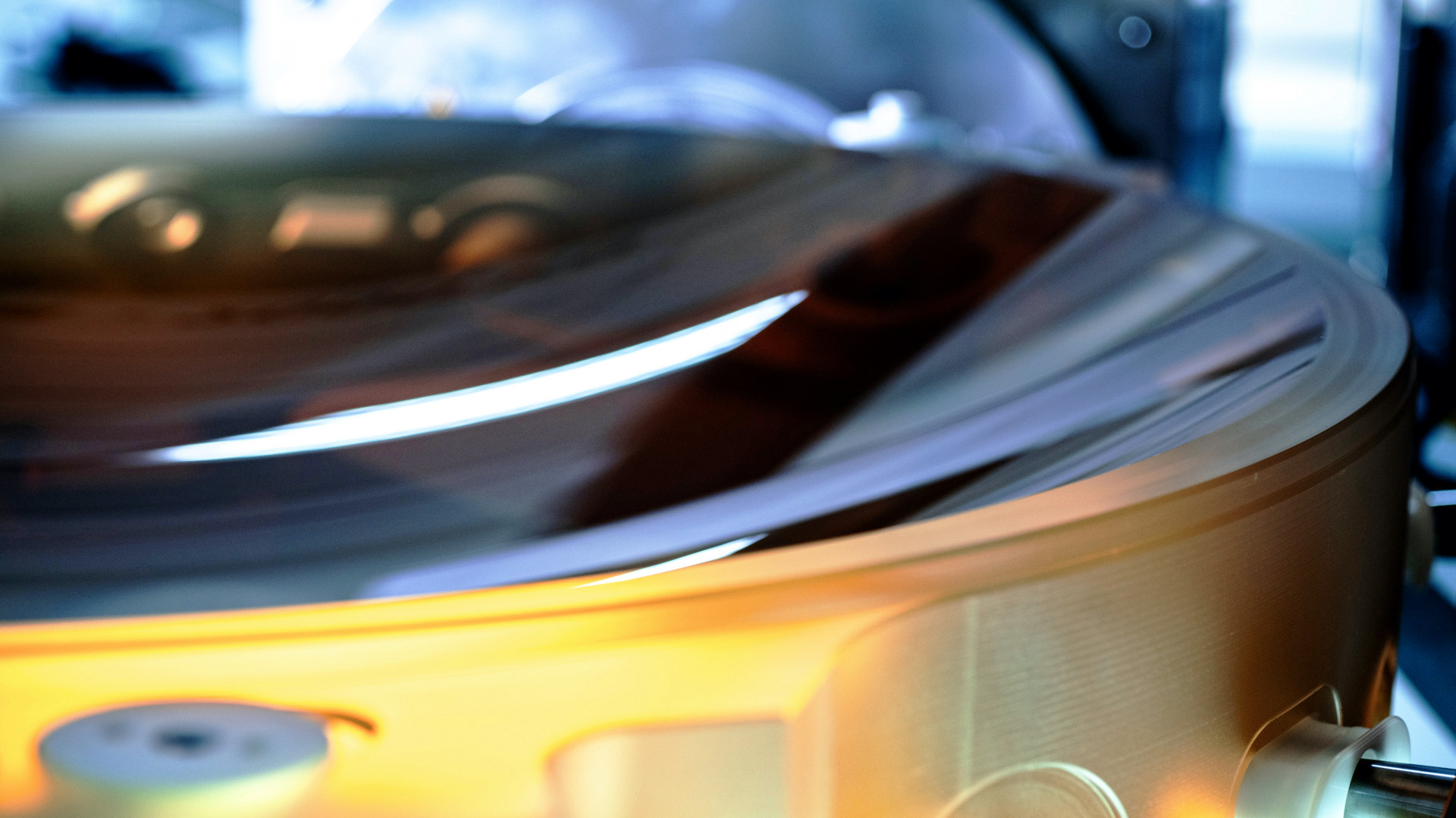
Preisträger 2020
EUV-Lithographie
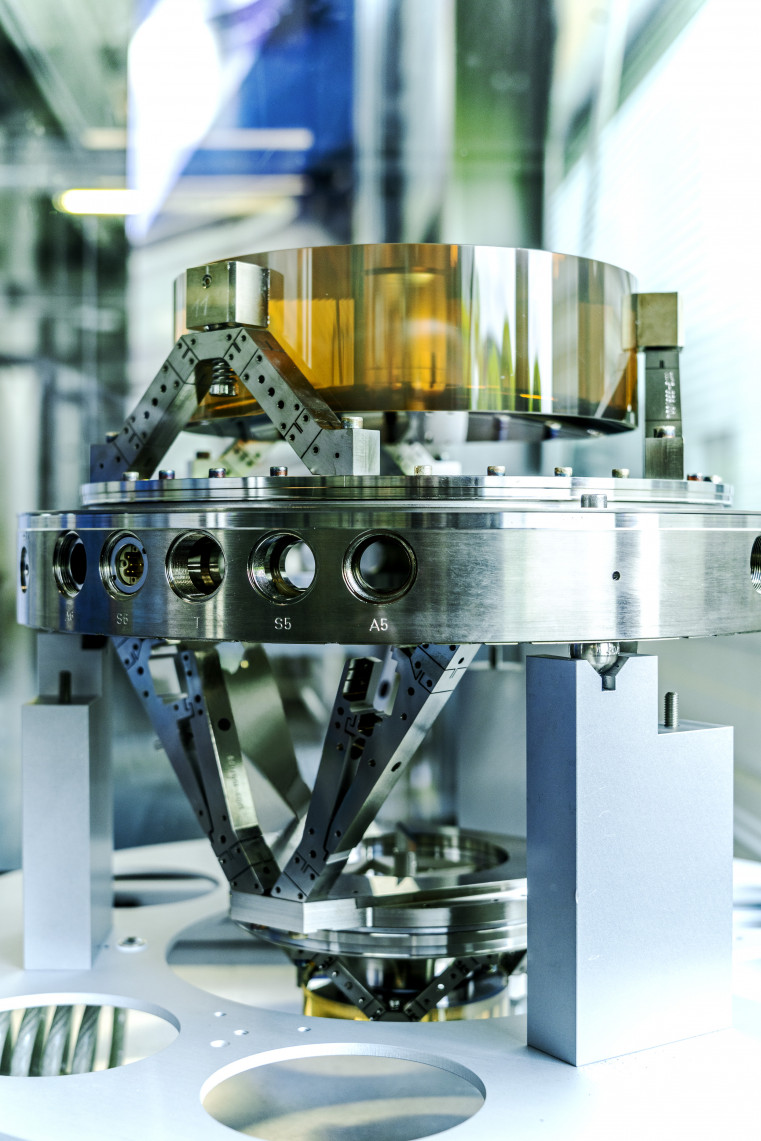
Dr. rer. nat. Peter Kürz, Dr. rer. nat. Michael Kösters und Dr. rer. nat. Sergiy Yulin haben einen wesentlichen Beitrag zur Entwicklung und Industrialisierung einer Technologie geleistet, mit der sich mikroelektronische Bauteile mit extrem feinen Strukturen fertigen lassen – die Voraussetzung für viele neue Anwendungen und einen kräftigen Schub bei der Leistungsfähigkeit der Informationstechnik (IT). Dazu setzten die drei Forscher zusammen mit über 2000 Entwicklungskollegen in ihren Unternehmen und in Zusammenarbeit mit ASML auf die in der Chipfertigung seit Jahrzehnten etablierte Methode der optischen Lithographie und machten diese fit für die Nutzung von Licht im extremen Ultraviolett (EUV).

Gegenüber der bisher etablierten Lithographie lassen sich mit der EUV-Lithographie wesentlich kleinere Strukturen erzeugen, in der Größenordnung von wenigen Nanometern (millionstel Millimetern) – das entspricht etwa einem Zehntausendstel der Dicke eines menschlichen Haars. Dazu musste das nominierte Team die Grenzen des technisch Machbaren drastisch verschieben – was den Forschern unter anderem durch ein neuartiges optisches System und eine Lasertechnik der Extraklasse gelang.
"Für diese Hochleistungsoptik haben wir die weltweit präzisesten Spiegel entwickelt. Zum Vergleich: Wenn man einen dieser Spiegel auf die Fläche von Deutschland aufblasen würde, dann wären die größten Abweichungen von der Sollform gerade mal 0,1 Millimeter groß."
