised by the ITB (later known as ITM):
- 2000
- Honoray doctorate of the State University for Technology, St. Petersburg, Russia
- 2001
- Techtextil-Innovation Award
- 2003
- Techtextil-Innovation Award
- 2004
- Creativity Award of the Walter Reiners-Stiftung des Deutschen Textilmaschinenbaus for dissertations
- 2004
- Creativity Award of the Walter Reiners-Stiftung des Deutschen Textilmaschinenbaus for Projects works and master theses
- 2005
- Cetex-Sponsorship Award
- 2006
- Honorary doctorate of the Technical University of Lodz, Poland
- 2013
- AUTEX-Award 2013 (Association of Universities for Textiles)
Contact
Team-Sprecher
Prof. Dr.-Ing. Manfred Curbach
Institut für Massivbau
Technische Universität Dresden
01062 Dresden
Phone: + 49 (0) 351 / 46 33 76 60
E-Mail: manfred.curbach@tu-dresden.de
Pressekontakt
Sandra Kranich
Institut für Massivbau
Fakultät Bauingenieurwesen
Technische Universität Dresden
01062 Dresden
Phone: +49 (0) 351 / 48 45 67 17
Fax: +49 (0) 351 / 48 45 67 10
Mobile: +49 (0) 162 / 43 63 855
E-Mail: Sandra.Kranich@tu-dresden.de
www.massivbau.tu-dresden.de
C3 - Carbon Concrete Composite e.V.
World Trade Center Dresden
Ammonstraße 72
01067 Dresden
E-Mail: post@bauen-neu-denken.de
www.bauen-neu-denken.de
Status 2016
A description provided by the institutes and companies regarding their nominated projects
Concrete gives shape to the world we live in. The steel bars embedded in the concrete up to now reinforce the material and give it stability. Steel reinforced concrete is resource intensive, environmentally stressing, heavy and, moreover, susceptible to corrosion. In fact, we are faced with the consequences of corrosion damage, including deteriorated bridges and roads, every day. The thought of not being stuck in traffic jams anymore seems tempting, but unrealistic. However, if Manfred Curbach, Chokri Cherif and Peter Offermann had their way, all of the above could be changed soon. The three scientists hope to be able to replace approximately 20% of steel reinforced concrete with carbon concrete in the near future. But what exactly is carbon concrete, and what makes it so special? The innovative material is a composite made of high-performance concrete and carbon reinforcement. The revolution is in the carbon fibre, which produce a light, flexible and durable material. Each yarn is composed of up to fifty thousand of these extremely fine carbon fibres. A textile machine then processes the yarns into a fabric covered with a stabilising coating. Moreover, for an optimal load-efficiency in the concrete the fibres can be arranged according to the stress distribution. The result is a corrosion-resistant and resource-efficient alternative to steel reinforced concrete.
The Dresden scientists have been working on this fascinating material since the 1990s. The fundamental knowledge about carbon concrete is based on research about textile reinforced concrete, carried out between 1999 and 2011 in two collaborative research centres of the Deutsche Forschungsgemeinschaft DFG in Dresden and Aachen. The scientific knowledge gained by this research was gradually put into practice. The founding of the organisations Deutsches Zentrum Textilbeton, Tudalit e.V., TUDATEX GmbH and CarboCon GmbH is yet another result of their hard work. Along the process chain – from the basic material to the finished building component – the practical implementation process already began and is being continued since 2014 by the largest German construction research project "C³ - Carbon Concrete Composite". This project, financed by the Federal Ministry of Education and Research, is managed by Professor Manfred Curbach and, under the lead management of the Technische Universität Dresden, is making significant advances in the research of carbon concrete. More than 140 companies are currently working together in order to successfully bring the material on the market.
Carbon concrete is light, corrosion-resistant and flexible. Therefore, any field in need of resource and energy efficient, durable, space-saving and multifunctional construction methods is a potential market.
Carbon concrete can be utilised in two areas: structure maintenance (tunnels, bridges, residential and industrial buildings, concrete masts) and new constructions; in short, in all fields, where the main focus lies on reducing the mass of construction components, and hence the structure's dead load. For façade panels or balcony floor boards for instance, the costs for material, transport and fitting, as well as the substructure, fastening and support structure, can be drastically reduced. Due to lightweight building components the level of factory prefabrication can be increased, resulting in lower costs and higher quality.
Numerous strengthened buildings and new constructions demonstrate the practicality and high resource-efficiency of carbon concrete in an impressive and convincing manner.