Dr. rer. nat. Peter Kürz
Weitere Details
Lebensläufe
Dr. rer. nat. Peter Kürz
- 01.05.1965
- Geboren in Bad Säckingen
- 1984
- Abitur am Klettgau-Gymnasium Tiengen
- 1985 - 1990
- Studium der Physik an der Ludwig-Maximilians-Universität München, Abschluss: Diplom
- 1990 - 1994
- Wissenschaftlicher Mitarbeiter an der Universität Konstanz
- 1990 - 1994
- Promotion am Lehrstuhl von Prof. J. Mlynek, Universität Konstanz
- 1994
- Forschungsaufenthalt an der Ecole Normale Supérieure, Paris, Frankreich
- 1994 - 1996
- Wissenschaftler bei den NTT Basic Research Laboratories, Nippon Telegraph and Telephone Corporation, Atsugi-Shi, Japan
- 1996 - 1997
- Wissenschaftlicher Mitarbeiter in der zentralen Forschungsabteilung bei ZEISS, Oberkochen
- 1998 - 1999
- Produktverantwortlicher im ZEISS Unternehmensbereich Halbleitertechnik, Oberkochen:
verantwortlich für die Entwicklung des ersten 193 nm Objektivs - 1999 - 2015
- Leiter EUV Programm im ZEISS Unternehmensbereich Halbleitertechnik, ab 2001 bei der ZEISS Sparte Semiconductor Manufacturing Technology (SMT), Oberkochen:
verantwortlich für Entwicklung & Produkteinführung von EUV Micro Exposure Tool, Alpha Demo Tool, Starlith® 3100 (EUV Pre-production Tool), Starlith® 3300 (erste serientaugliche EUV-Optik), Starlith® 3350 - 2015 - 2017
- Product Line Manager EUV Systems bei der ZEISS Sparte SMT Oberkochen: verantwortlich für Entwicklung & Produkteinführung des Starlith® 3400 (erstes EUV-Serientool)
- seit 2017
- Vice President Field of Business EUV High-NA bei der ZEISS Sparte SMT Oberkochen:
verantwortlich für Entwicklung & Produkteinführung der nächsten Generation von EUV-Optiken
Ehrungen und Auszeichnungen
- 2006
- Carl Zeiss Innovationspreis für Leading Edge Technology für die Entwicklung des optischen Systems für das EUV Alpha Demo Tool
- 2007
- Als Teamsprecher nominiert für den Deutschen Zukunftspreis: „Revolutionäre Optik für den Computerchip der Zukunft“
- 2013
- Carl Zeiss Innovationspreis für Leading Edge Technology für die Entwicklung der ersten serientauglichen EUV Optik (Starlith® 3300)
Dr. rer. nat. Michael Kösters
- 18.06.1980
- Geboren in Bad Hönningen, Deutschland
- 2000 - 2006
- Studium der Physik, Rheinische Friedrich-Wilhelms-Universität Bonn, Abschluss: Diplom
- 2003 - 2004
- Auslandsstudium in Electrical Engineering, California Institute of Technology, Pasadena, USA
- 2005 - 2010
- Wissenschaftlicher Mitarbeiter, Physikalisches Institut, Rheinische Friedrich-Wilhelms-Universität Bonn
- 2006 - 2010
- Promotion am Lehrstuhl von Prof. Dr. Karsten Buse (angewandte Optik), Physikalisches Institut, Rheinische Friedrich-Wilhelms-Universität Bonn
- 2010 - 2014
- Projektleiter bei TRUMPF Laser- und Systemtechnik GmbH, Ditzingen:
Entwicklung eines gepulsten Hochleistungs-CO2-Lasers im Rahmen des BMBF-Projekts InProLight (Integrative Prozesskette zur ressourcenschonenden Serienfertigung von Leichtbauteilen aus thermoplastischen Faserverbundkunststoffen für die Fahrzeugindustrie) - 2010 - 2015
- Projektleiter für Seed Module / EUV bei TRUMPF Laser- und Systemtechnik GmbH, Ditzingen
- 2014
- Interims-Serviceleiter bei TRUMPF Laser- und Systemtechnik GmbH, ASML/Veldhoven, Niederlande
- seit 2015
- Gruppenleiter Entwicklung für High Power Seed Module / EUV bei TRUMPF Lasersystems for Semiconductor GmbH, Ditzingen
Stipendien
- 2003 - 2004
- Stipendium des Deutschen Akademischen Austauschdienstes (DAAD)
- 2006 - 2009