Economical: Carbon concrete reduces costs and saves material
Building with carbon reinforced concrete creates new values. New structures with a significantly extended utilisation period are proof of this. At the same time, carbon concrete sustains existing values by the chance of reinforcing old buildings with very thin layers of concrete, enabling their continued use for a prolonged period of time. Carbon concrete not only saves valuable resources, but also allows us to reduce the total cost of construction. During the tender process for the strengthening of the historical railway bridge in Naila at the beginning of 2016, carbon concrete was chosen over steel reinforced concrete because it was 10% cheaper. Moreover, using carbon concrete for the structural retrofitting saved approximately 80% of the material.
The important thing is that as far as the technical efficiency is concerned, carbon and steel are equal in terms of price, although the kilogramme-prices may give a different impression. 1 kilogramme of steel costs appr. 1 euro, whereas a kilogramme of carbon costs appr.16 euros, respectively. However, the density of carbon is four times lower than that of steel, and its strength is six times as high. Consequently, for 16 times the price you get 24 times the technical efficiency.
For instance, façade panels or reinforcement layers made of carbon concrete are approximately only two centimetres thick, whereas if made of steel reinforced concrete, they would be eight centimetres thick. As such, the amount of material that has to be manufactured, transported, built in and fixed is reduced by 75%. Moreover, the significantly longer period of use plays an important role: whilst structures made of steel reinforced concrete have to be retrofitted every 40 to 80 years due to corrosion damage, carbon concrete is considered to have a service life of up to 200 years or more.
Efficient: Using carbon concrete reduces CO2 emissions and saves valuable resources
The building industry is one of the most important branches of the German economy. Its level of innovation will have a significant influence on whether Germany succeeds in fulfilling its climate goals - the reduction of CO2 emissions, energy saving and resource conservation. With the exception of water, concrete is the most-used raw material, with approximately 5 billion m³. Concrete is composed of cement, sand, gravel and water. 1.6 billion tonnes of cement, 10 billion tonnes of sand and gravel aggregate, and one billion tonnes of water are used in the development and retrofitting of buildings and bridges every year. Thereby, every tonne of cement generates over half a million tonnes of CO2. The immense amount of material required causes the building industry to be one of the largest emitters of CO2 and responsible for around 40% of energy consumption.
Carbon is a fundamental element of life on earth, and can be extracted from plants, rocks, and even air. Crude oil is currently used to produce carbon, as it is relatively inexpensive and, compared to the required amount, its availability is practically unlimited. However, current research is looking at the possibility of producing carbon from lignins, a product of wood residues left over when manufacturing paper. This method could be put into industrial use within 5 years.
Switching to carbon concrete for the construction and retrofitting of buildings reduces energy consumption and CO2 emissions by 50% and saves valuable resources. Using carbon concrete means we can build with thinner walls, which requires less cement, sand, gravel and water, and furthermore reduces transport costs.
Attractive: Carbon concrete creates an entirely new design language
A durable and resource-efficient composite material, carbon concrete combines strength with flexibility and multi-functionality, making construction maintenance and future construction economical, ecologically sustainable and attractive. "Lightweight building" and "concrete" is no longer a contradiction. The relatively small thickness of the building components allows for a finer and more appealing building style. Thus, it is possible to gain more interior space whilst maintaining the size of the exterior. The flexible but extremely highstrength carbon fabric is easy to process and, due to its enhanced durability, is a suitable as reinforcing material.
Carbon concrete causes a paradigm shift in architecture as well as construction, and is about to create an entirely new design language. In future carbon concrete technology is likely to meet changing user requirements and to adjust to new multifunctional features. Furthermore, carbon concrete creates new opportunities for building retrofitting and strengthening. The innovative building material allows for extremely thin but highly efficient strengthening layers in concrete constructions and is particularly suited to complex boundary conditions and the preservation of historical buildings.
TU Dresden / Institute for Concrete Construction & Institute for Textile Machinery and High Performance Material Technology
With 36,000 students, the Technische Universität Dresden is one of the leading universities in Germany and Europe; strong in the field of research, first-class in diversity and the quality of educational programmes, and closely linked to culture, commerce and society.
Concrete construction has been taught as part of the TU Dresden programme for more than 100 years. The institute includes two professorships. The academic focus in teaching and research lies on all aspects of reinforced concrete in experiments and simulations. Several commercial and industrial partners add to the programme and work together to transfer the results of research to real construction projects.
The research activity of the Institute for Textile Machinery and High Performance Material Technology includes the processing of fibre-based high tech materials with various processing technologies, as well as the functionally integrated development of semi-finished textiles and textile products. In addition, the research activity includes the modelling and simulation of structures and processes at every stage of the textile chain.