- Promotionsstipendium der Bonn-Cologne Graduate School for Physics and Astronomy
Dr. rer. nat. Sergiy Yulin
- 27.12.1965
- Geboren in Charkiw, Ukraine
- 1983
- Abitur an der Mittelschule No. 84 in Charkiw, Ukraine
- 1983 - 1989
- Studium der Physik an der Polytechnischen Universität Charkiw, Ukraine, Abschluss: Diplom
- 1989 - 1999
- Wissenschaftlicher Mitarbeiter, Forschungsinstitut der Metalle und Halbleiter an der Polytechnischen Universität Charkiw, Ukraine
- 1996 - 1998
- Promotion an der Karazin-Universität Charkiw, Ukraine
- 1999 - 2001
- Werkvertrag zur Zusammenarbeit in verschiedenen wissenschaftlichen Projekten, Fraunhofer-Institut für Angewandte Optik und Feinmechanik IOF, Jena
- seit 2001
- Wissenschaftlicher Mitarbeiter, Fraunhofer-Institut für Angewandte Optik und Feinmechanik IOF, Jena
- seit 2003
- Leitung von Industrieprojekten für die EUV-Lithographie, Fraunhofer-Institut für Angewandte Optik und Feinmechanik IOF, Jena
verantwortlich für neue Materialien für Optiken mit streifendem Einfall, Z-grading von EUV-Breitbandbeschichtungen und Beschichtung von EUV-Optiken, Entwicklung eines EUV-Bestrahlungsinstruments, Methoden zum Schutz und Reinigung der EUV-Lithographie-Bildgebungsoptik, Entwicklung von EUV-Hochtemperaturspiegeln und einer Beschichtung von Kollektoren von Hochleistungs-LPP-Quellen - seit 2003
- Ausbildung von Studierenden und Promovierenden, Fraunhofer-Institut für Angewandte Optik und Feinmechanik IOF, Jena
- seit 2012
- Senior Principal Scientist, Fraunhofer-Institut für Angewandte Optik und Feinmechanik IOF, Jena
Ehrungen und Auszeichnungen
- 2012
- ASML Poster Award Best Innovation: Poster „Cymer LLP collector lifetime: Strategy and improvements”
- 2007
- Thüringer Forschungspreis: „Komponenten und Systeme für die Next Generation Lithography (13,5 nm)“
Kontakt
Koordination und Pressekontakt
Frederic Franz
Communication and Implementation of Group Initiatives
ZEISS Sparte Semiconductor Manufacturing Technology
Carl Zeiss SMT GmbH
Rudolf-Eber-Straße 2
73447 Oberkochen, Deutschland
Tel.: +49 (0) 7364 / 20 62 838
Mobil: +49 (0) 151 / 18 76 89 54
E-Mail: frederic.franz@zeiss.com
Web: www.zeiss.de
Sprecher
Dr. rer. nat. Peter Kürz
Head of Field of Business High-NA EUV
ZEISS Semiconductor Manufacturing Optics
Carl Zeiss SMT GmbH
Rudolf-Eber-Straße 2
73447 Oberkochen, Germany
Tel.: +49 (0) 7364 / 20 48 95
E-Mail: peter.kuerz@zeiss.com
Web: www.zeiss.de
Beschreibung der Institute und Unternehmen zu ihren nominierten Projekten
EUV-LITHOGRAPHIE
Mit extrem ultraviolettem Licht in die digitale Zukunft
Ohne Rechenleistung keine Digitalisierung: Heute hat allein ein Smartphone die millionenfache Rechenpower des Computers, der 1969 die erste Mondlandung begleitete. Ermöglicht wird dies durch einen kaum fingernagelgroßen Mikrochip, auf dem sich mehr als zehn Milliarden Transistoren befinden. Neue Technologien und Anwendungsbereiche wie Künstliche Intelligenz, autonomes Fahren, 5G, Smart Home oder Industrie 4.0 benötigen nochmals deutlich leistungsfähigere Mikrochips. Um diese Chips der Superlative herzustellen, müssen mehr und mehr Transistoren auf immer engerem Raum Platz finden. Vorausgesagt hat Intel-Mitbegründer Gordon Moore diesen Fortschritt bei der Miniaturisierung von elektronischen Bauelementen schon 1965. Das „Moore’sche Gesetz“ besagt, dass sich die Anzahl der Transistoren auf einem Chip alle zwei Jahre verdoppelt. Eine Prognose, die mittlerweile zum Maßstab der Halbleiterindustrie geworden ist.