The interdisciplinary project “C³ - Carbon Concrete Composite” is one of ten projects funded by the Federal Ministry of Education and Research programme "Twenty20 - Partnership for Innovation" as part of the initiative "Entrepreneurial Regions". The project is managed by the Technische Universität Dresden. The C³ project is working with over 140 partners from research in addition to various companies and associations to develop a new composite material made of carbon fibres and high performance concrete. Thanks to its flexibility and durability, carbon concrete is a resource-efficient alternative to steel reinforced concrete and saves material as well as creating many new design opportunities, characterised by lightness and malleability.
The right to nominate outstanding achievements for the Deutscher Zukunftspreis is incumbent on leading German institutions in science and industry as well as foundations.
The project "Carbon concrete, a fascinating material - economical, efficient, attractive” was nominated by the Leopoldina - the German National Academy of Sciences.
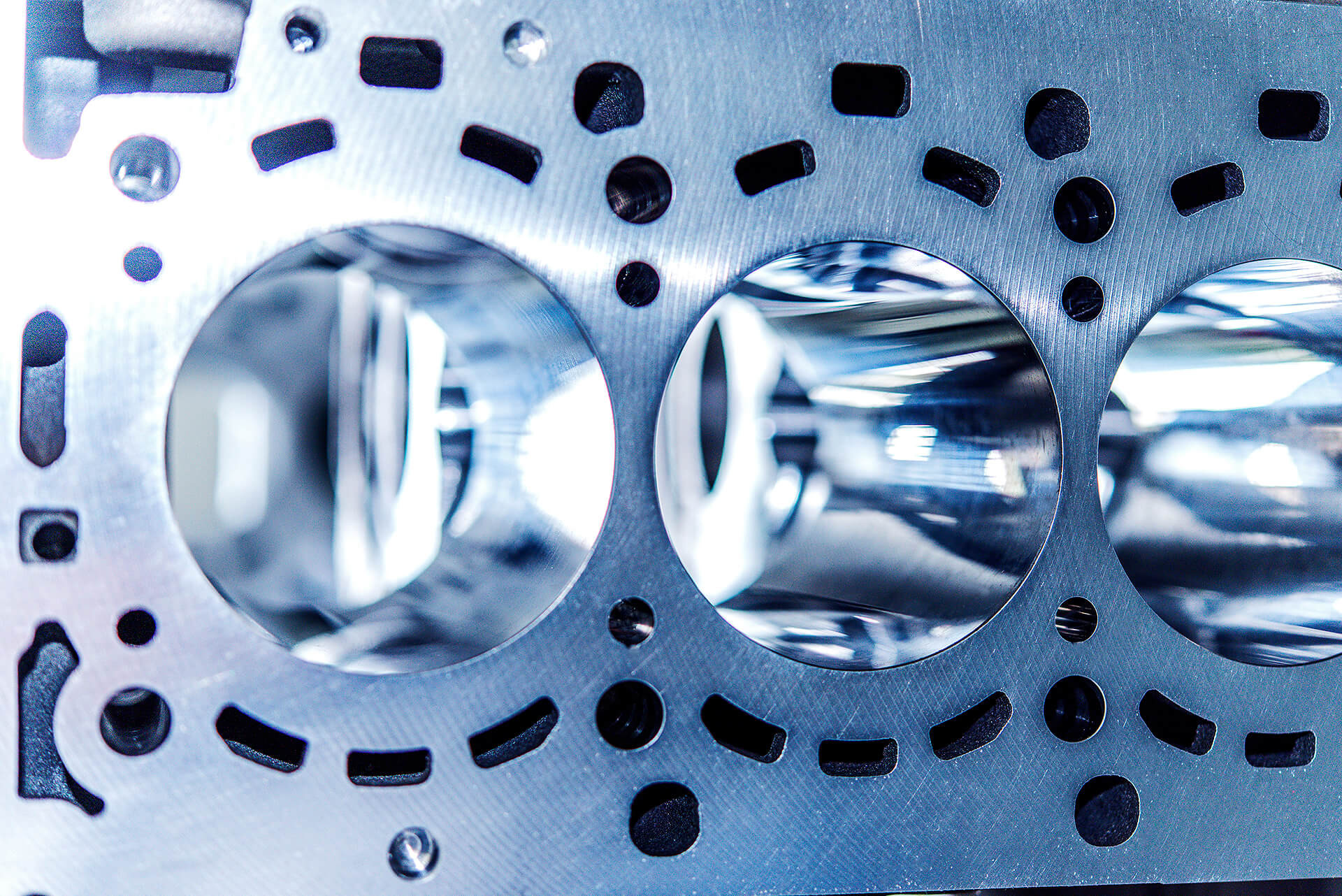