Schlüsseltechnologie für die Herstellung von Mikrochips ist seit mehr als 40 Jahren die optische Lithographie. Dabei werden die Strukturen der elektronischen Bauelemente ähnlich wie bei der Projektion eines Dias auf die Chips übertragen. Die Projektionsoptik bildet die Chip-Strukturen von einer Maske auf eine mit einem Fotolack bedeckte Siliziumscheibe (Wafer) ab. Dieser Ablauf wird mit verschiedenen Masken rund 100 Mal wiederholt, wodurch ein komplexes dreidimensionales Gebilde aus Transistoren und Leiterbahnen entsteht: ein Mikroprozessor oder Speicherchip. Dieses bewährte Verfahren stößt aber zunehmend an technische und ökonomische Grenzen. Um die für die fortschreitende Digitalisierung der Welt benötigte Rechenleistung zu erreichen und gleichzeitig den Energieverbrauch und die Fertigungskosten pro Chip zu senken, musste völlig neu gedacht werden.
Extrem ultraviolettes Licht ermöglicht höhere Rechenpower
Nun ist der Durchbruch gelungen. Nach über 20 Jahren intensiver, partnerschaftlicher Entwicklungsarbeit haben europäische Unternehmen und Forschungseinrichtungen eine revolutionäre neue Fertigungstechnik für leistungsfähige Mikrochips zur Serienreife gebracht: die EUV-Lithographie. EUV steht für „extrem ultraviolett“, also Licht mit extrem kurzer Wellenlänge. Mit diesem „neuen Licht“ lassen sich weitaus leistungsfähigere, energieeffizientere und kostengünstigere Mikrochips herstellen als jemals zuvor. Seit 2018 produzieren Weltmarktführer wie Samsung und TSMC ihre modernsten Chips auf Basis dieses neuen Verfahrens; Smartphones mit per EUV-Lithographie hergestellten Mikrochips sind seit Herbst 2019 auf dem Massenmarkt.
Einen entscheidenden Beitrag beim Sprung vom Labor zur Marktreife haben Teams von ZEISS Semiconductor Manufacturing Technology (SMT), der Halbleitersparte von ZEISS, TRUMPF Lasersystems for Semiconductor Manufacturing und dem Fraunhofer-Institut für Angewandte Optik und Feinmechanik IOF geleistet. Stellvertretend für die an der Entwicklung Beteiligten stehen Dr. Peter Kürz, der 1999 die Leitung des EUV-Programms bei ZEISS SMT übernahm und heute für Entwicklung und Produkteinführung der nächsten Generation von EUV-Optiken verantwortlich ist, Dr. Michael Kösters, der bei TRUMPF die Entwicklung der Hochleistungslaser zur Erzeugung des EUV-Lichts mitverantwortet, und Dr. Sergiy Yulin, der für das Fraunhofer IOF als Senior Principal Scientist Forschungsprojekte für die Oberflächenvergütung von EUV-Optiken leitet.
Während das bis dato führende optische Lithographieverfahren auf Lichtquellen mit einer Wellenlänge von 193 Nanometer setzt, arbeitet das neue Fertigungsverfahren mit nur noch 13,5 Nanometern. Die Auflösung der Optik und damit die Dimensionen der Strukturen auf den Chips skalieren mit der Wellenlänge des verwendeten Lichts. Dadurch kann die EUV-Lithographie die Transistordichte um mehr als den Faktor zehn steigern. Eine enorme Leistung, denn um Licht mit 13,5 Nanometern überhaupt erst zu erzeugen und nutzbar zu machen, mussten die Grenzen des technisch Machbaren deutlich verschoben werden.
Europäische Partnerschaften sind der Schlüssel
Weltweit einziger Hersteller für EUV-Lithographie-Maschinen ist die niederländische Firma ASML, die als Integrator die Architektur des Gesamtsystems und insbesondere die EUV-Quelle entworfen hat. Schlüsselkomponenten dieser Maschinen sind der Hochleistungslaser für die EUV-Lichtquelle und das optische System. Und genau hier kommen die Halbleitersparten des Laserherstellers TRUMPF und des Optik-Spezialisten ZEISS ins Spiel.
Um für das neue Verfahren EUV-Licht zu erzeugen, haben ASML und TRUMPF eine einzigartige Lichtquelle konstruiert: In einer von ASML entwickelten Plasmaquelle werden 50.000 Zinn-Tropfen pro Sekunde in ein Hochvakuum geschossen und dabei jeweils von zwei aufeinanderfolgenden Pulsen eines Hochleistungs-CO2-Lasers von TRUMPF getroffen. Der sogenannte Vorpuls trifft die Zinntropfen, sodass diese quasi aufquellen. Der hinterhereilende Hauptpuls trifft nun den Tropfen mit voller Leistung. Dadurch wird das Zinn-Plasma gezündet, welches die EUV-Strahlung abgibt. Damit EUV-Licht erzeugt werden kann, muss das Plasma eine Temperatur von fast 220.000 Grad Celsius erreichen. Das ist fast 40 Mal heißer als die durchschnittliche Oberflächentemperatur der Sonne. Der für diesen Vorgang erforderliche TRUMPF-Laser ist mit 30 kW Leistung der stärkste Industrielaser weltweit.
Weil ultraviolettes Licht von allen Materialien – auch Luft – absorbiert wird, hat ZEISS SMT für die EUV-Lithographie-Maschine ein optisches System geschaffen, das im Hochvakuum betrieben wird und aus Spiegeln aufgebaut ist. Da die Spiegel während des Belichtungsvorgangs so stabil wie möglich in ihrer Position gehalten werden müssen, war für maximale Kippstabilität ein völlig neues mechatronisches Konzept erforderlich. Dessen Ergebnis spricht für sich: Würde ein Laserstrahl über einen dieser EUV-Spiegel umgelenkt und auf den Mond gerichtet, könnte man damit einen Tischtennisball auf der Mondoberfläche treffen.
Wesentliche Innovationen stecken außerdem in den Spiegeln. Da selbst kleinste Unregelmäßigkeiten zu Abbildungsfehlern führen, wurde für die EUV-Lithographie der weltweit „präziseste“ Spiegel entwickelt. Vergrößerte man ihn auf die Größe Deutschlands, wäre die Zugspitze ganze 0,1 Millimeter hoch. Neben diesem Maß an Genauigkeit erfordern EUV-Spiegel höchste Reflexionsfähigkeit. Das Fraunhofer IOF fungierte hier als wichtiger Forschungspartner für die Entwicklung von EUV-Multilagenbeschichtungen, sogenannten Bragg-Spiegeln. Dabei wird ein Schichtsystem aus über 100, jeweils wenige Nanometer dicken Einzelschichten mit atomarer Präzision aufgebracht. Besonders herausfordernd ist es dabei, eine möglichst hohe Reflektivität über die gesamte Spiegeloberfläche sowie eine lange Lebensdauer der Beschichtung im späteren Belichtungsprozess zu erreichen.
Die Zukunft in neuem Licht – Hochtechnologie schafft Arbeitsplätze
Die EUV-Lithographie ist eine europäische Erfolgsgeschichte in der von asiatischen und amerikanischen Firmen dominierten Halbleiterindustrie. Optik und Lichtquelle profitieren von der großen Expertise bei photonischen Technologien in Deutschland; weitere Faktoren waren das Hochtechnologie-Netzwerk aus mehr als 1.200 Zulieferern, Universitäten und Forschungsinstituten, aber auch das enorme Durchhaltevermögen der beteiligten Firmen: EUV-Quelle, Optiksystem und EUV-Lithographie-Maschine durchliefen auf dem Weg vom Prototyp bis hin zur Serienreife einen mehr als zwei Jahrzehnte langen Prozess. Begleitet wurde die Entwicklung durch deutsche und europäische Förderprojekte, wobei die Förderung durch das Bundesministerium für Bildung und Forschung hervorzuheben ist. Das Resultat ist eine durch über 2.000 Patente abgesicherte Zukunftstechnologie.
Entsprechend groß ist die wirtschaftliche Bedeutung für die Halbleiterindustrie und für die beteiligten Firmen. Startete die EUV-Entwicklung bei der ZEISS Sparte SMT 1995 mit einigen wenigen Mitarbeitenden, sind bis heute mehr als 2.000 Hochtechnologie-Arbeitsplätze entstanden. 2019 stieg der Jahresumsatz mit EUV-Optiken auf mehr als 650 Millionen Euro, und er wächst dynamisch weiter. Auch bei TRUMPF arbeiten mittlerweile mehr als 500 Mitarbeitende an der Entwicklung und Produktion des Hochleistungslasers, mit einem Umsatz von mehr als 400 Millionen Euro in diesem Geschäftsfeld.
Die Zukunftsaussichten sind glänzend: ZEISS SMT, TRUMPF und Fraunhofer arbeiten bereits an den nächsten Generationen der EUV-Optiken und Hochleistungs-CO2-Laser. Die EUV-Technologie verspricht, Halbleiterstrukturen in den kommenden Jahren auf wirtschaftliche Weise massiv weiter zu verkleinern. Damit ist sie die Basis für den weiteren technischen Fortschritt und die Digitalisierung unseres Alltags.
Über ZEISS
ZEISS ist ein weltweit führendes Technologieunternehmen der optischen und optoelektronischen Industrie. In den vier Sparten Semiconductor Manufacturing Technology, Industrial Quality & Research, Medical Technology und Consumer Markets erwirtschaftete die ZEISS Gruppe zuletzt einen Jahresumsatz von über 6,4 Milliarden Euro (Stand: 30.9.2019).
ZEISS entwickelt, produziert und vertreibt für seine Kunden hochinnovative Lösungen für die industrielle Messtechnik und Qualitätssicherung, Mikroskopielösungen für Lebenswissenschaften und Materialforschung sowie Medizintechniklösungen für Diagnostik und Therapie in der Augenheilkunde und der Mikrochirurgie. ZEISS steht auch für die weltweit führende Lithographieoptik, die zur Herstellung von Halbleiterbauelementen von der Chipindustrie verwendet wird. ZEISS Markenprodukte wie Brillengläser, Fotoobjektive und Ferngläser sind weltweit begehrt und Trendsetter.
Mit diesem auf Wachstumsfelder der Zukunft wie Digitalisierung, Gesundheit und Industrie 4.0 ausgerichteten Portfolio und einer starken Marke gestaltet ZEISS den technologischen Fortschritt mit und bringt mit seinen Lösungen die Welt der Optik und angrenzende Bereiche weiter voran. Grundlage für den Erfolg und den weiteren kontinuierlichen Ausbau der Technologie- und Marktführerschaft von ZEISS sind die nachhaltig hohen Aufwendungen für Forschung und Entwicklung.
Mit über 31.000 Mitarbeitern ist ZEISS in fast 50 Ländern mit rund 30 Produktionsstandorten, 60 Vertriebs- und Servicestandorten sowie 25 Forschungs- und Entwicklungsstandorten weltweit aktiv. Hauptstandort des 1846 in Jena gegründeten Unternehmens ist Oberkochen, Deutschland. Alleinige Eigentümerin der Dachgesellschaft, der Carl Zeiss AG, ist die Carl-Zeiss-Stiftung, eine der größten deutschen Stiftungen zur Förderung der Wissenschaft.
Weitere Informationen unter www.zeiss.de
Über TRUMPF
Das Hochtechnologieunternehmen TRUMPF bietet Fertigungslösungen in den Bereichen Werkzeugmaschinen und Lasertechnik. Die digitale Vernetzung der produzierenden Industrie treibt das Unternehmen durch Beratung, Plattform- und Softwareangebote voran. TRUMPF ist Technologie- und Marktführer bei Werkzeugmaschinen für die flexible Blechbearbeitung und bei industriellen Lasern.
2019/20 erwirtschaftete das Unternehmen mit rund 14.300 Mitarbeitern einen Umsatz von 3,5 Milliarden Euro (vorläufige Zahlen). Mit mehr als 70 Tochtergesellschaften ist die Gruppe in fast allen europäischen Ländern, in Nord- und Südamerika sowie in Asien vertreten. Produktionsstandorte befinden sich in Deutschland, Frankreich, Großbritannien, Italien, Österreich und der Schweiz, in Polen, Tschechien, den USA, Mexiko, China und Japan.
Weitere Informationen über TRUMPF finden Sie unter: www.trumpf.com
Über Fraunhofer
Die Fraunhofer-Gesellschaft mit Sitz in Deutschland ist die weltweit führende Organisation für anwendungsorientierte Forschung. Mit ihrer Fokussierung auf zukunftsrelevante Schlüsseltechnologien sowie auf die Verwertung der Ergebnisse in Wirtschaft und Industrie spielt sie eine zentrale Rolle im Innovationsprozess. Als Wegweiser und Impulsgeber für innovative Entwicklungen und wissenschaftliche Exzellenz wirkt sie mit an der Gestaltung unserer Gesellschaft und unserer Zukunft. Die 1949 gegründete Organisation betreibt in Deutschland derzeit 74 Institute und Forschungseinrichtungen. Rund 28 000 Mitarbeiterinnen und Mitarbeiter, überwiegend mit natur- oder ingenieurwissenschaftlicher Ausbildung, erarbeiten das jährliche Forschungsvolumen von 2,8 Milliarden Euro. Davon fallen 2,3 Milliarden Euro auf den Leistungsbereich Vertragsforschung.
Das Vorschlagsrecht zum Deutschen Zukunftspreis obliegt den führenden deutschen Einrichtungen aus Wissenschaft und Wirtschaft sowie Stiftungen.
Das Projekt „EUV- Lithographie – neues Licht für das digitale Zeitalter“ wurde von der Fraunhofer-Gesellschaft e.V. eingereicht.
Bundespräsident Frank Walter Steinmeier überreicht am 25. November 2020 den 24. Deutschen Zukunftspreis am eines der drei nominierten Teams.
Präsentation des Projektes Abendveranstaltung, 09. September 2020
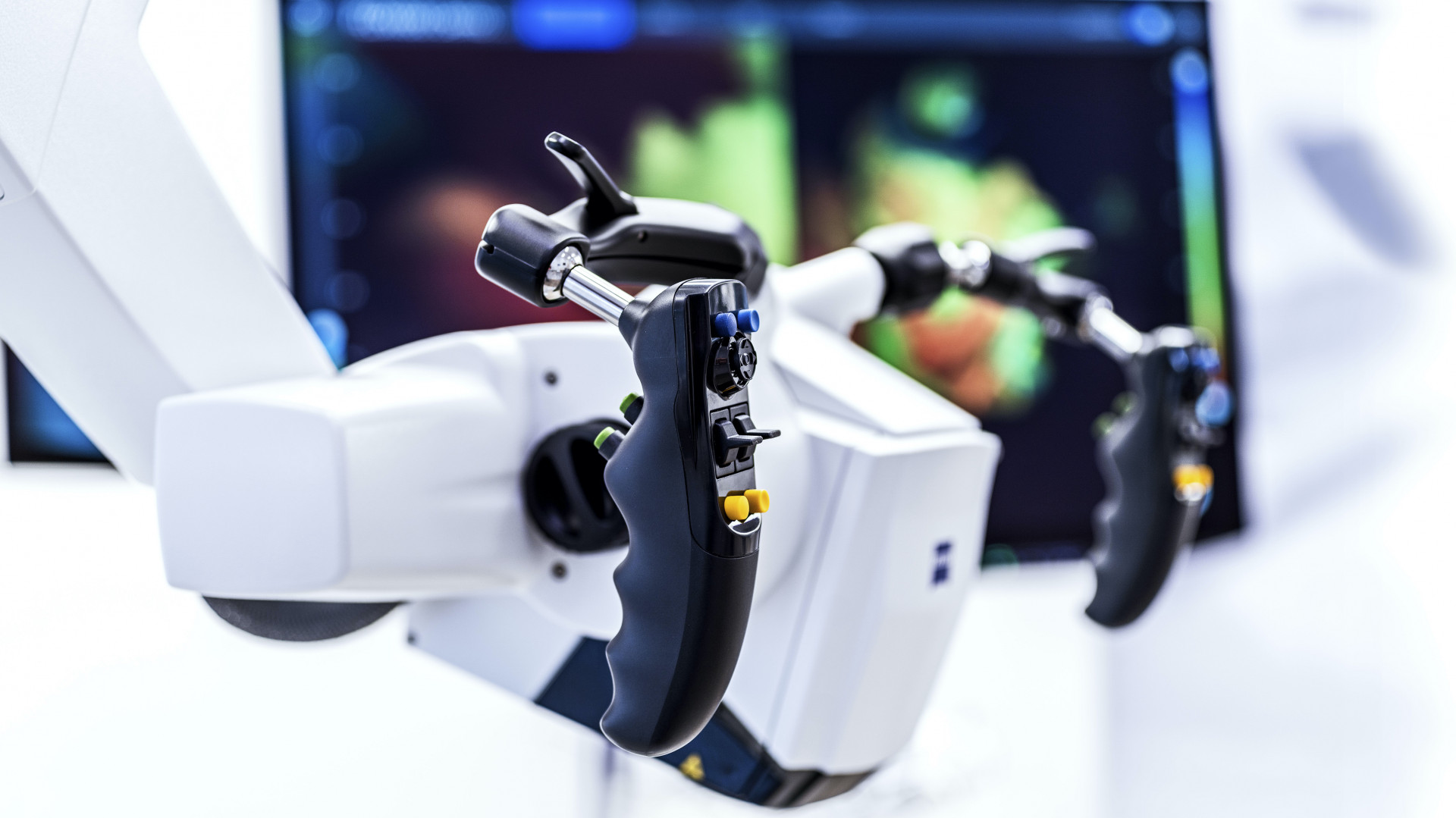